Exterior
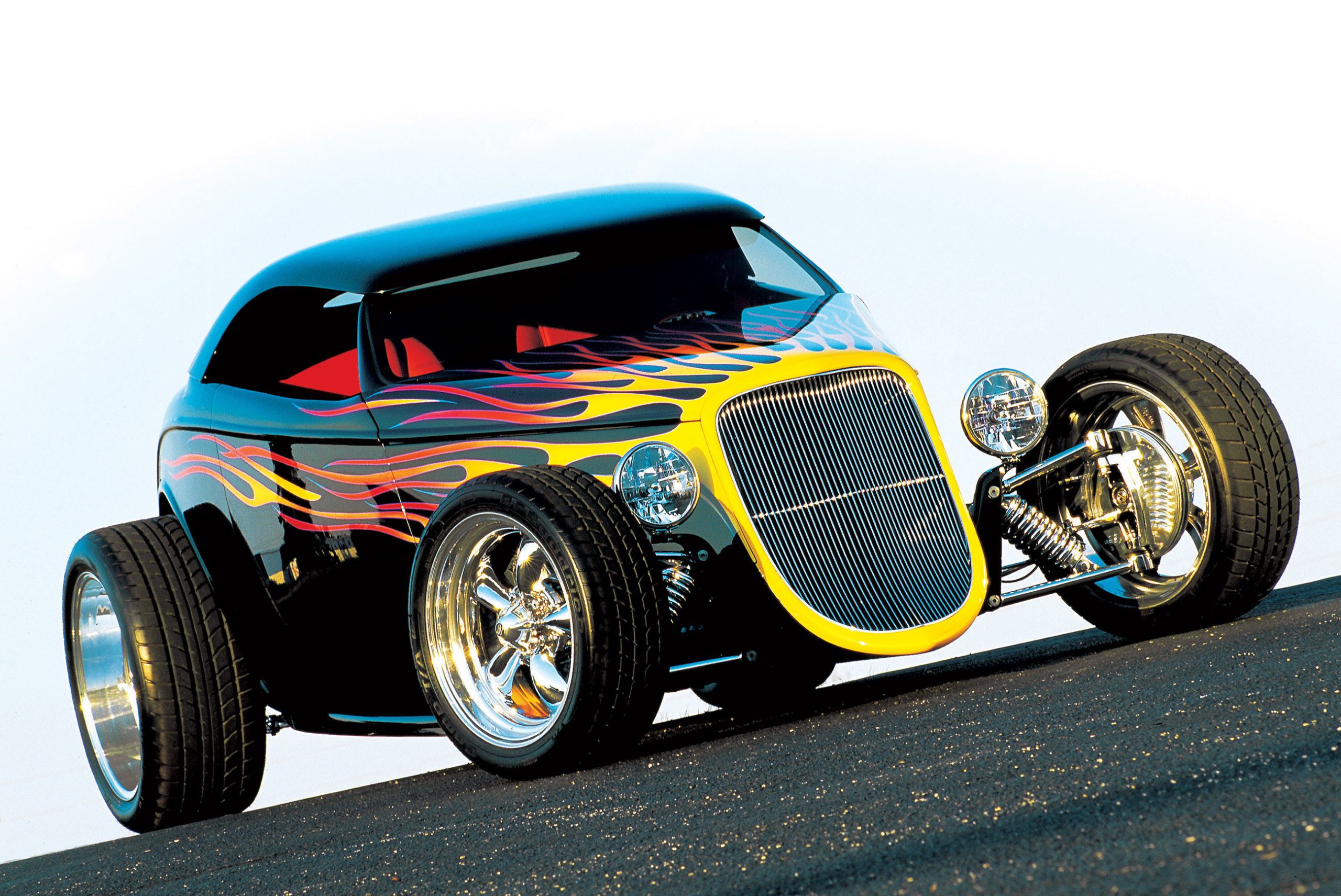
Alloway has built a lengthy succession of exciting cars, each with its own style, and all with a level of detailing that is a trademark of Alloway’s creations. This kind of finish work has earned him the coveted Ridler Award, along with every honor and title that one could garner from this hobby.
