Compact Cars
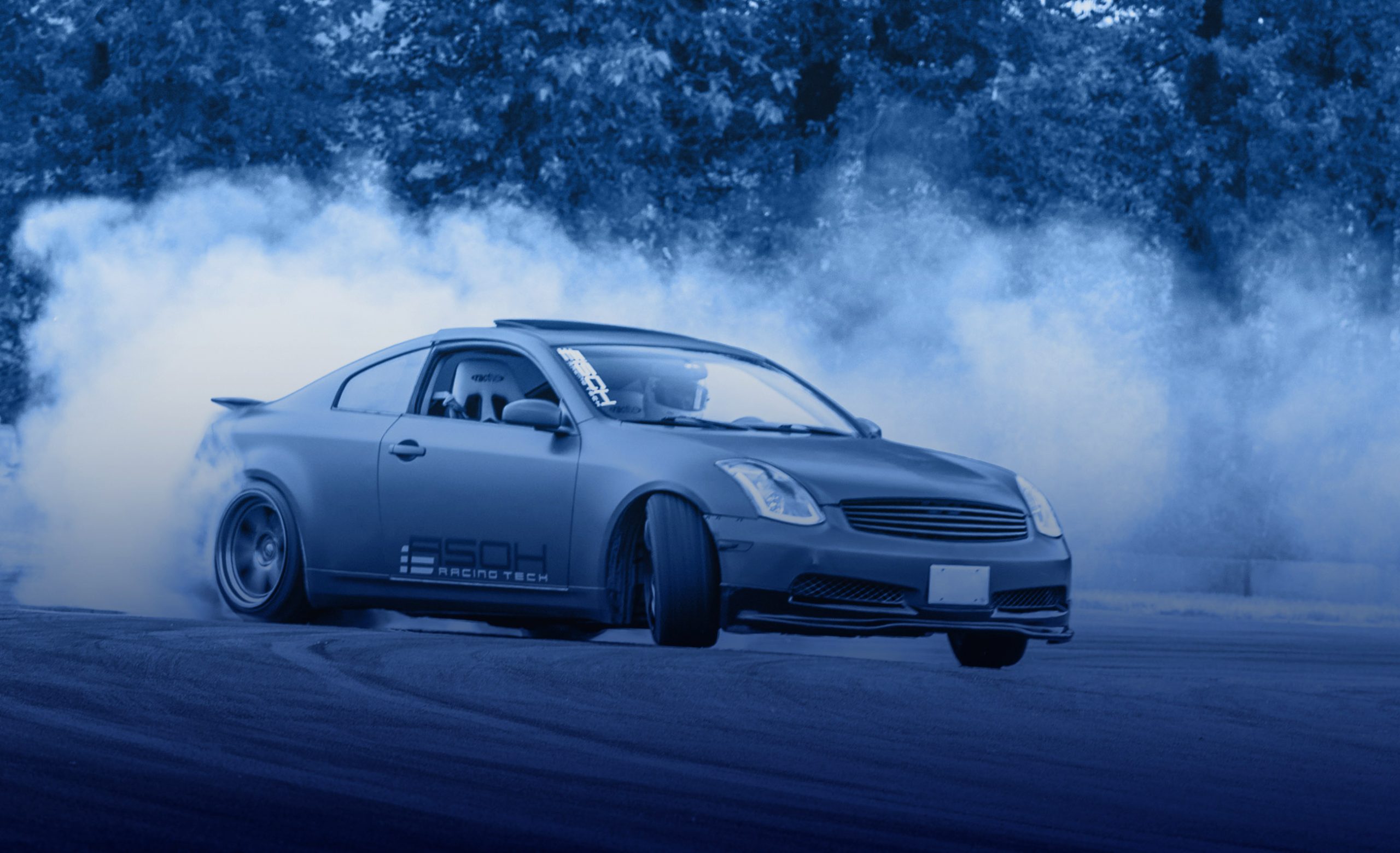
In the realm of high-performance automotive engineering, fuel flow reigns supreme as the lifeblood of optimal power delivery. DeatschWerks emerges as a game-changer with their Performance In-Tank Regulators, engineered to unleash the true potential of EFI engines.
