Drag Race

Back in the ’60s, a youthful Barry Wallner was well known in and around Illinois for his modified ’57 sedan delivery. It was a tough competitor at the local dragstrips, but time took its toll, and most of the dragstrips have disappeared, giving way to housing and shopping-center developments and industrial complexes. But this hasn’t stopped Wallner, who was an adept restorer. So, from the late-’60s through the mid-’90s, he has gone on with other ’57 Chevys to win top show awards.

Once a West Coast gasser, this ’55 Chevy made its way to Lebanon, Ohio, thanks to longtime Chevy enthusiast Freddie Green. That was back in 1978, when his son Jason was just four years old. Fast forward a few years, and Jason, professing to be a Chevy man since birth, took ownership of the car from his father at the age of 10.

At first, it appeared as though the bright red Mustang didn’t have an engine in it, but once the seller, Eric Rizner, opened the hood, Holden and Wunsch could plainly see that the engine had been set back in the chassis. Was this the elusive Mustang “racecar” that Holden had been looking for?
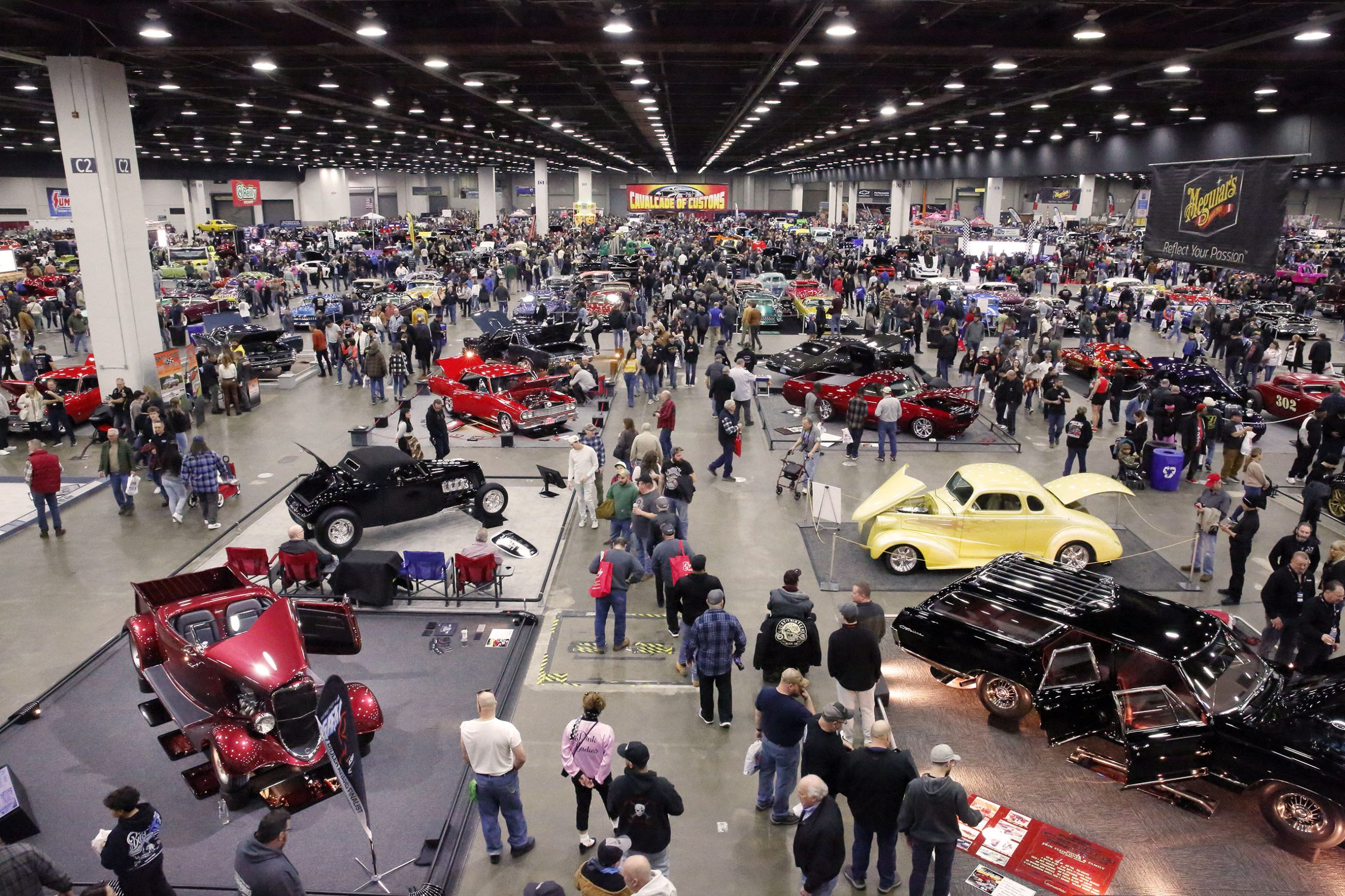
A Celebration of Automotive Passion Author Walking into the Madness Step through the doors, and bam—you’re hit with row after row of mind-blowing builds. Right off the bat, Barbie’s pink Cadillac Convertible was stealing the show, proving that even a toy-inspired cruiser can have serious presence. Then there was the Mega Morph Giant Transforming Robot Car—because why not? Nothing says Autorama like a car that can shape-shift. The 2025 Ridler Award Winner and the Great 8 The 2025 Ridler Award went to a beast of a build—Gray Madder, a killer 1955 Chevy Nomad that took things to a whole new level. Built by Southern Comfort Customs, this thing is pure automotive perfection, with flawless bodywork, a rowdy LS3 engine, and custom details that had the crowd losing their minds. But don’t get it twisted—the