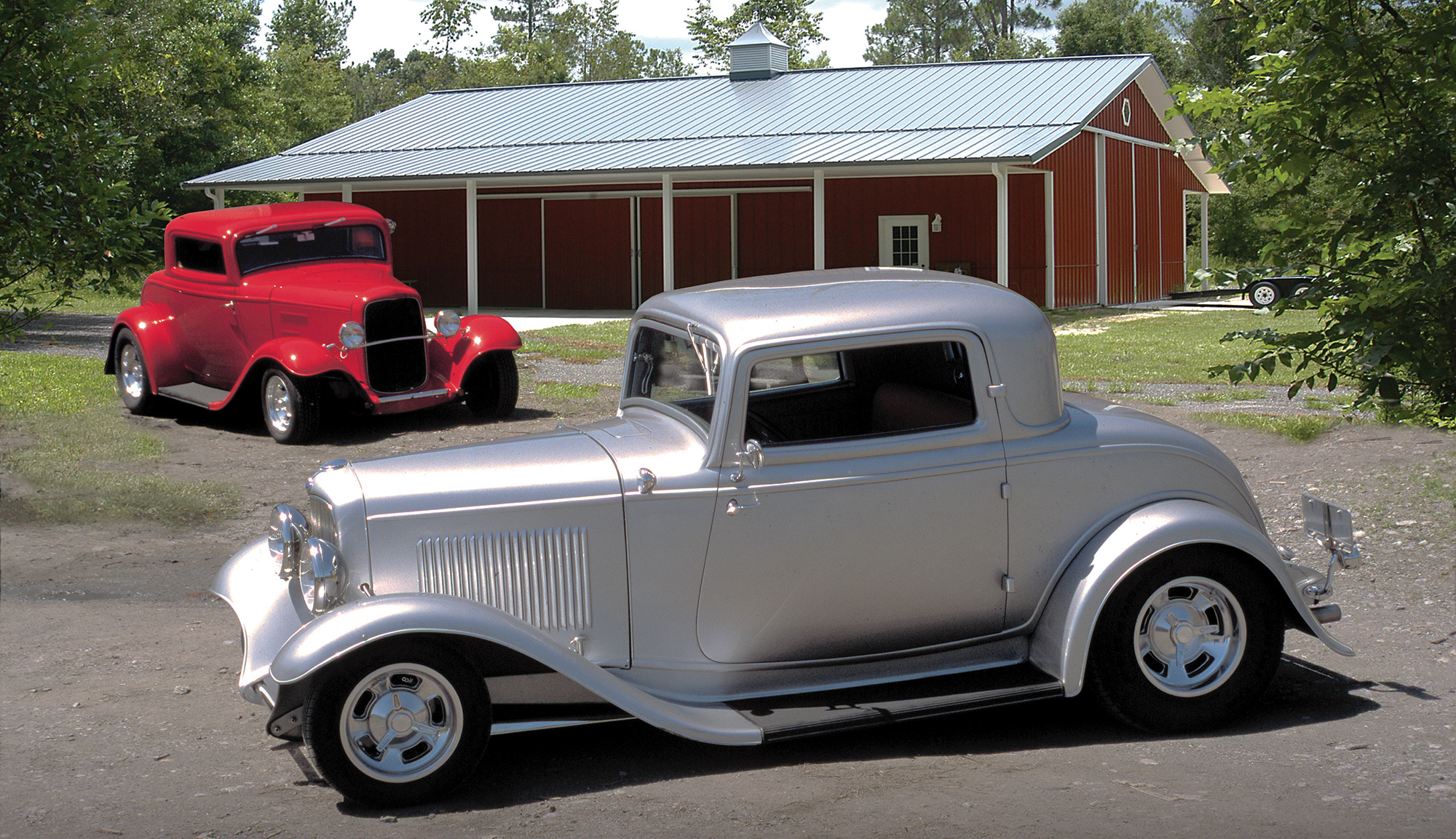
Hardcore rodders have a history of searching for vintage tin, even though the number of old cars (and trucks) sitting behind barn doors, in fields, under tarps and alongside garages has dwindled as interest has increased. This steady decline of available vintage steel is the very reason why so many businesses presently produce fiberglass and steel reproduction bodies and body parts.