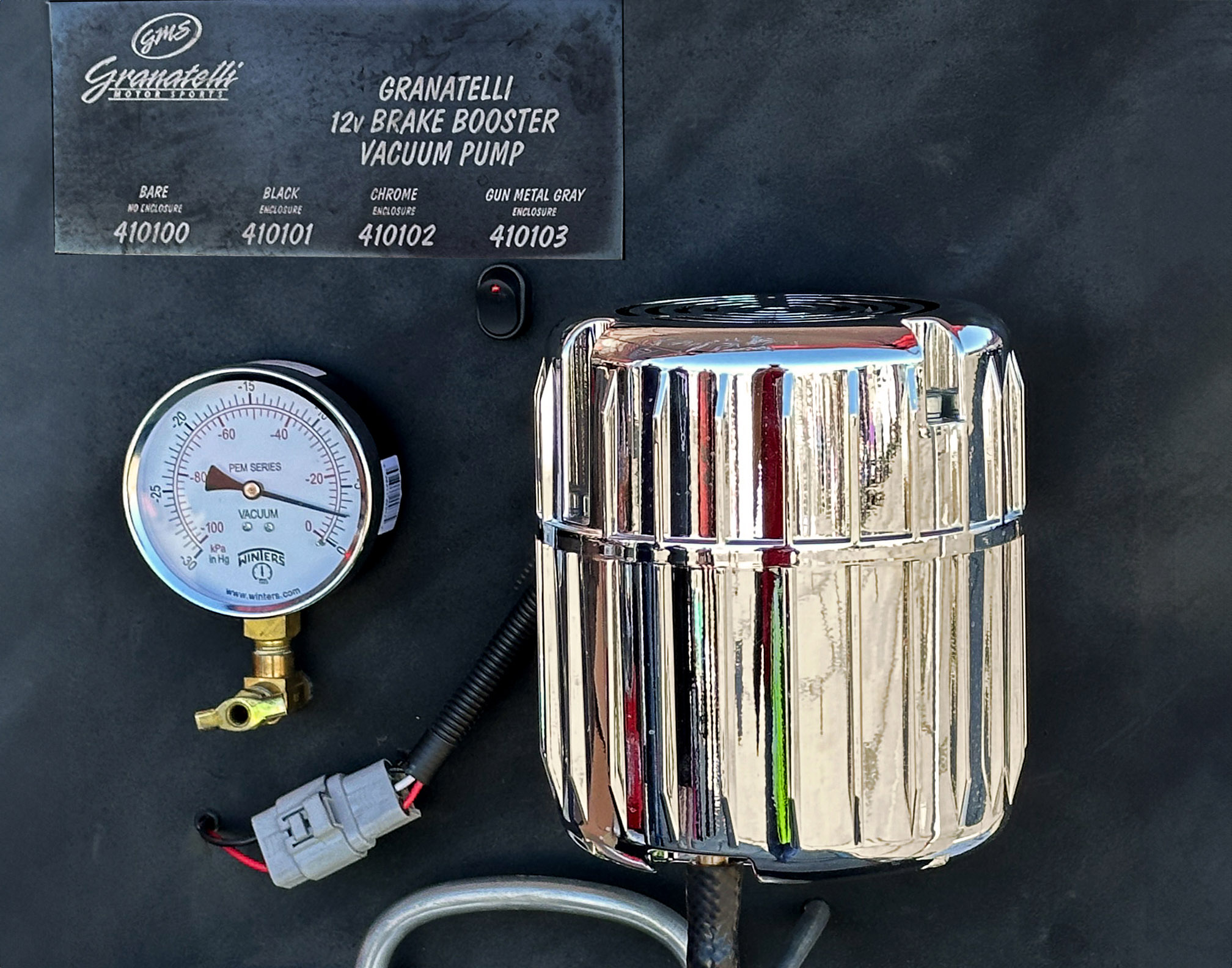
Rev up your engines and buckle up, folks, because Granatelli Motorsports is unleashing the ultimate solution to your vacuum woes with their 12V Electric Vacuum Pump Kit! Picture this: you’ve got your hot rod sitting pretty in the garage, but you’re struggling with power brakes, wipers, or engine management issues due to vacuum deficiencies. Well, fear not, because Granatelli has your back with their state-of-the-art kit, designed to tackle these challenges head-on and turbocharge your ride’s performance.
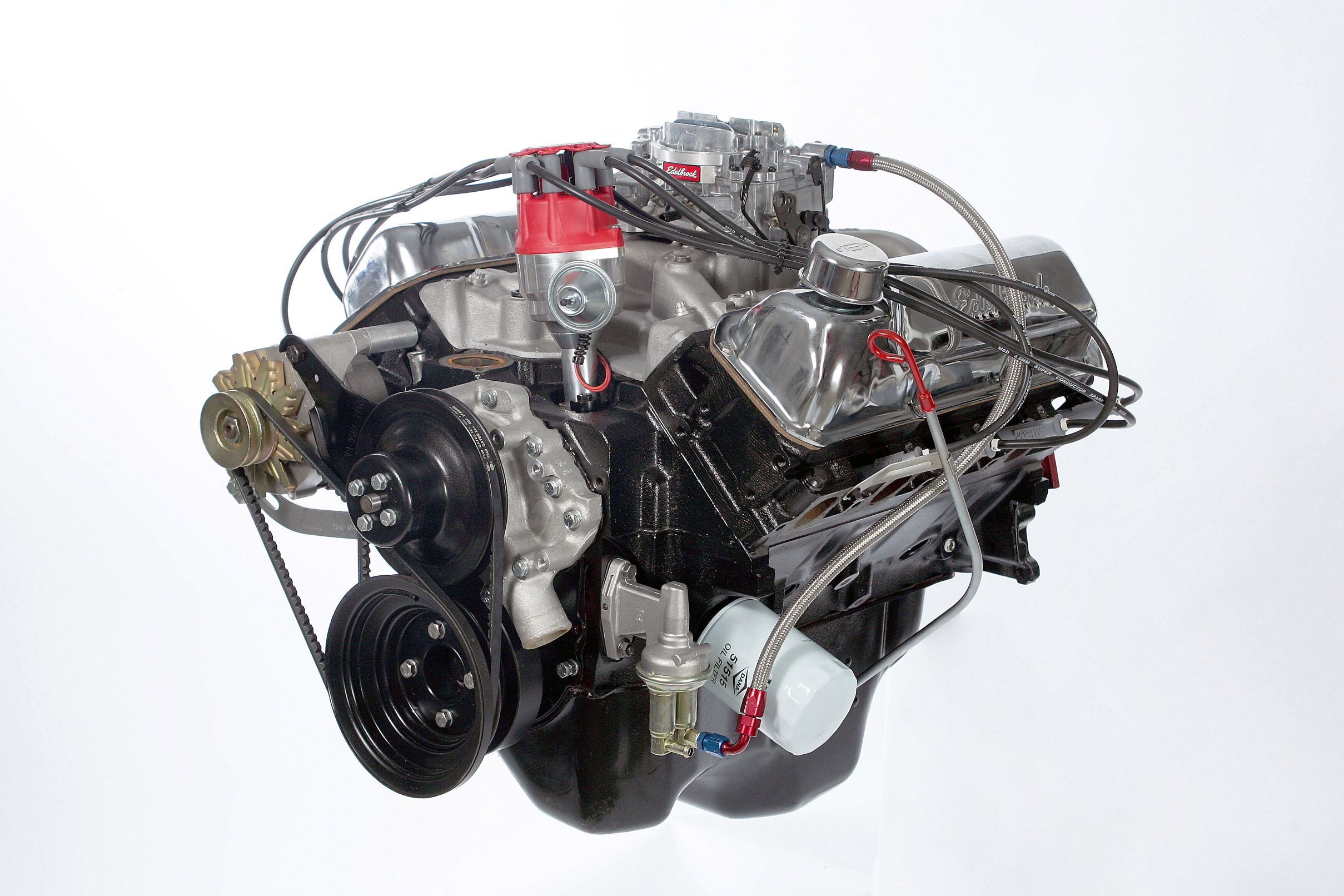
Ford fans will always have a soft spot in their blue-oval hearts for the Windsor, the Cleveland and the big 460 FE engines—and deservedly so. If you’ve ever crawled a junkyard for