rest of the Great 8 weren’t exactly slouches. We’re talking about high-end restorations and wild, out-of-this-world customs that brought serious heat, proving once again that if you want to make it in this game, you better bring everything you’ve got. History, Horsepower, and Pure Creativity One of the coolest things about Autorama is the mix of styles, and this year was no different. A 1941 Buick Special, complete with a bullet hole from Pearl Harbor—yeah, you read that right—brought some serious history to the show floor. Then there was the 1951 Mercury done up like a NASCAR stocker, making the trek all the way from Austria just to drop jaws. Why Autorama is Pure Magic Detroit Autorama isn’t just another car show—it’s a full-blown tribute to the obsession, creativity, and hardcore wrenching that makes car culture what it is. Whether you’re into pristine classics, wild customs, or off-the-wall builds that make zero sense but totally work, this show had it all. And as the doors closed on another epic year, one thing was clear: 2025 was a banger, and we’re already counting the days ‘til next year.
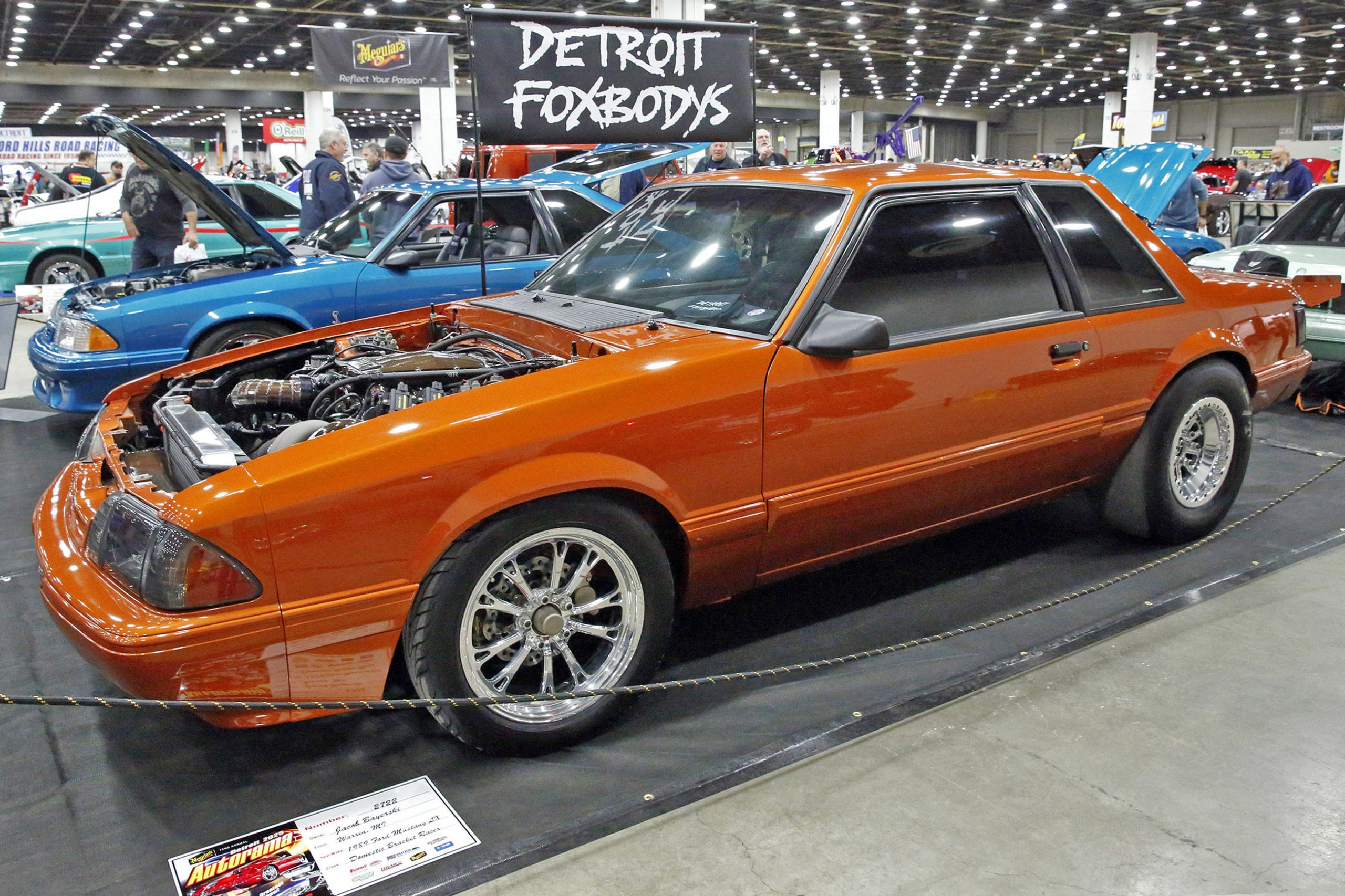
The Detroit Autorama—America’s Greatest Hot Rod Show—once again delivered the goods, and this year, the Detroit Foxbody Car Club rolled in strong. If you were there, you know. If you weren’t, well, you missed one hell of a display from a crew that knows how to build, drive, and talk Fox Bodies like nobody else.
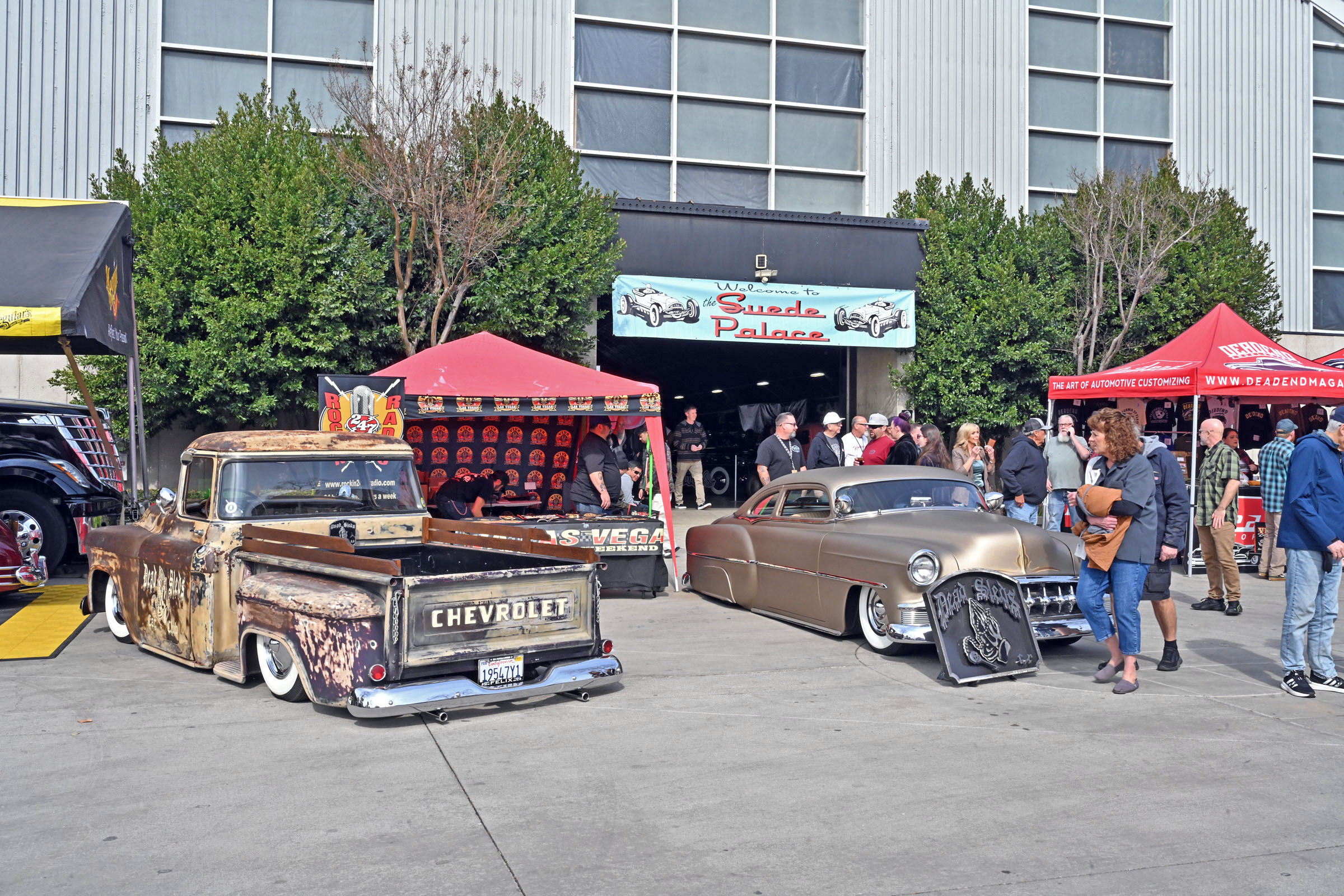
The Suede Palace at the 2025 Grand National Roadster Show was, as always, the ultimate hotspot for anyone who lives and breathes traditional hot-rodding. Tucked into Building 10 of the Pomona Fairplex, this gathering wasn’t about high-dollar billet builds or over-polished show queens—it was a raw, authentic tribute to the early days of hot-rodding, where creativity, attitude, and a little grease under the fingernails mattered more than a six-figure paint job.