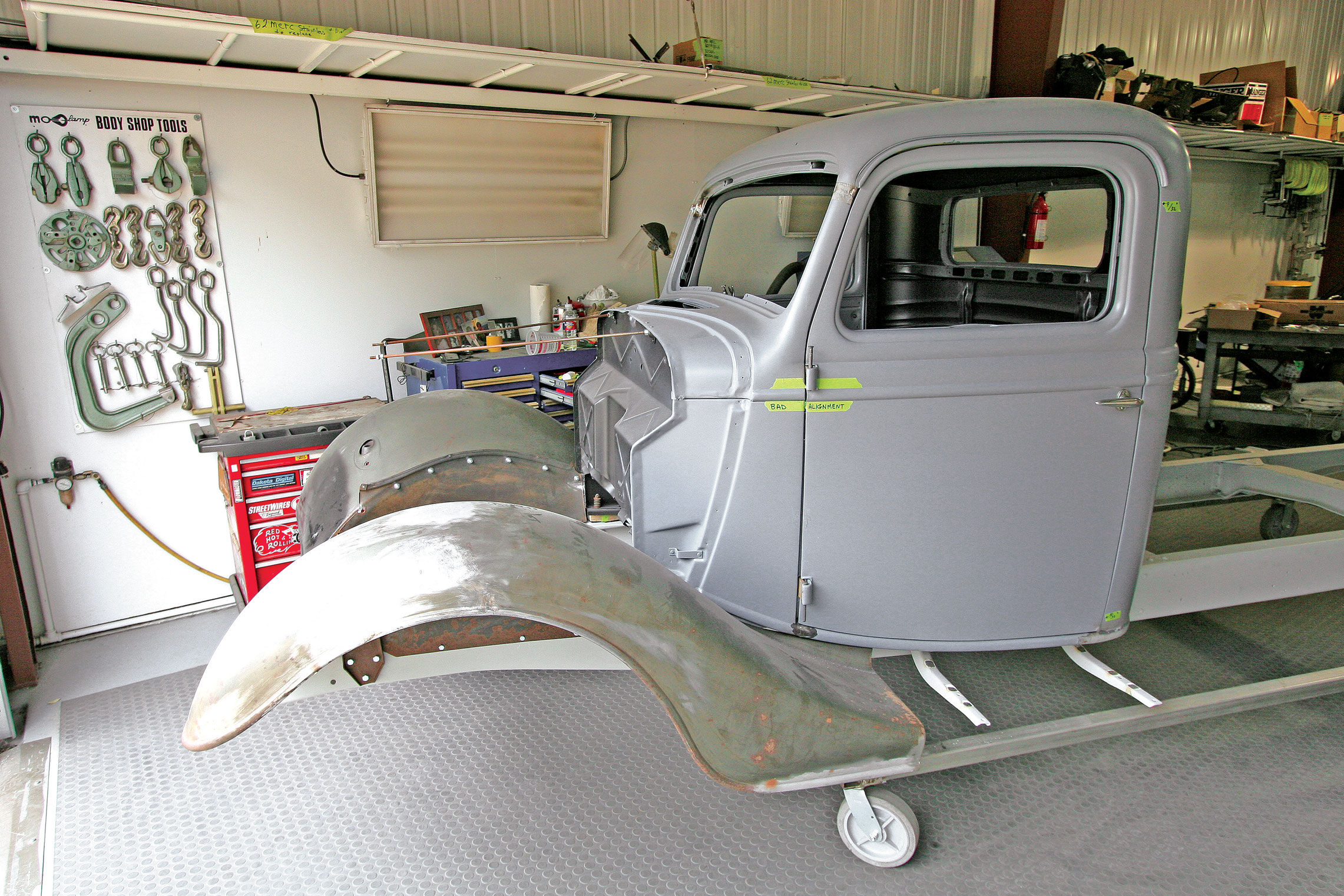
Pickup trucks from the ’30s were never meant to be high-quality hot rods, but several builders, including Jeff Lilly Restorations, are ready to change that theory. Lots of beater trucks are being built and driven frequently, and it’s great to see some of the cool ideas that come from these old farm or service trucks. Pickups are hot right now, and while some rodders are using low-gloss paint for their final coatings, many opt for a super-slick appearance with precision gaps and laser-straight panels.
