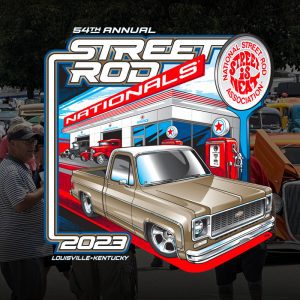
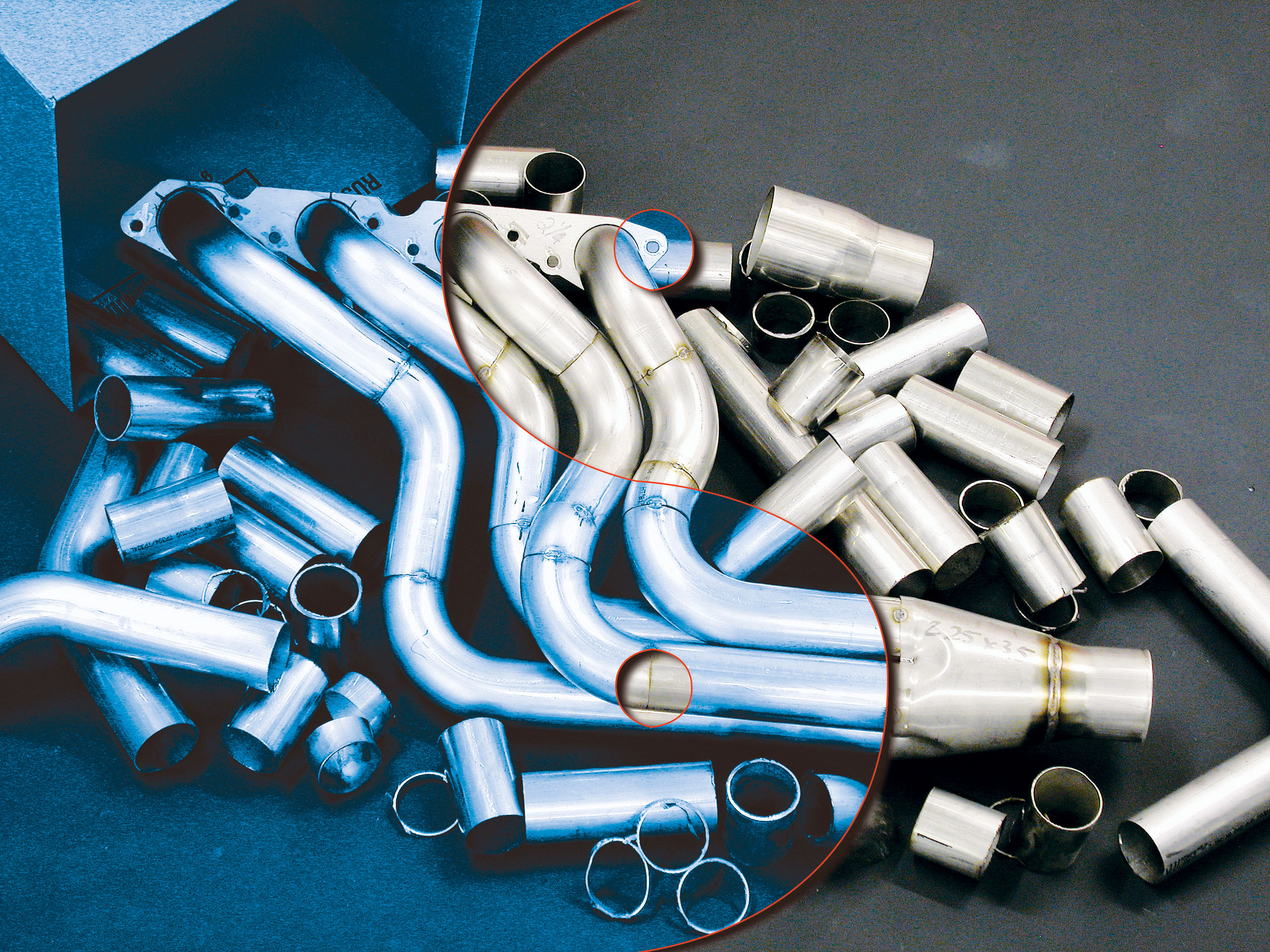
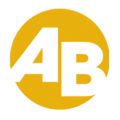
THE AUTO BUILDER
Featured
- All Post
- 20 High Priority - SR Super Rod
- Builds
- 25 High Priority - FB Ford Builder
- Cars
- 30 High Priority - AR American Rodder
- 01 Post Status
- 35 High Priority - RD Rodders Digest
- 40 High Priority - OTR On the Road
- 45 High Priority - SRB Street Rod Builder
- 50 High Priority - TB Truck Builder
- 55 High Priority - BSCENE Buckaroo Scene
- 60 High Priority - FPB Family Power Boat
- Trucks
- Swaps
- Performance Boats
- _000 Home Sliders
- Builders
- 00 Sidebars
- Manufacturers
- 05 High Priority - HCI Hot Compact Imports
- 05 Publications
- 10 High Priority - CR Chevy Rumble
- Back
- Chassis
- Engine
- Fuel System
- Electrical
- Exhaust
- Transmission / Drivetrain
- Suspension
- Steering
- Brakes
- Wheels and Tires
- Interior
- Exterior
- Accessories
- Power Adders
- Back
- Chassis
- Engine
- Fuel System
- Electrical
- Exhaust
- Transmission / Drivetrain
- Suspension
- Steering
- Brakes
- Wheels and Tires
- Interior
- Exterior
- Accessories
- Power Adders
- Back
- Chassis
- Engine
- Electrical
- Exhaust
- Fuel System
- Transmission / Drivetrain
- Suspension
- Steering
- Brakes
- Wheels and Tires
- Interior
- Exterior
- Accessories
- Power Adders
- Back
- Chassis
- Engine
- Electrical
- Exhaust
- Fuel System
- Transmission / Drivetrain
- Suspension
- Steering
- Brakes
- Wheels and Tires
- Interior
- Exterior
- Accessories
- Power Adders
- Back
- Chassis
- Engine
- Fuel System
- Electrical
- Exhaust
- Transmission / Drivetrain
- Suspension
- Steering
- Brakes
- Wheels and Tires
- Interior
- Exterior
- Accessories
- Power Adders
- Back
- Chassis
- Engine
- Fuel System
- Electrical
- Exhaust
- Transmission / Drivetrain
- Suspension
- Steering
- Brakes
- Wheels and Tires
- Interior
- Exterior
- Accessories
- Power Adders