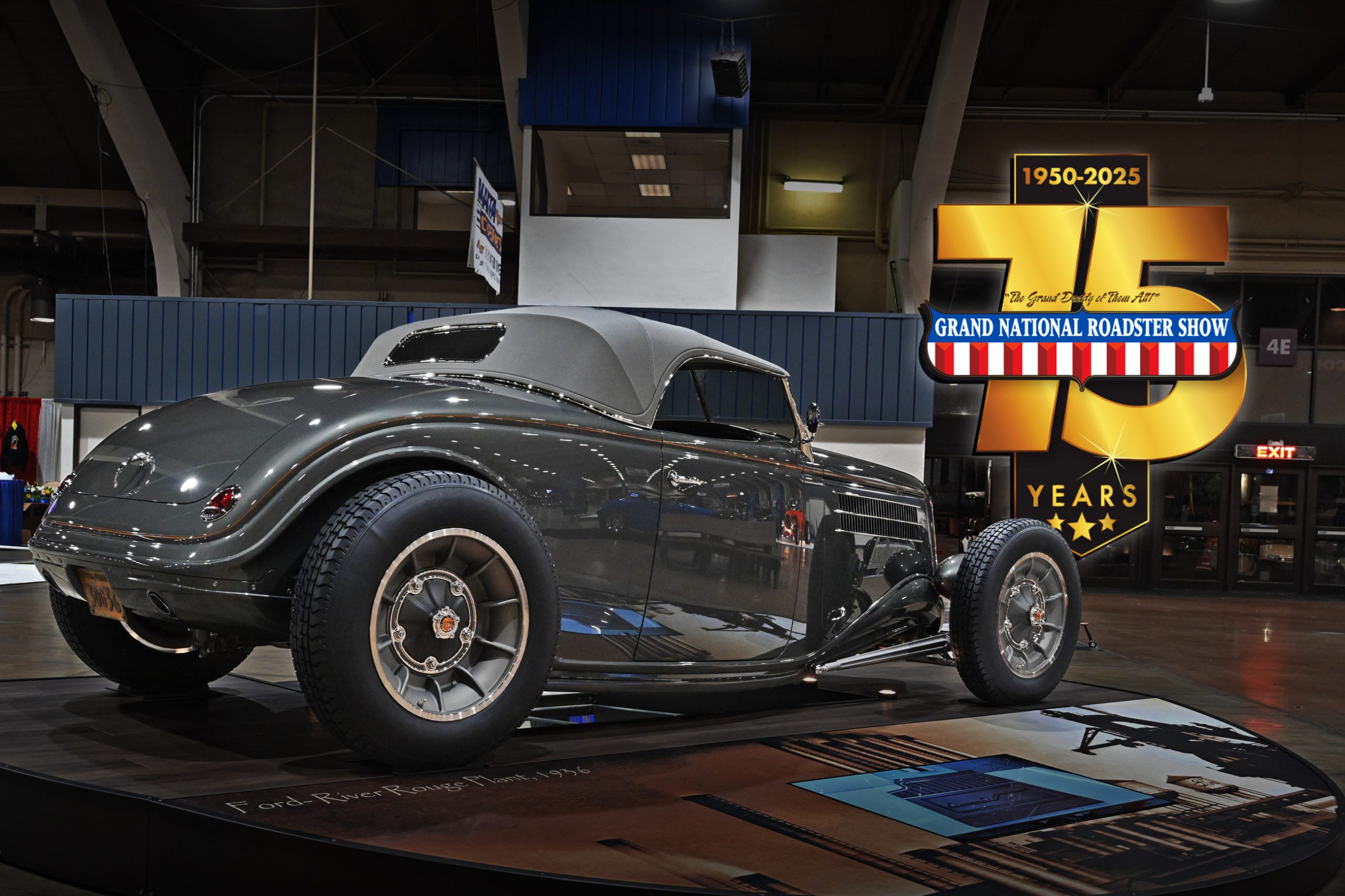
The 75th annual O’Reilly Auto Parts Grand National Roadster Show, presented by Meguiar’s, once again proved why it’s the crown jewel of indoor car shows. From January 31 to February 2, the Pomona Fairplex was loaded with the meanest, cleanest roadsters in the country, all gunning for the top prize: the America’s Most Beautiful Roadster (AMBR) Award. This wasn’t just some polished-up car show—this was a throwdown of craftsmanship, power, and pure hot rod passion.