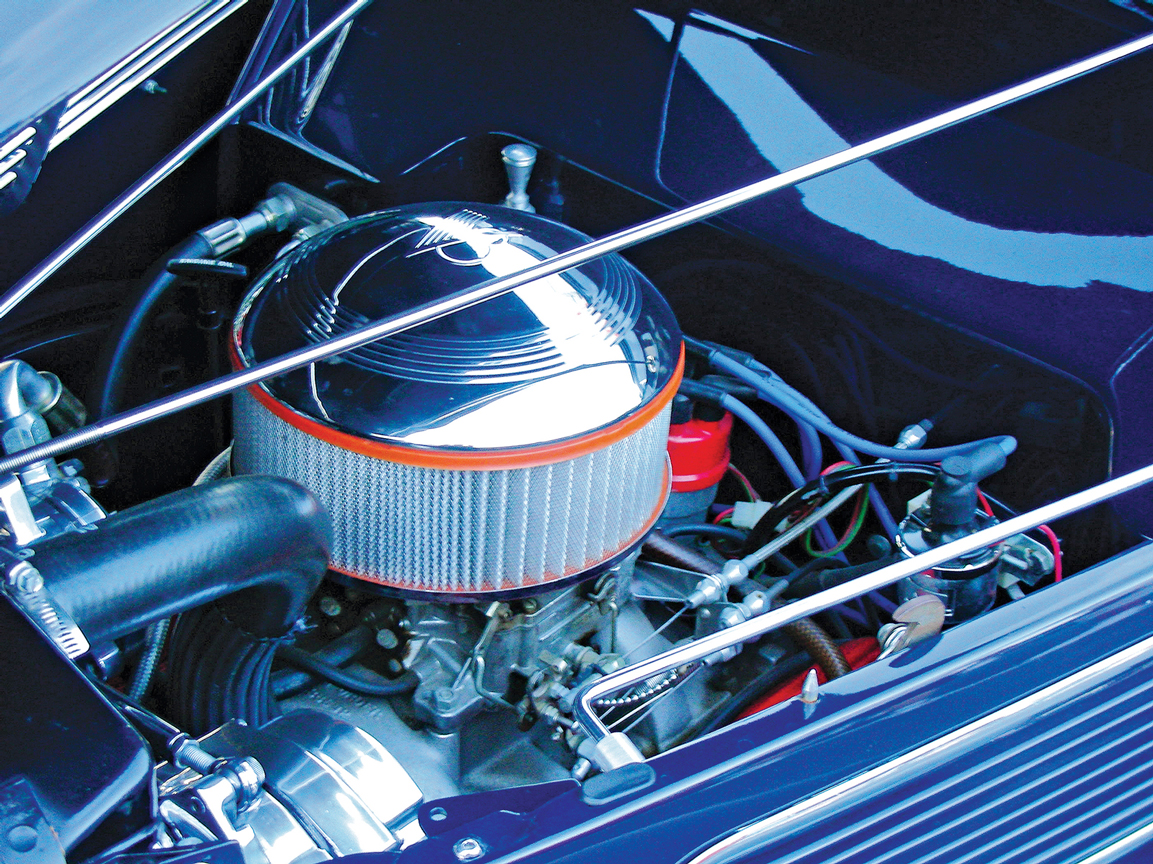
Call ’em tech tips, building tips, details or whatever you like, but this is the stuff we see at events and shows while shooting features or doing shop tours, not to mention things we’ve discovered while working in our own shops. It’s like when you’re foot-cruising an event with the boys and pointing things out to each other, or when you have a stroke of genius while working on your own project.