- Back
- Chassis
- Engine
- Fuel System
- Electrical
- Exhaust
- Transmission / Drivetrain
- Suspension
- Steering
- Brakes
- Wheels and Tires
- Interior
- Exterior
- Accessories
- Power Adders
- Back
- Engine
- Fuel System
- Electrical
- Outdrives
- Steering
- Interior
- Accessories
- Power Adders
- Exterior and Hull
- Back
- Chassis
- Engine
- Electrical
- Exhaust
- Fuel System
- Transmission / Drivetrain
- Suspension
- Steering
- Brakes
- Wheels and Tires
- Interior
- Exterior
- Accessories
- Power Adders
- Back
- Chevrolet
- Cadillac
- Pontiac
- AMC
- Buick
- Jeep
- Lincoln
- Ford
- Honda
- GMC
- BMW
- Mitsubishi
- Dodge
- Nissan
- Chrysler
- Subaru
- Toyota
- Plymouth
- Mercury
- Volvo
- Volkswagen
- Oldsmobile
- Acura
- Back
- 05 Pub HCI Hot Compact Imports
- 15 Pub 4x4 4x4 Builder
- 20 Pub SR Super Rod
- 25 Pub FB Ford Builder
- 30 Pub AR American Rodder
- 35 Pub RD Rodders Digest
- 40 Pub OTR On the Road
- 55 Pub BSCENE Buckaroo Scene
- 10 Pub CR Chevy Rumble
- 50 Pub TB Truck Builder
- 60 Pub FPB Family Power Boat
- 45 Pub SRB Street Rod Builder
- Back
- Chip Foose
- Ring Brothers
- Jack Fuller
- Bob Cullipher
- Jerry Nichols
- Bobby Alloway
- Jesse James
- Carl Casper
- J.F. Launier
- Steve Sellers
- Boyd Coddington
- Rad Rides by Troy
- Cal Auto Creations
- George Barris
- West Coast Customs
- Back
- Street Rods
- Hot Rods
- Late Model
- Drag Race
- Handling
- Compact Cars
- Chassis
- Engine
- Fuel System
- Electrical
- Exhaust
- Transmission / Drivetrain
- Suspension
- Steering
- Brakes
- Wheels and Tires
- Interior
- Exterior
- Accessories
- Power Adders
- Chassis
- Engine
- Fuel System
- Electrical
- Exhaust
- Transmission / Drivetrain
- Suspension
- Steering
- Brakes
- Wheels and Tires
- Interior
- Exterior
- Accessories
- Power Adders
- Chassis
- Engine
- Electrical
- Exhaust
- Fuel System
- Transmission / Drivetrain
- Suspension
- Steering
- Brakes
- Wheels and Tires
