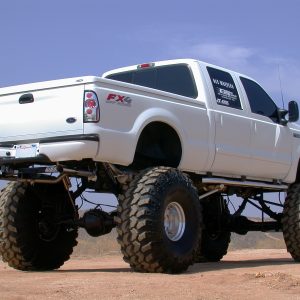
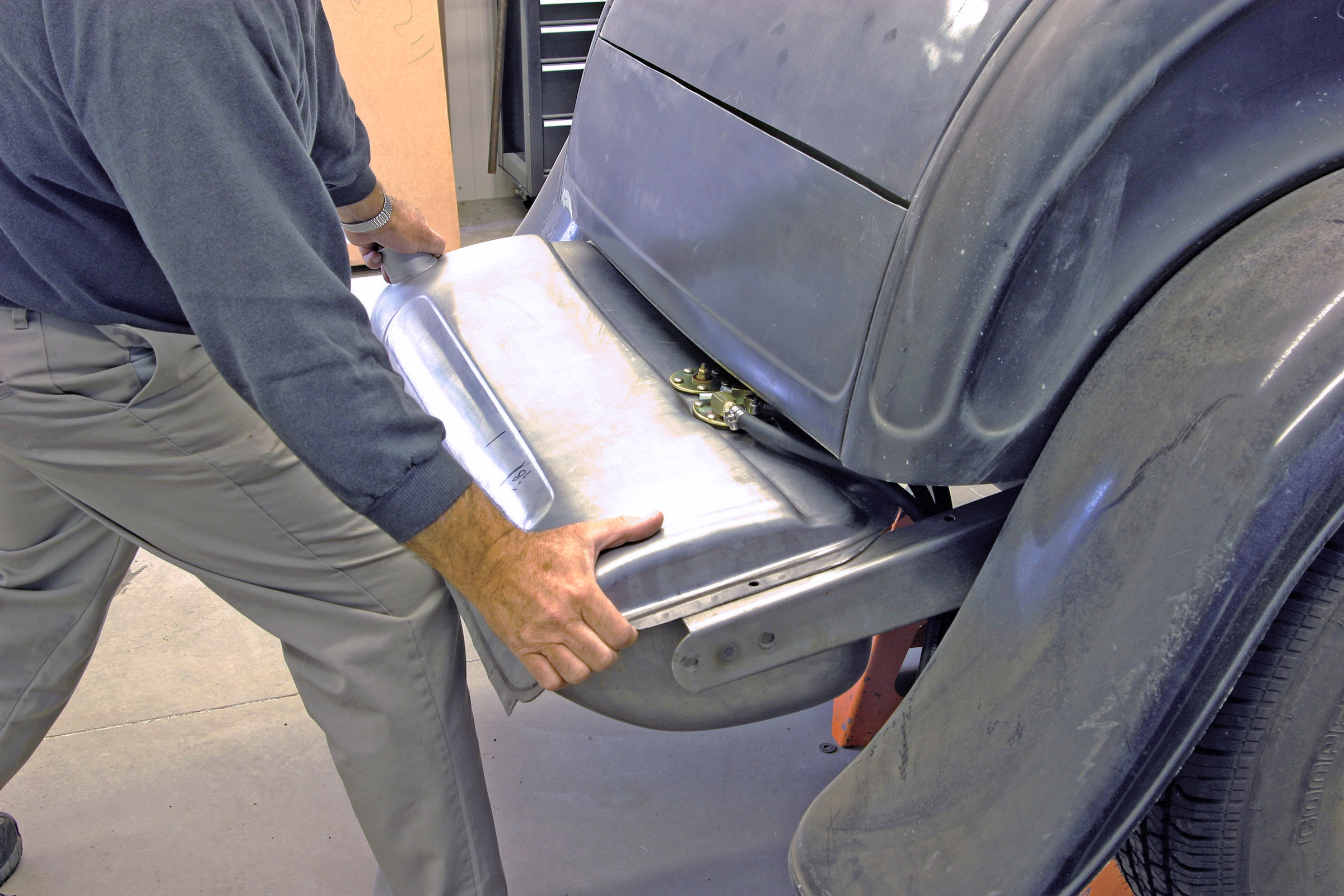
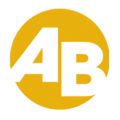
THE AUTO BUILDER
Featured
- All Post
- 20 High Priority - SR Super Rod
- Builds
- 25 High Priority - FB Ford Builder
- Cars
- 30 High Priority - AR American Rodder
- 01 Post Status
- 35 High Priority - RD Rodders Digest
- 40 High Priority - OTR On the Road
- 45 High Priority - SRB Street Rod Builder
- 50 High Priority - TB Truck Builder
- 55 High Priority - BSCENE Buckaroo Scene
- 60 High Priority - FPB Family Power Boat
- Trucks
- Swaps
- Performance Boats
- _000 Home Sliders
- Builders
- 00 Sidebars
- Manufacturers
- 05 High Priority - HCI Hot Compact Imports
- 05 Publications
- 10 High Priority - CR Chevy Rumble
- Back
- Chassis
- Engine
- Fuel System
- Electrical
- Exhaust
- Transmission / Drivetrain
- Suspension
- Steering
- Brakes
- Wheels and Tires
- Interior
- Exterior
- Accessories
- Power Adders
- Back
- Chassis
- Engine
- Fuel System
- Electrical
- Exhaust
- Transmission / Drivetrain
- Suspension
- Steering
- Brakes
- Wheels and Tires
- Interior
- Exterior
- Accessories
- Power Adders
- Back
- Chassis
- Engine
- Electrical
- Exhaust
- Fuel System
- Transmission / Drivetrain
- Suspension
- Steering
- Brakes
- Wheels and Tires
- Interior
- Exterior
- Accessories
- Power Adders
- Back
- Chassis
- Engine
- Electrical
- Exhaust
- Fuel System
- Transmission / Drivetrain
- Suspension
- Steering
- Brakes
- Wheels and Tires
- Interior
- Exterior
- Accessories
- Power Adders
- Back
- Chassis
- Engine
- Fuel System
- Electrical
- Exhaust
- Transmission / Drivetrain
- Suspension
- Steering
- Brakes
- Wheels and Tires
- Interior
- Exterior
- Accessories
- Power Adders
- Back
- Chassis
- Engine
- Fuel System
- Electrical
- Exhaust
- Transmission / Drivetrain
- Suspension
- Steering
- Brakes
- Wheels and Tires
- Interior
- Exterior
- Accessories
- Power Adders
- Back
- Chassis
- Engine
- Fuel System
- Electrical
- Exhaust
- Transmission / Drivetrain
- Suspension
- Steering
- Brakes
- Wheels and Tires