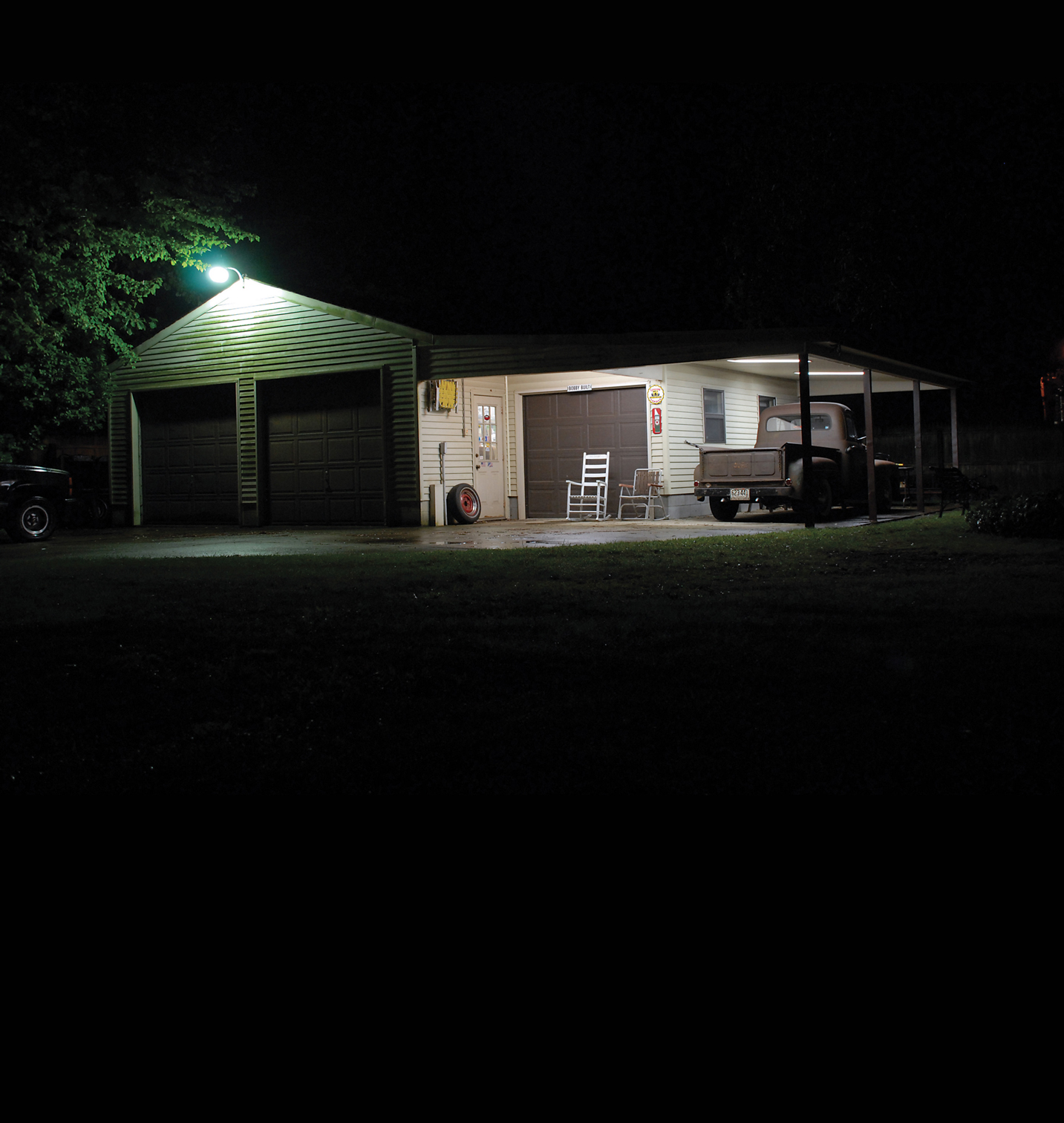
We always find it amusing when a bench racing session turns to building street rods. It seems there is a huge contingency of rodders and observers of street rodding who believe that every car in the fairgrounds area was built by a professional shop. We’re not about to argue the point that a lot of people now pay to have work done on their cars, whether it’s chassis work, bodywork or upholstery. However, there is still a large group of people who spend evenings and weekends out in the garage forming brackets, repairing rust, blocking panels and wiring hot rods. In short, they are building cars the old-fashioned way—at home with the help of a few friends.