- Interior
- Exterior
- Accessories
- Power Adders
- Chassis
- Engine
- Electrical
- Exhaust
- Fuel System
- Transmission / Drivetrain
- Suspension
- Steering
- Brakes
- Wheels and Tires
- Interior
- Exterior
- Accessories
- Power Adders
- Chassis
- Engine
- Electrical
- Exhaust
- Fuel System
- Transmission / Drivetrain
- Suspension
- Steering
- Brakes
- Wheels and Tires
- Interior
- Exterior
- Accessories
- Power Adders
- Chassis
- Engine
- Fuel System
- Electrical
- Exhaust
- Transmission / Drivetrain
- Suspension
- Steering
- Brakes
- Wheels and Tires
- Interior
- Exterior
- Accessories
- Power Adders
- Back
- 05 Post Imported
- 20 Post Missing Images (All)
- 25 Post Missing Images (Partial)
- 15 Post In Progress
- 30 Post Internal Review
- 40 Post On Hold
- 50 Post Approved
- 10 Post Images Imported
- 17 Post Missing TXT Files
- 18 Post Missing PDF Files
- 27 Post Missing Content
- Back
- Chassis
- Engine Swaps
- Interior Swaps
- Driveline
- Back
- Street Trucks
- OffRoad Trucks
- Chassis
- Engine
- Fuel System
- Electrical
- Exhaust
- Transmission / Drivetrain
- Suspension
- Steering
- Brakes
- Wheels and Tires
- Interior
- Exterior
- Accessories
- Power Adders
- Chassis
- Engine
- Fuel System
- Electrical
- Exhaust
- Transmission / Drivetrain
- Suspension
- Steering
- Brakes
- Wheels and Tires
- Interior
- Exterior
- Accessories
- Power Adders
- Back
- 01 Sidebar Left
- 01 Sidebar Right
Zen and the Art of Building Headers
Building Headers from a Box of Tube Sections Begins One Bend at a Time
Author
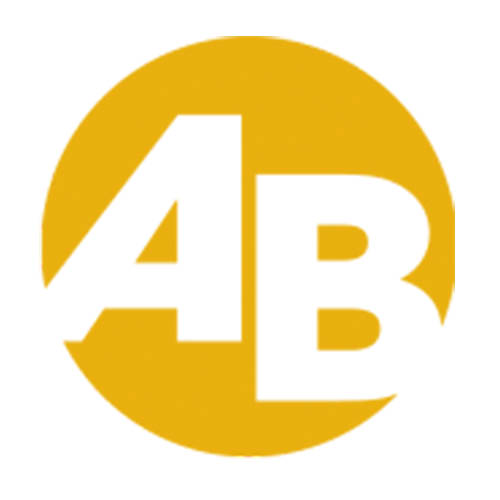
Brad Ocock
Story & Photography
Bending up a set of headers
Bending up a set of headers is one of those fabrication jobs that seem to intimidate most builders, regardless of their skill level. We’ve seen guys who can fabricate full chassis systems balk at taking a box of tubing and mandrel-bent segments to build a set of headers.