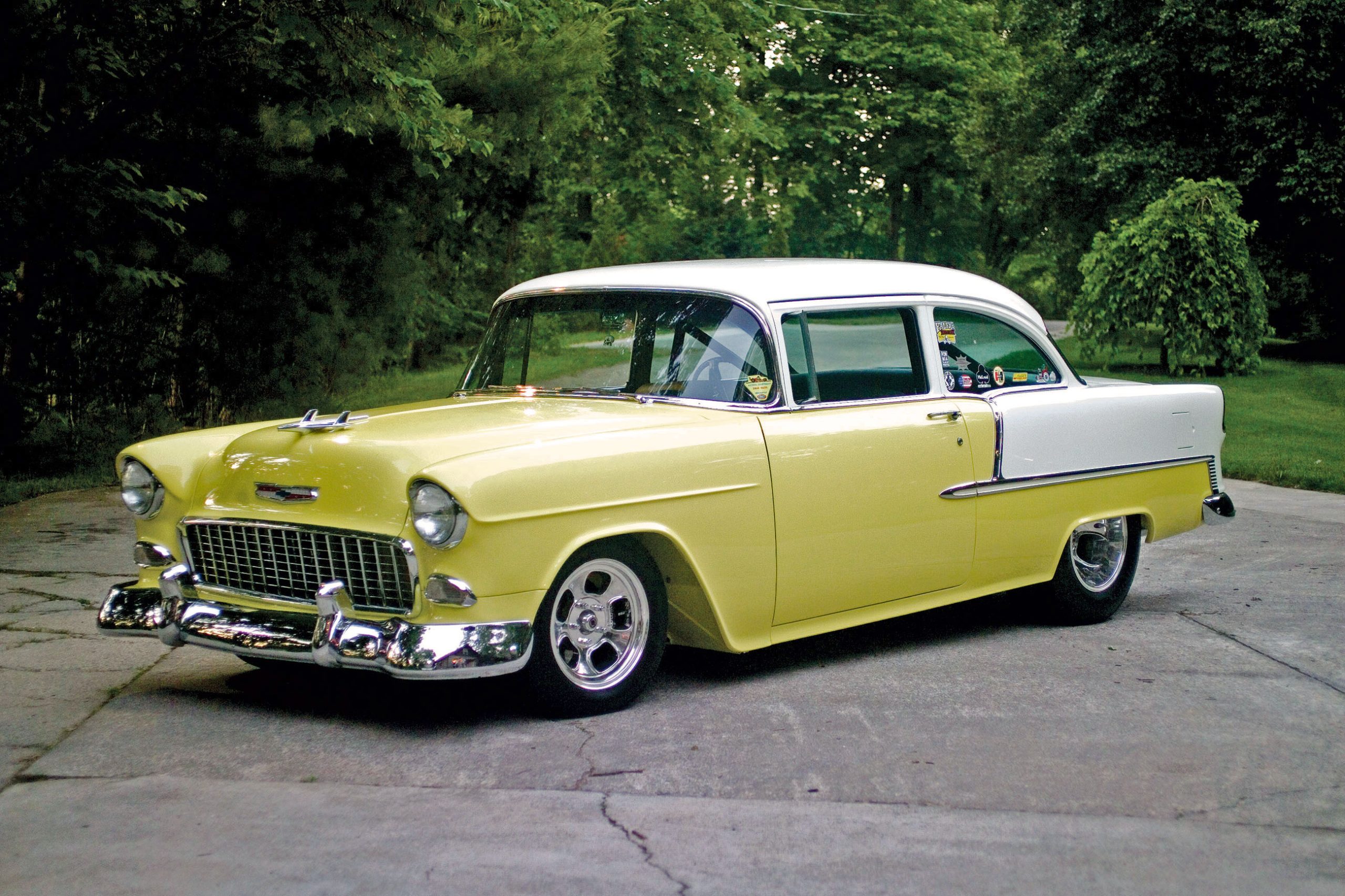
As we’ve come to learn, there’s something special about a ’55 Chevy, particularly when it is fitted with one of the popular Chevy engines that have become so common today. But that’s not the case when the hood is opened on this ’55. It is not the celebrated 265, or one of the more respected LS engines, or even a Chevy big block that captures your attention here. This is something different, and not a Bow Tie at all.