one of these engines, you’ve likely passed over more than a few 351M and 400 engines to find what you are looking for. Poor factory numbers and bad word-of-mouth have made these cousins to the mighty Cleveland about as wanted as poison ivy at a nudist colony, but there is power to be found in those engines—and cheap, too.
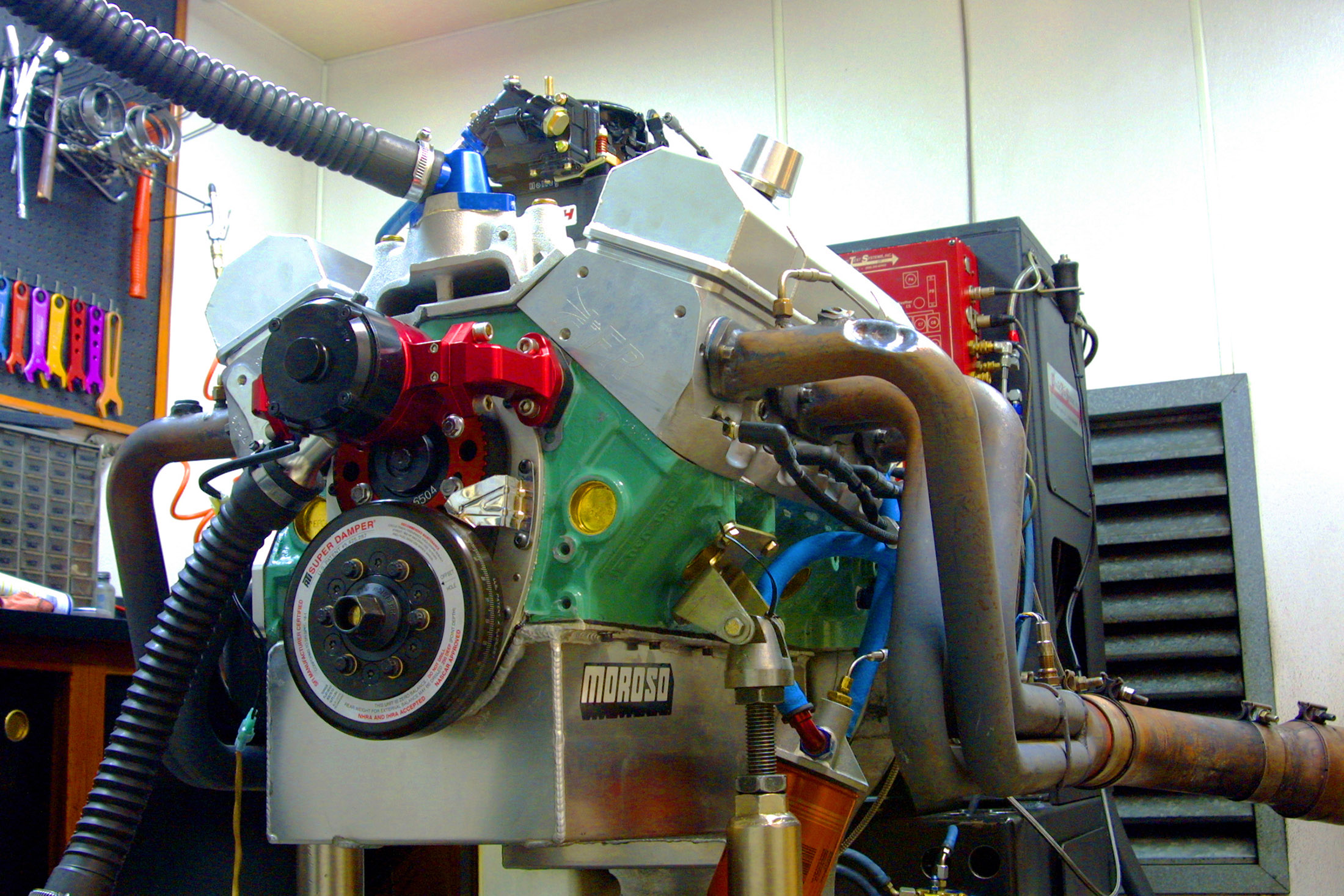
We showed you how to build a small-block engine that could make over 500 hp and 500 lb-ft of torque on 87-octane gas. It was a motor that could be driven just about every day with a hydraulic-roller cam and a good carburetor, making acquisition and maintenance almost nonexistent. Like many things we do in the engine world, the results we enjoyed—while good—just weren’t satisfying anymore. We wanted more.