- Interior
- Exterior
- Accessories
- Power Adders
- Back
- Engine
- Fuel System
- Electrical
- Outdrives
- Steering
- Interior
- Accessories
- Power Adders
- Exterior and Hull
- Back
- Chassis
- Engine
- Electrical
- Exhaust
- Fuel System
- Transmission / Drivetrain
- Suspension
- Steering
- Brakes
- Wheels and Tires
- Interior
- Exterior
- Accessories
- Power Adders
- Back
- Chevrolet
- Cadillac
- Pontiac
- AMC
- Buick
- Jeep
- Lincoln
- Ford
- Honda
- GMC
- BMW
- Mitsubishi
- Dodge
- Nissan
- Chrysler
- Subaru
- Toyota
- Plymouth
- Mercury
- Volvo
- Volkswagen
- Oldsmobile
- Acura
- Back
- 05 Pub HCI Hot Compact Imports
- 15 Pub 4x4 4x4 Builder
- 20 Pub SR Super Rod
- 25 Pub FB Ford Builder
- 30 Pub AR American Rodder
- 35 Pub RD Rodders Digest
- 40 Pub OTR On the Road
- 55 Pub BSCENE Buckaroo Scene
- 10 Pub CR Chevy Rumble
- 50 Pub TB Truck Builder
- 60 Pub FPB Family Power Boat
- 45 Pub SRB Street Rod Builder
- Back
- Chip Foose
- Ring Brothers
- Jack Fuller
- Bob Cullipher
- Jerry Nichols
- Bobby Alloway
- Jesse James
- Carl Casper
- J.F. Launier
- Steve Sellers
- Boyd Coddington
- Rad Rides by Troy
- Cal Auto Creations
- George Barris
- West Coast Customs
- Back
- Street Rods
- Hot Rods
- Late Model
- Drag Race
- Handling
- Compact Cars
- Chassis
- Engine
- Fuel System
- Electrical
- Exhaust
- Transmission / Drivetrain
- Suspension
- Steering
- Brakes
- Wheels and Tires
- Interior
- Exterior
- Accessories
- Power Adders
- Chassis
- Engine
- Fuel System
- Electrical
- Exhaust
- Transmission / Drivetrain
- Suspension
- Steering
- Brakes
- Wheels and Tires
- Interior
- Exterior
- Accessories
- Power Adders
- Chassis
- Engine
- Electrical
- Exhaust
- Fuel System
- Transmission / Drivetrain
- Suspension
- Steering
- Brakes
- Wheels and Tires
- Interior
- Exterior
- Accessories
- Power Adders
- Chassis
- Engine
- Electrical
- Exhaust
- Fuel System
- Transmission / Drivetrain
- Suspension
- Steering
- Brakes
- Wheels and Tires
- Interior
- Exterior
- Accessories
- Power Adders
- Chassis
- Engine
- Electrical
- Exhaust
- Fuel System