Tackling the challenge
Where most people are completely overwhelmed is when they first see that pile of bent tubing segments, and they can’t imagine cutting and assembling them into single, flowing lengths of header pipe. The key is to look at the small picture rather than the big picture. A great analogy we once heard was an Eskimo in his kayak on the ocean when a horrible storm came up. He survived the storm by taking it on one wave at a time, conquering it and moving to the next wave, rather than fighting the entire ocean in an effort to get back to land.
Building custom headers
Custom building a set of headers relies on the same principle. If you think about how all the tubes need to be cut, fit, where each of the bends goes, etc., you’ll quickly be overwhelmed and the project will go nowhere. However, if you simply start at the first bend and build from there, you’ll have a good-looking set of headers before you know it.
Specialized jobs
To be honest, we’ve also considered it one of those “specialized” jobs that get farmed out. But after watching Jeff Georges at Year One weld a set of big tubes for its ProMax Nova project, we found out that fabricating custom headers is more time-consuming than difficult. It’s a pretty straightforward process; it just takes a lot of time and patience. If you can tack-weld, operate a chop saw and have the patience to measure, mark and cut with a high degree of accuracy, creating a set of headers is something well within the grasp of most any builder.
Welding skills
In fact, we’d go so far as to say you don’t even have to have welding skills past tack-welding. If you can’t make a pretty, high-quality weld bead, you can simply tack the pieces in place and then drop the headers off with a professional for final welding.
Power increase with headers
It’s common knowledge that headers are an easy power increase, and a lot has been written over the years on maximizing that power potential. The biggest bit of information most people grab onto and don’t let go of is that equal-length header tubes will make the most power. As a result, everyone wants equal-length tubes. While it’s true equal-length headers will make more power, it’s totally unnecessary on a street car. Bolting a simple set of headers in place of cast-iron exhaust manifolds is an easy power gain. Bolting a set of equal-length headers in place is a huge hassle and frankly, a waste of time and effort.
The math and measuring involved
From a fabrication standpoint, there’s a whole lot of math and measuring involved to get tubes to be all the same length. They require a lot of additional bending in several directions in order for the tube at the rear of the block to terminate at the same place as the tube that starts at the front cylinder. This almost always limits access to spark plugs, steering linkage and boxes, starters and oil filters, not to mention the simple nightmare of bolting up the headers in the first place. On a dedicated Stock-class racer, yeah, they’re mandatory. But for the rest of us? Hardly. As the Buddha says: “Keep it simple, stupid.”
Optimizing the engine
There is a lot of power to be found in the average street engine before an owner needs to start worrying about maximizing his headers. For instance, have you completely blueprinted the entire valvetrain? Rocker arm geometry, valve springs and degreeing the camshaft will give you extra power before headers come into play. How about really tuning your carb? Have you adjusted the curve of your distributor, changed when the advance kicks in? How about tuning your chassis? High-temp coatings? The list goes on.
Racecar versus street car
If you’re building a dedicated racecar, the steps we’ve just listed are part and parcel to building a contender. But on a street car, equal-length headers are nothing more than bragging rights—which are quickly forgotten the first time you have to change an oil filter or spark plugs.
The problem with custom-built headers
Another common problem with custom-built headers is the “bigger equals better” line of thinking. In practice, the opposite is usually the case. If the headers are too large, you’ll actually lose power.