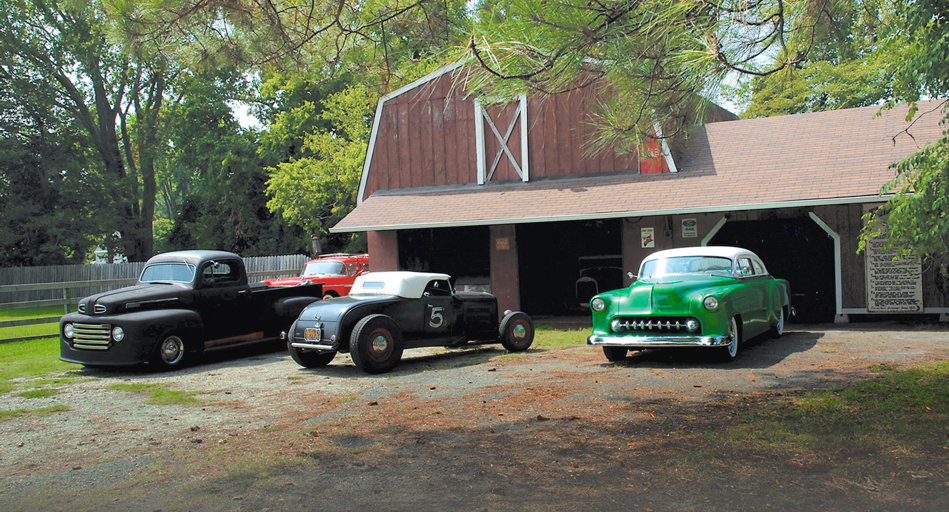
Jack Fuller has been at this hot rod game for a long time, and while he builds hot rods for a living, make no mistake—this is a man who loves his work. As a matter of fact, the mantra of the garage is, “When the fun stops, the doors close for good.” It’s pretty simple stuff, and oddly enough, that seems to be the specialty of the house—basic hot rods that look cool and work well. Jump in a Jack Fuller hot rod, and you’ll know it was designed to be driven. Jack’s own ’32 cabriolet has seen untold miles over the years, as have most of the other hot rods he has built.
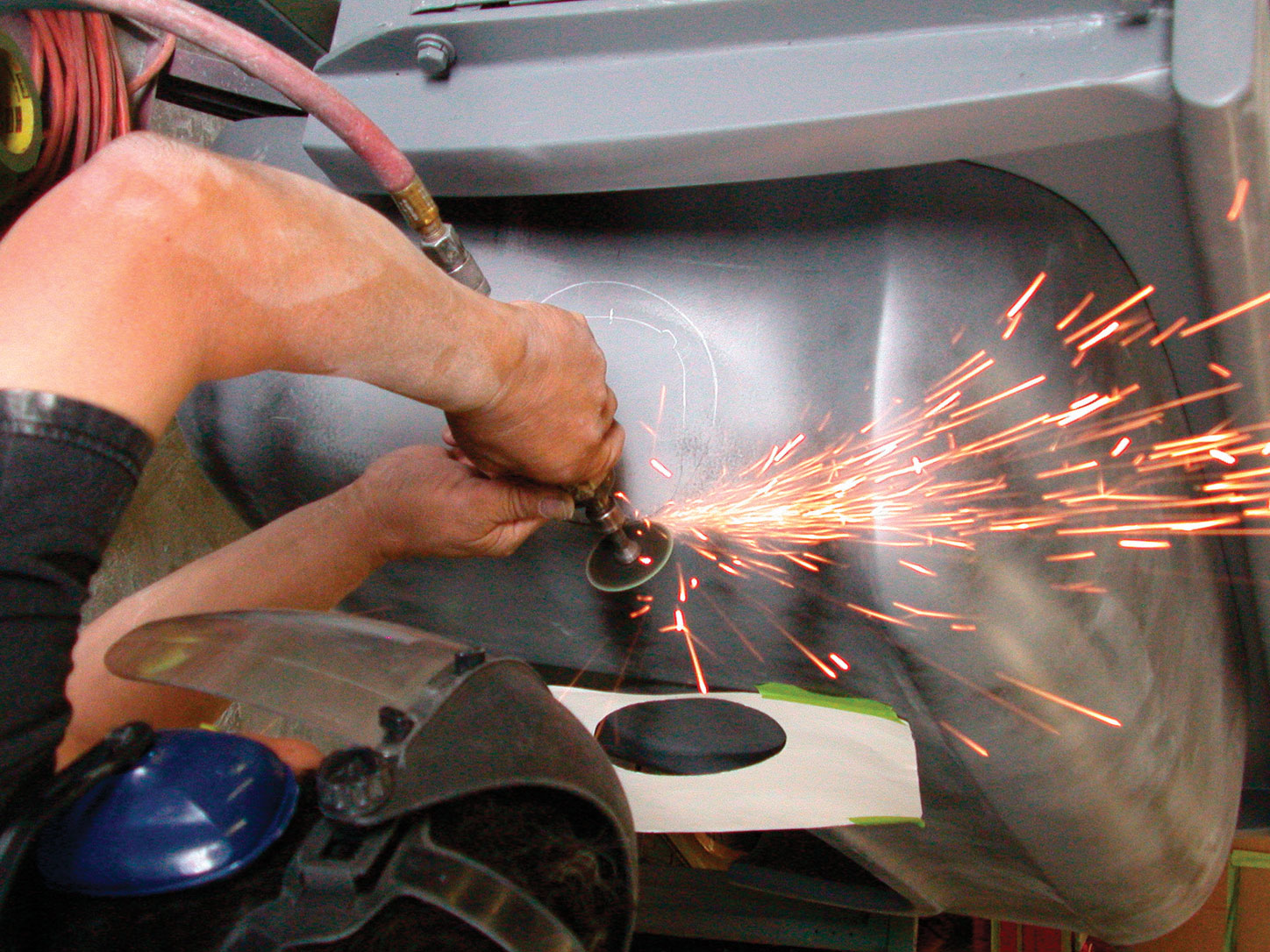