- Transmission / Drivetrain
- Suspension
- Steering
- Brakes
- Wheels and Tires
- Interior
- Exterior
- Accessories
- Power Adders
- Chassis
- Engine
- Fuel System
- Electrical
- Exhaust
- Transmission / Drivetrain
- Suspension
- Steering
- Brakes
- Wheels and Tires
- Interior
- Exterior
- Accessories
- Power Adders
- Back
- 05 Post Imported
- 20 Post Missing Images (All)
- 25 Post Missing Images (Partial)
- 15 Post In Progress
- 30 Post Internal Review
- 40 Post On Hold
- 50 Post Approved
- 10 Post Images Imported
- 17 Post Missing TXT Files
- 18 Post Missing PDF Files
- 27 Post Missing Content
- Back
- Chassis
- Engine Swaps
- Interior Swaps
- Driveline
- Back
- Street Trucks
- OffRoad Trucks
- Chassis
- Engine
- Fuel System
- Electrical
- Exhaust
- Transmission / Drivetrain
- Suspension
- Steering
- Brakes
- Wheels and Tires
- Interior
- Exterior
- Accessories
- Power Adders
- Chassis
- Engine
- Fuel System
- Electrical
- Exhaust
- Transmission / Drivetrain
- Suspension
- Steering
- Brakes
- Wheels and Tires
- Interior
- Exterior
- Accessories
- Power Adders
- Back
- 01 Sidebar Left
- 01 Sidebar Right
GOING IN THE TANK
The Finer Points of Gas Tank and Fuel System Design
Author
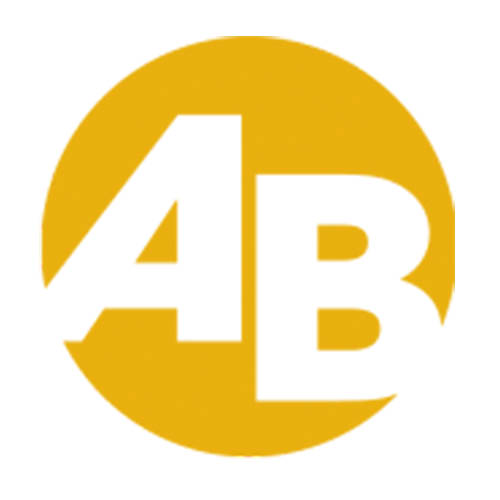
Lane Anderson
Story & Photography
More than one technical article has been written about gas tanks. Some of these articles would lead you to believe that a foam-filled fuel cell is the only solution, and others give you the impression that any tank will work as long as you have a high-dollar, killer fuel pump. However, we believe that the truth lies somewhere between these two opinions.
Your gas tank is only the first part of the fuel system. As more streetcars are equipped with fuel injection and the required higher-pressure fuel pumps, having the components of the fuel system to work in unison becomes more important. As fuel pressure and volume requirements increased, mechanical fuel pumps disappeared, and electric pumps went from an aftermarket item to a standard in the gas tanks of The Big Three.