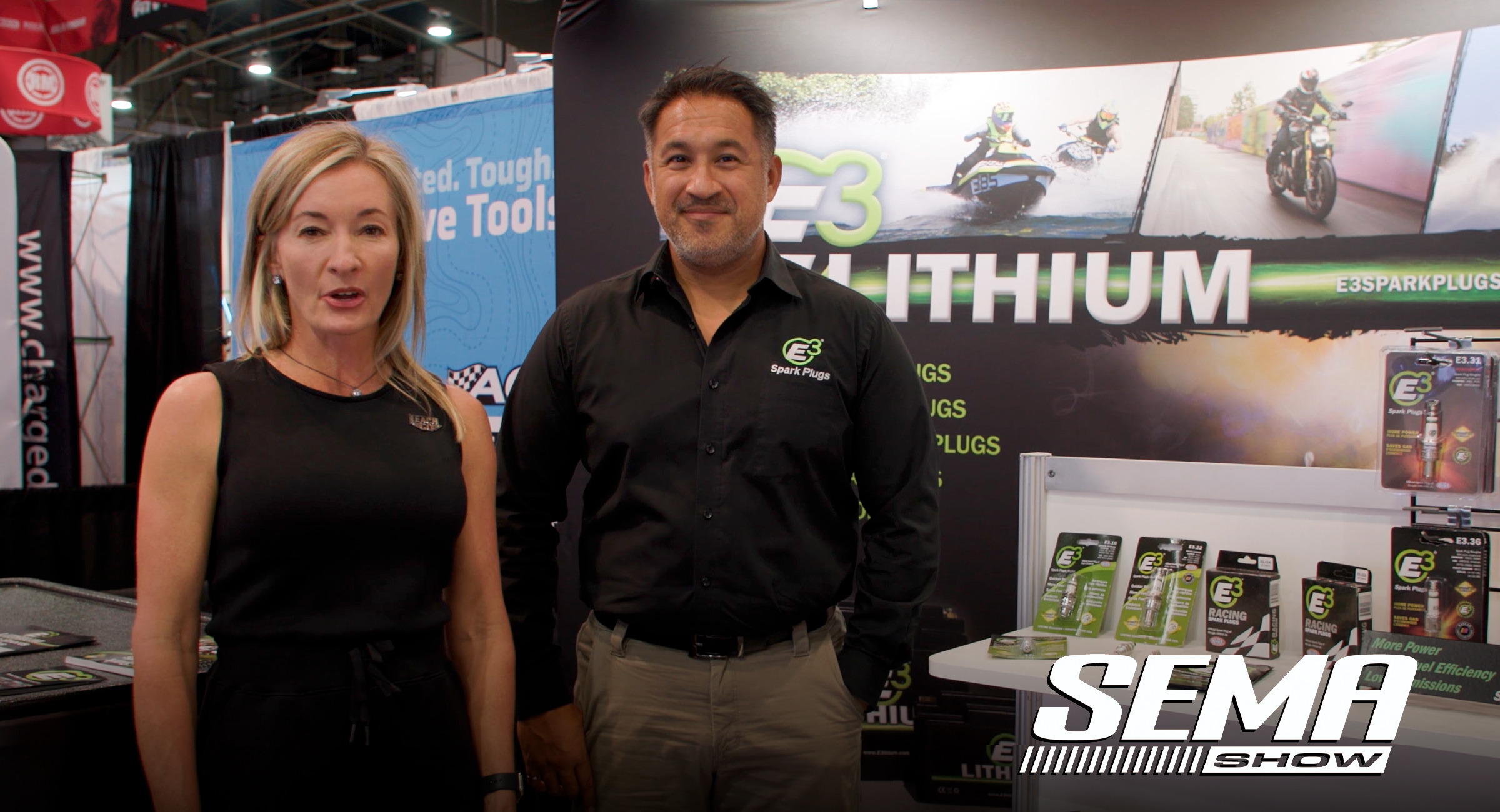
Dive into our exclusive coverage recorded LIVE from the SEMA 2024 show floor. From groundbreaking performance enhancements to next-generation customization tools, each moment is brimming with ideas and inspiration from the pros who are shaping the future of automotive innovation. Whether you’re a seasoned professional or a car enthusiast eager to discover the next big thing, The Auto Builder’s live showcase offers an unrivaled experience. Witness the passion, creativity, and expertise that make SEMA the pinnacle of automotive excellence. Catch the highlights now and immerse yourself in the excitement of automotive innovation like never before!