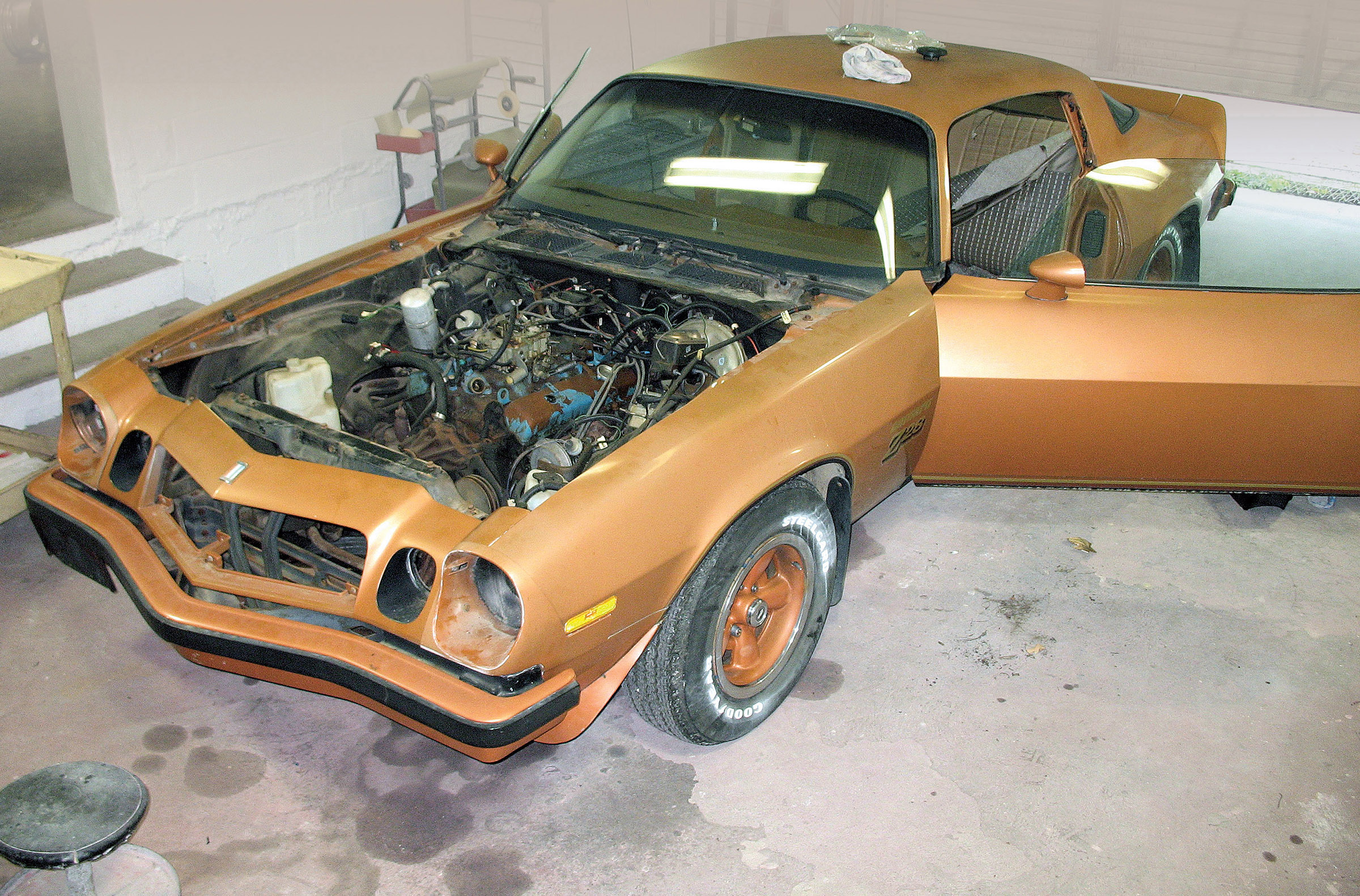
When starting any project that requires bodywork, rebuilding or even repainting, the first question is always, “What could possibly be lurking under the old paint that could come back and haunt us later?”