Higher fuel pressure requires the fuel pump to expend more energy, and with energy comes heat. By putting the pump into the tank, the gasoline in the tank is used to keep the pump cool. Using a flammable liquid (gasoline) to cool the electric pump may sound scary, but remember that only the vapor is flammable-not the liquid. The pump needs to be immersed at all times, including during hard turns, sudden stops and violent accelerations. To keep the liquid around the pump, it becomes necessary to have baffles around the pump. These baffles function like a tank within the tank. It is also not a good idea to uncover the fuel pickup and allow air to be pumped into the fuel lines. Some aftermarket fuel pumps that mount outside of the gas tank recommend adding a 2- or 3-quart accumulator (mini-tank) to prevent starvation of the pump.
We selected Tanks (320/558-6882) because they offer several styles of tanks for many popular applications and several different submerged fuel pumps for almost any application.
Just for ’32 Fords, Tanks offers standard and oversized tanks (11- or 16-gallon) in mild steel, stainless steel, polyethylene and galvanized options. They offer three different fuel pumps, each having a different output flow to match your needs. They also offer fuel pumps with a self-contained reservoir for use in many of the polyethylene tanks. With so many options, good technical support becomes important, and Tanks has an excellent technical support staff.
We selected an oversized, plated, steel tank with internal baffles and a submerged fuel pump that matched the requirements of our TPI fuel injection system. Tanks lists three different fuel pumps for the various volumes and pressure requirements.
The gas tank may be the biggest single part of the fuel system, but the smallest part is just as important. Let’s take a tour through the rest of the fuel system. Gas hose isn’t just gas hose anymore!
The top-of-the-line option is braided stainless steel hose. This is the best-looking option, but the hose and related fittings can get pricy really fast. It is not necessary to use the high-dollar braided hose, but the old-style, low-pressure fuel hose is definitely not suitable. Your local auto parts store can provide you with a black, flexible, high-pressure fuel hose. This hose will be clearly marked “fuel injection.” The fuel return line also requires the high-pressure hose. The old-style, single-rib hose barb fittings are no longer acceptable. Multiple-rib fittings with two hose clamps will handle the higher pressure.
The next component to consider is the fuel filter. The old-style inline plastic filter should not be used for two reasons. First, those filters were not designed for the higher pressure. Second, they cannot handle the volume required for a fuel injection system. For years, the important number was fuel pressure, but that all changed in 1965, when GM introduced the Q-Jet carburetor with its small fuel bowl. From that point forward, the important number became fuel volume.
When you get the fuel supply and return lines to the fuel rails on the engine, you need fittings to connect them. We called Street & Performance (479/394-5711) to ask what we needed to complete our connections. The crew at S&P advised us that the majority of OEM fuel injections use O-ring fittings of a 14mm or 16mm diameter, and S&P can supply adaptor fittings to connect most metric ports to #6 AN fittings.
The TPI system has a 3/8-inch supply line and a 5/16-inch return line, and there was enough line between the fuel rail and the metric fittings that we could cut the factory fittings off, form 37-degree flares and connect a #6 AN union directly to each line. You could buy a lot of adaptors for the price of one flaring tool, but we already had the flaring tool.
The return portion of the system runs from the return line exiting the fuel rail, through a #6 braided hose, to the 3/8-inch steel line and back to the fuel tank. When the return line enters the tank, it should discharge the returning fuel at the bottom of the tank below the liquid level. Dumping the fuel into the top of the tank will cause unwanted splashing, aeration, static electricity and unwanted vapors.
Gas tank venting is not something that you buy, but it is a very real part of your fuel system and should not be ignored. Tanks and other suppliers can help you make good decisions regarding the routing of the vent hose and/or use of a rollover check valve. You should also think about the fact that gasoline weighs approximately 6 pounds per gallon, so 14 gallons of gas will weigh 84 pounds. That is a lot of weight to be sloshing around inside your fuel tank. Baffles in the tank will greatly reduce the sloshing, but the tank needs to be securely anchored. When the fuel has returned to the tank, the fuel system is complete.