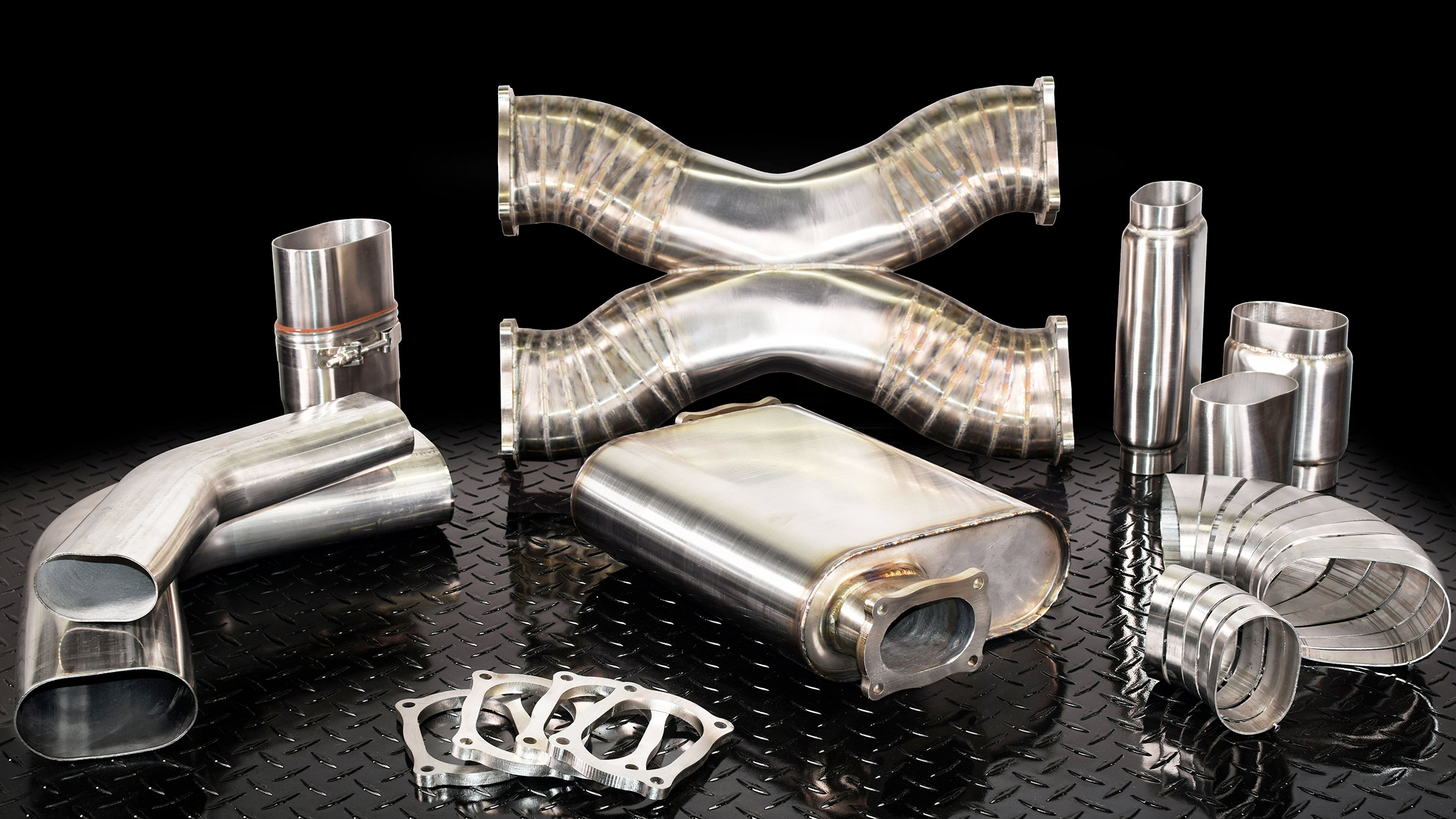
When it comes to squeezing every ounce of power and performance out of your ride, the details make the difference. Headers and mufflers might steal the show, but let’s not overlook a serious player in the game: oval exhaust tubing. And if you’re in the know, you’ve probably heard of Stainless Headers Mfg. Inc.—a company we respect for their top-notch craftsmanship and American-made quality.