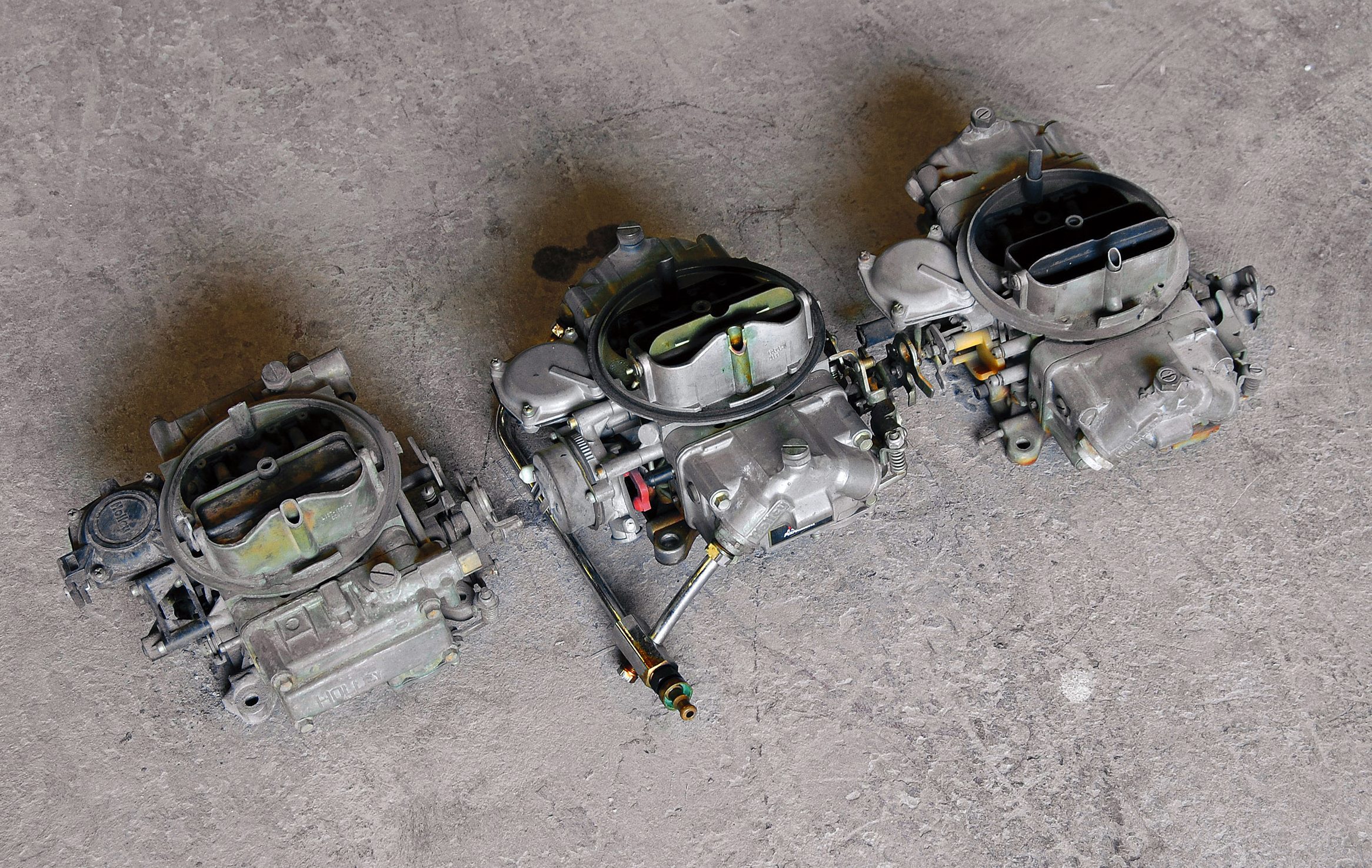
Holley carburetors have long been a staple in the go-fast world of high-performance motoring, whether it’s NASCAR, drag racing or on the street. Much like other performance-oriented products—perhaps even more so with a carburetor—a carburetor requires a fundamental setup and a degree of maintenance, and that’s considering you have chosen the correct-size carburetor for your application, at least to get it in the ballpark. Knowing how to adjust, maintain and even repair your Holley carburetor goes a long way toward helping to ensure that your carburetor will make optimum horsepower for a long time. Because of this, we decided to compile a few troubleshooting and repair tips for the popular 4150-series Holley carburetor, which is the series designation for Holley’s street/strip and racing carburetors.