Always hard at work in the never-ending pursuit to do something just a little different, Darryl Nance and the crew at D&P Classic Chevrolet in Huntington Beach, California, recently added a pair of Chevy Cobalt taillights to one of the mid-’50s pickups that they have been working on. The Chevy is a frame-off project that was completed to exhibit all of the tricks that the D&P team can throw at it, and we were on hand when they installed the late-model lights to the old-time treasure.
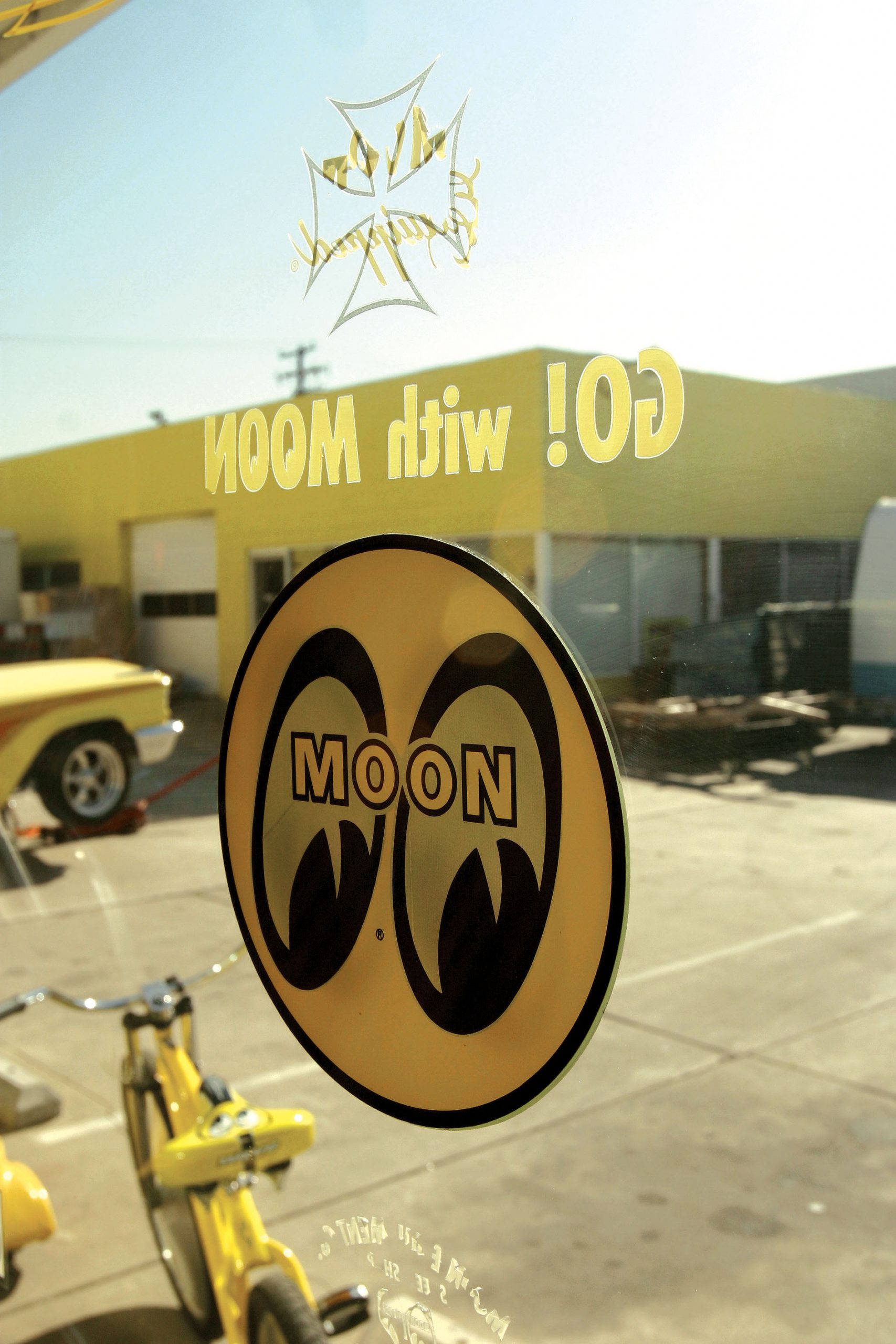