Choosing the right size
So how much is too much? For a small-block street engine, a generally accepted size for primary tubes is 1-5/8 inches to 1-3/4 inches. Obviously, nitrous, superchargers and RPM are going to play factors, and on race engines the size could increase from 1-7/8 inches all the way up to 2 inches for a monster small block. But here again, we’re talking about maximum-effort engines, not your crate engine or hot small block.
Big-block applications
For big-block applications, 1-7/8 inches is typically a good size, with 2 inches at the boundaries of a street application, while 2-1/8 inches to 2-1/4 inches would be normal for a race application. Now again, we’re not talking about monster displacement, forced-induction or huge shots of nitrous. There are always going to be different circumstances and these can’t possibly all be taken into account for a simple magazine article. We’re just throwing these numbers out there so you have a starting point, and so that when you see a warmed-over small block with a single Holley on a dual-plane intake, you’ll recognize that the 2-1/4-inch ceramic-coated headers are more show than go.
Seeking advice
The very best bit of advice we can give in selecting a tube size is to seek the wise man on the mountain. Call the company that’s supplying your segments and ask what it recommends for your particular combination. The next best piece of advice we have is that you listen! The company’s business is headers, so it isn’t going to give you bad advice. There’s no benefit in customer dissatisfaction, and it doesn’t want or need it compounded with bad word-of-mouth that comes from recommending the wrong-sized header tubes.
Year One and Stainless Works
So with all that being said, the guys at Stainless Works had more than a little angst when Year One decided to fab up a set of 2-1/4-inch primary tube headers for the 572ci GM Performance Parts crate engine, knowing full well it was going to be set up for street driving rather than Pro-Mod. However, the whole car is being built with an over-the-top mentality, so the really big header tubes will look right at home with the rest of the really big hardware. Year One’s Jeff “Hollywood” Georges was responsible for the fabrication of the headers; one was assembled for the “Rides” television show, the other for us to photograph and show the construction in greater detail.
Building confidence and learning tricks
In addition to this job being a real confidence-builder, we also learned a couple of very cool tricks for building headers. After watching Georges, I wouldn’t hesitate in building a set in the future. My welding skills aren’t past being able to tack something together, but between that, running a chop saw and attention to detail, it’s not something that’s beyond someone with a medium skill level. Follow along, Grasshopper.
ARTICLE SOURCES
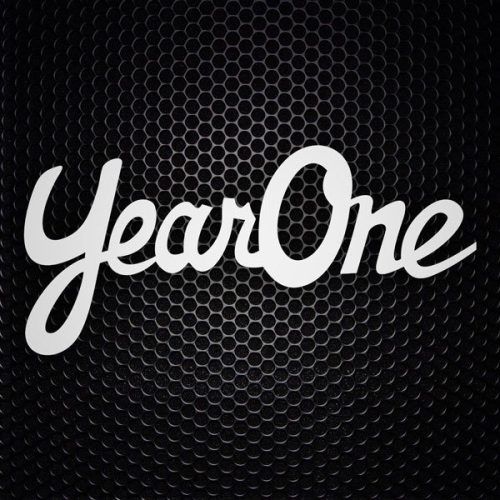
Year One
PO Box 1019
Cornelia, GA 30531
800-932-7663
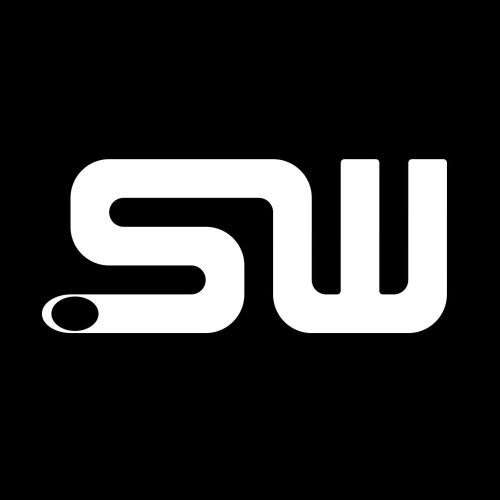
Stainless Works
10145 Philipp Pkwy
Streetsboro, OH 44241
800-878-3635