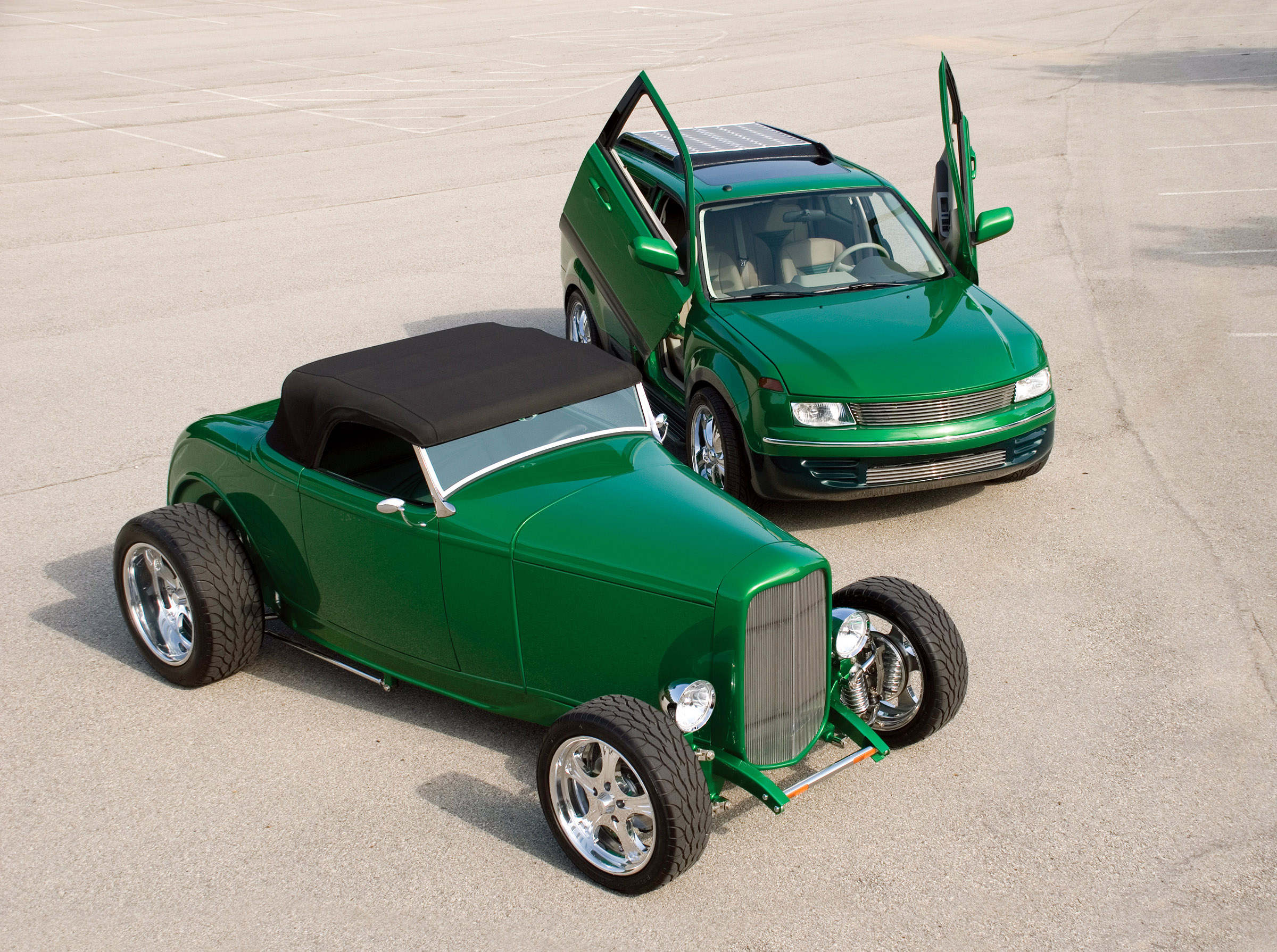
Alternative-fuel sources and hybrid cars are all the rage today. Everyone from major automakers to backyard inventors is pursuing alternative fuels and energy sources. While the ultimate goal is generally to eliminate dependence on foreign oil, for hot rodders there is also the desire to invent and create a better-performing engine.
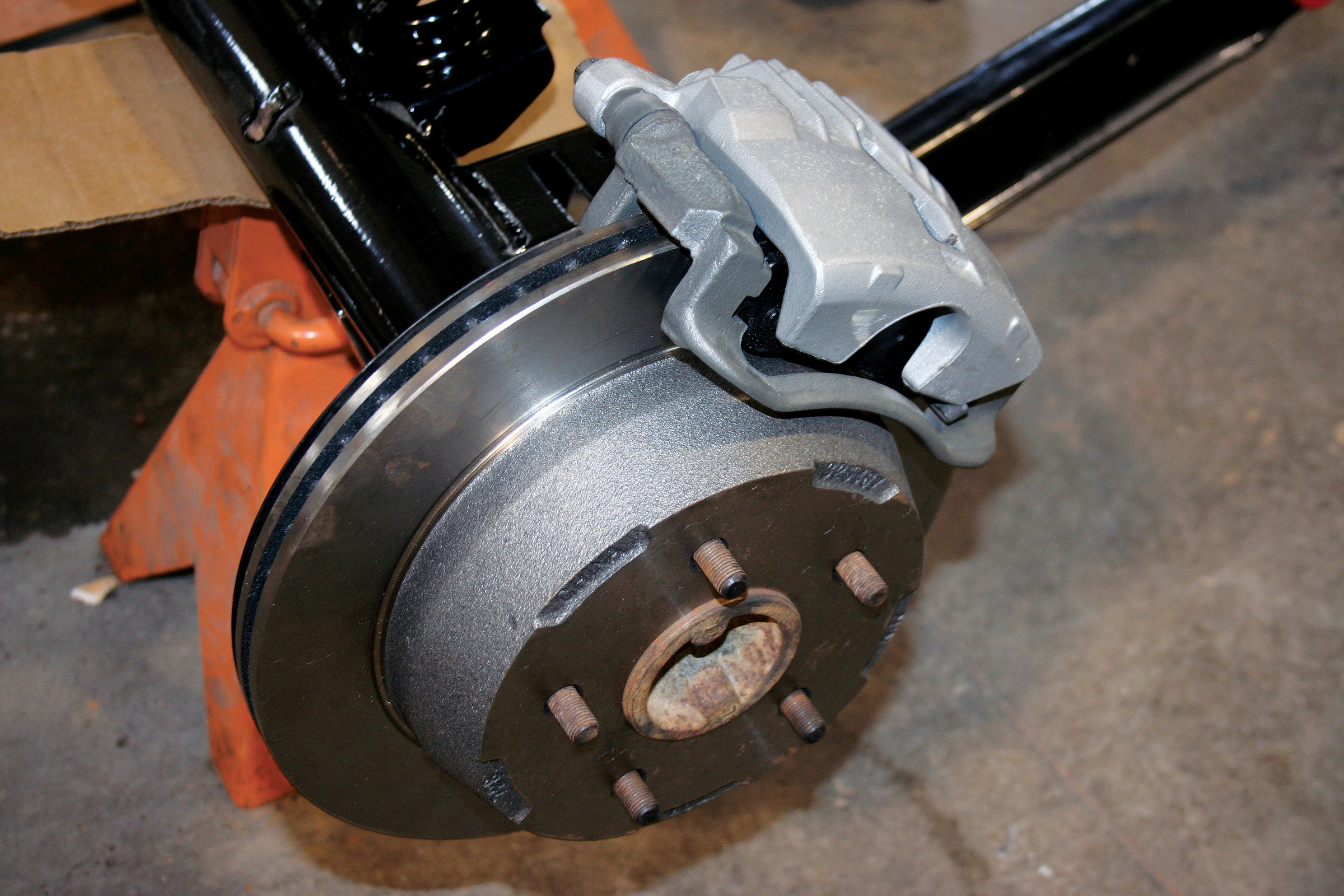
Since we don’t really have to search for vintage parts anymore, gone are the days of scouring the local “Pick-a-Part” in search for that illusive part that will interchange or convert your muscle car to bucket seats, tilt steering, A/C or some suspension upgrade. But there was a day when you and a rodding buddy could venture to your favorite junkyard