The showroom is what every auto parts store dreams of being: diced in checkerboard black and yellow tile with a heap of pegboard. Up front, the sales counter is the hub of business, fueled by eager customers that keep the phone ringing off the hook. Bob, Sam and Robin deal one-on-one with customers, keeping all 50 states Moon-equipped.
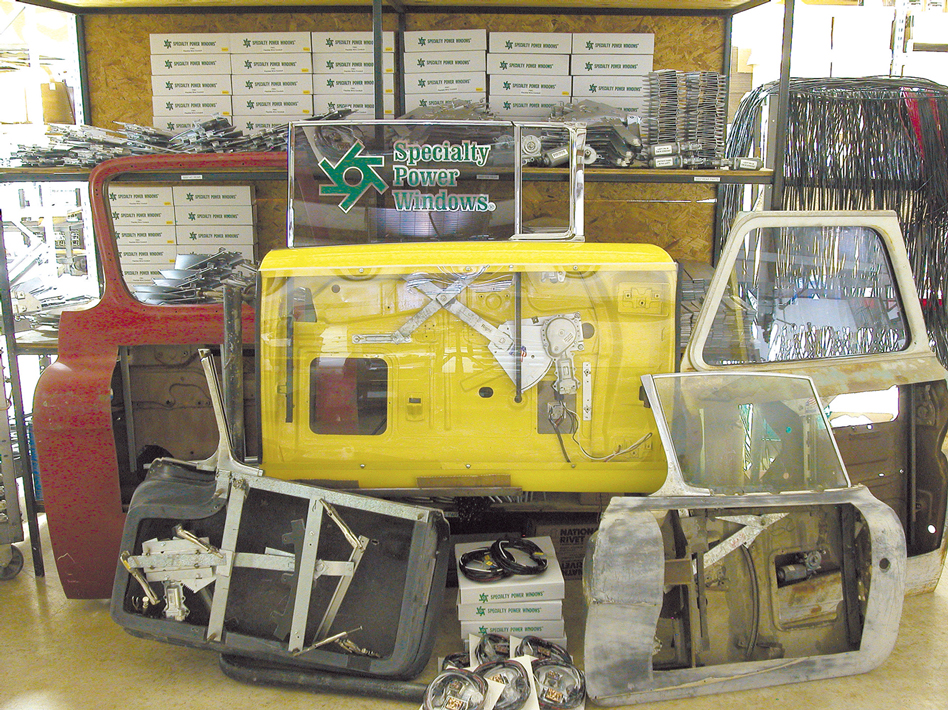
There was a time not all that long ago, between station wagons and SUVs, when big conversion vans were the family transportation of choice. In the beginning, the Big Three considered vans to be commercial vehicles, fitted with rubber floor mats, vinyl seats and short (if any) side windows, not the decked-out, posh family transport they would become.