and come home with a whole truckload of cool vintage goodies that would aid you in your rebuild, all in the span of a day.
Well, those days aren’t completely gone. While at the local wrecking yard looking for any useful hot rod parts, we stumbled across another enthusiast, Sean Rievley, who is in the progress of upgrading his ’71 Chevelle chassis
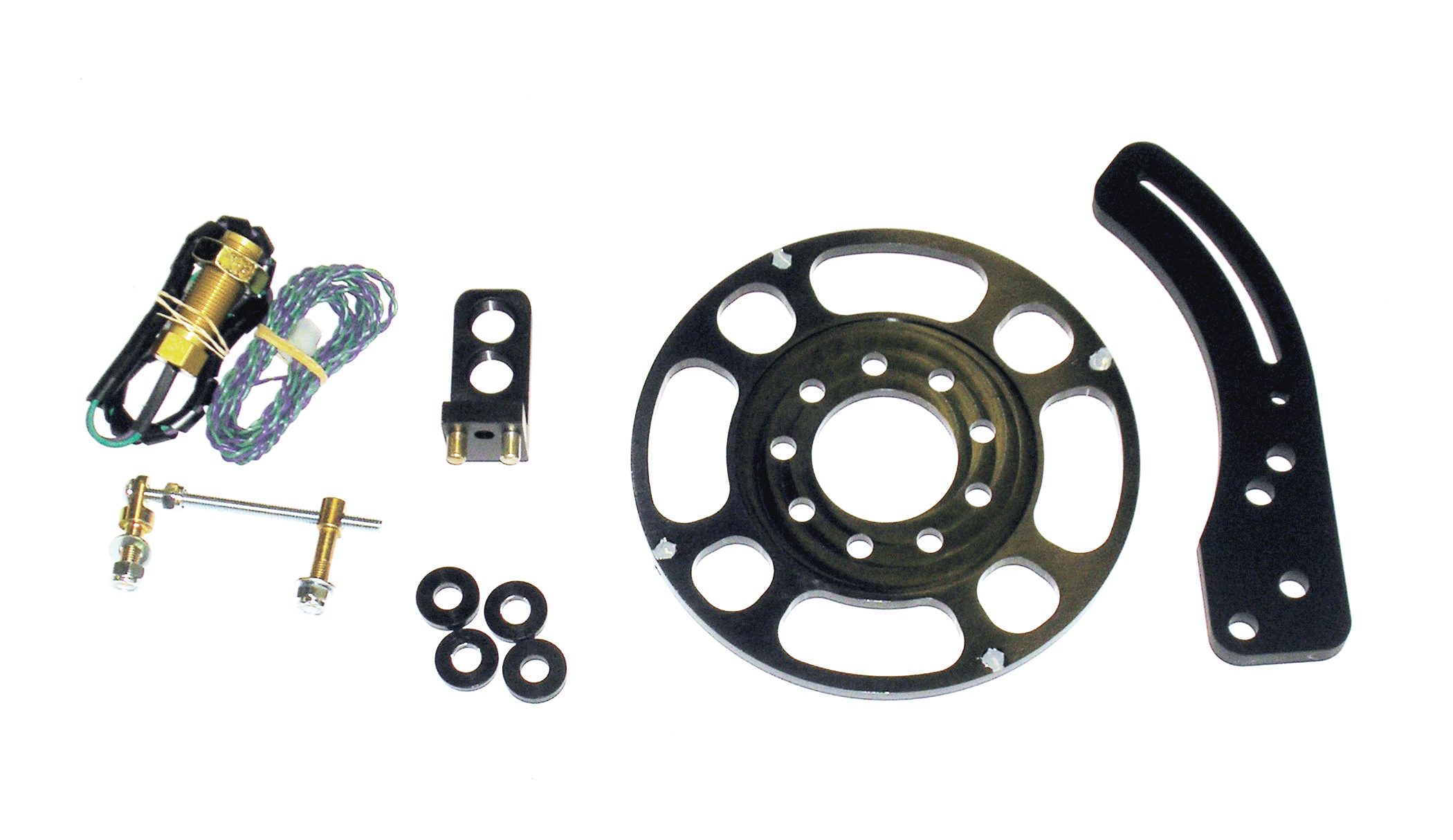
Crankshaft trigger mechanisms have been used in racing applications for a considerable length of time. In truth, they’ve actually been in service for decades. It’s a simple known fact that one of the best ways to improve engine performance is to ensure that the ignition timing is stable. That’s the whole purpose behind such a system, and that’s why racers regularly use them.
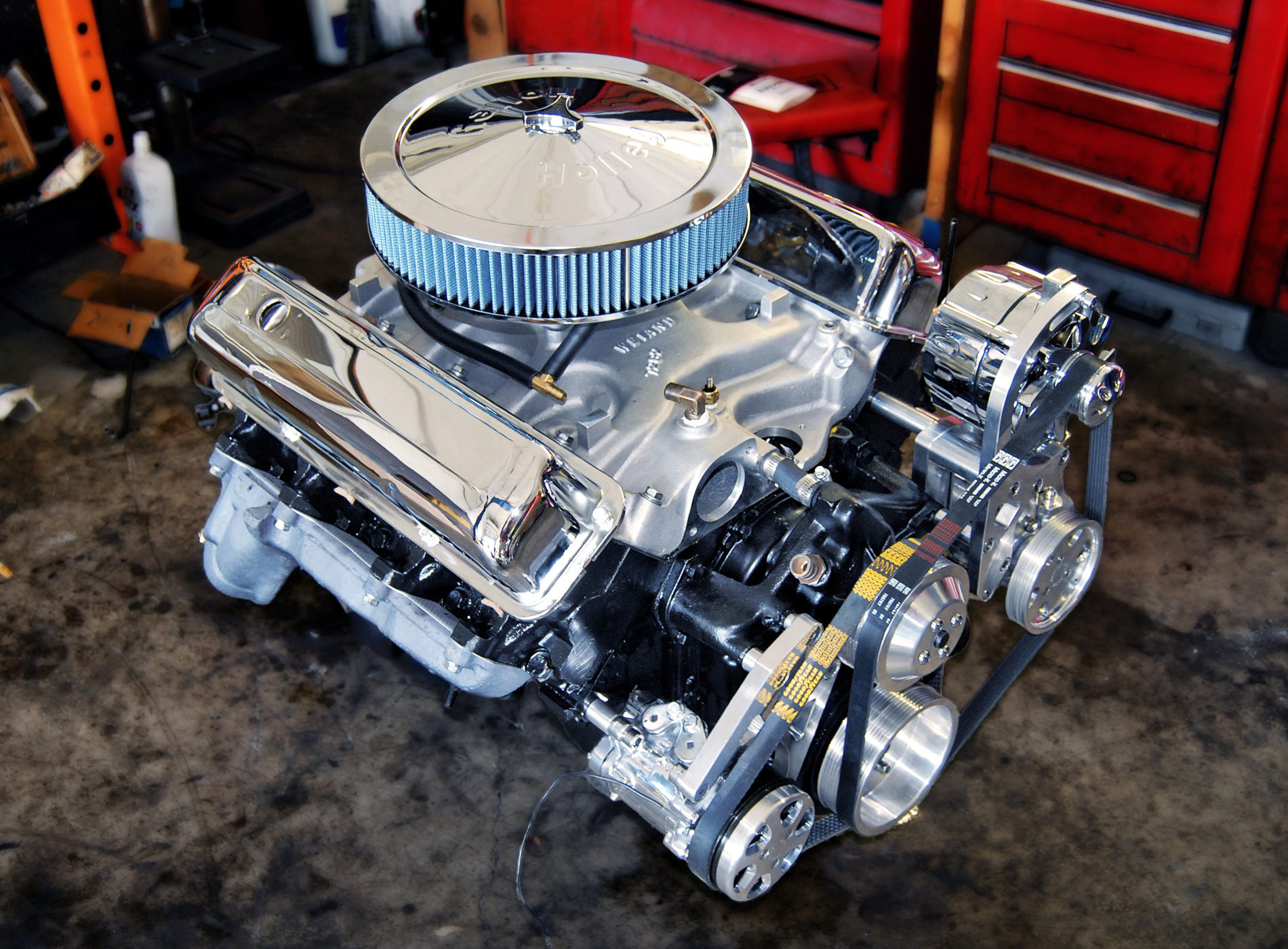
After recently purchasing a ’62 Thunderbird, it became obvious very quickly that the car needed a new engine. Our plan was to turn the car into a daily driver, and so, as long as we needed a new engine, we figured we’d add air conditioning to the car while we were at it. And if you really know your Ford history, you also know that the ’62 was the last model T-bird to come with a generator rather than an alternator—one more reason to consider an upgrade.