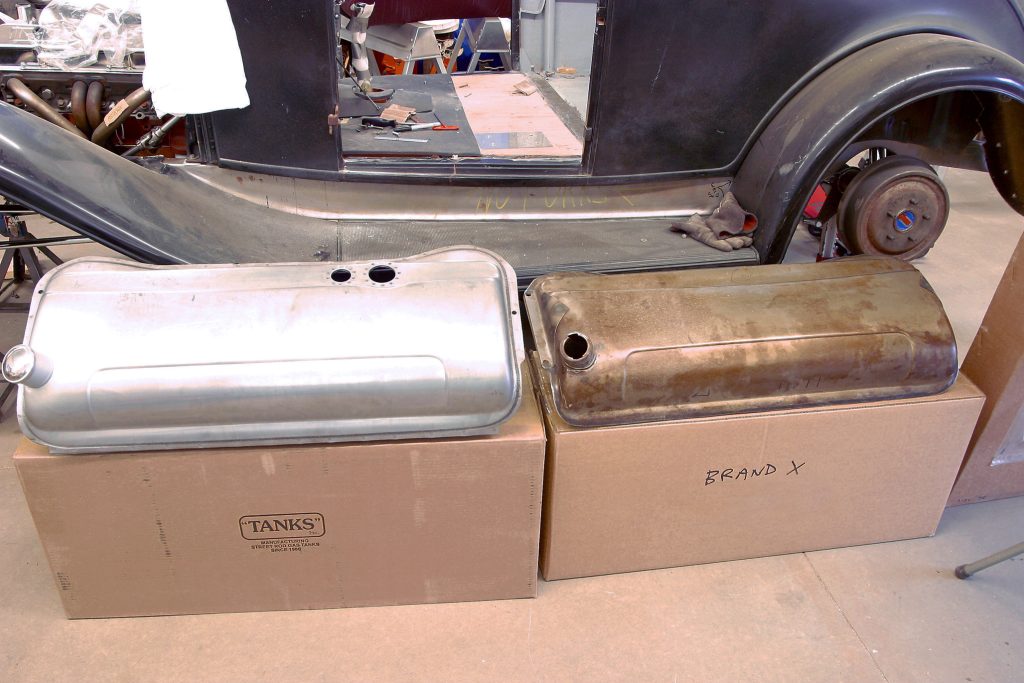
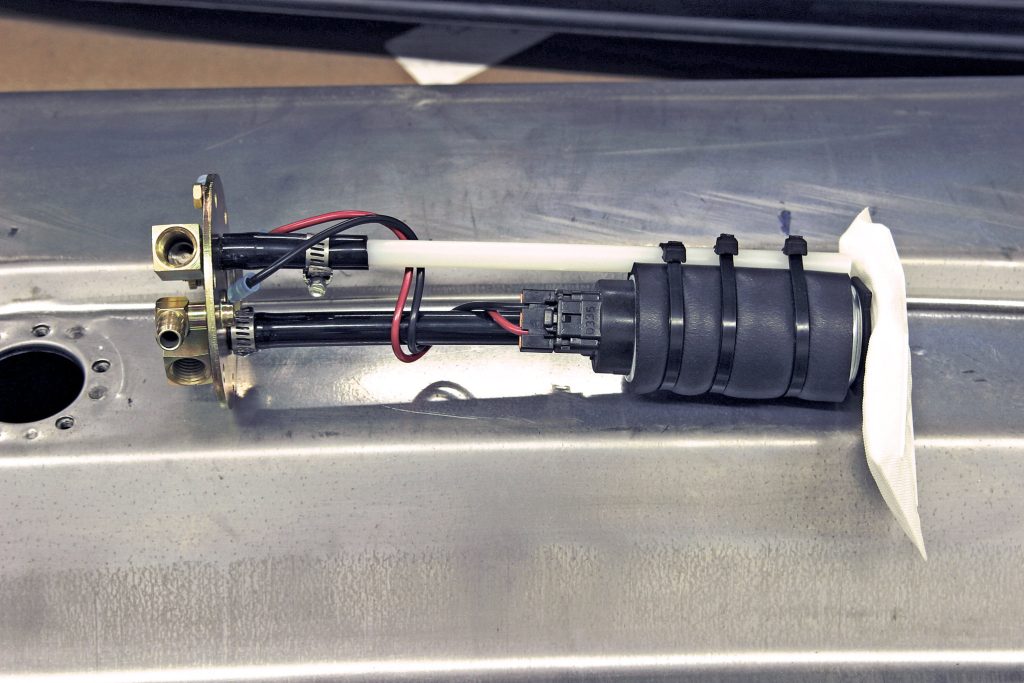
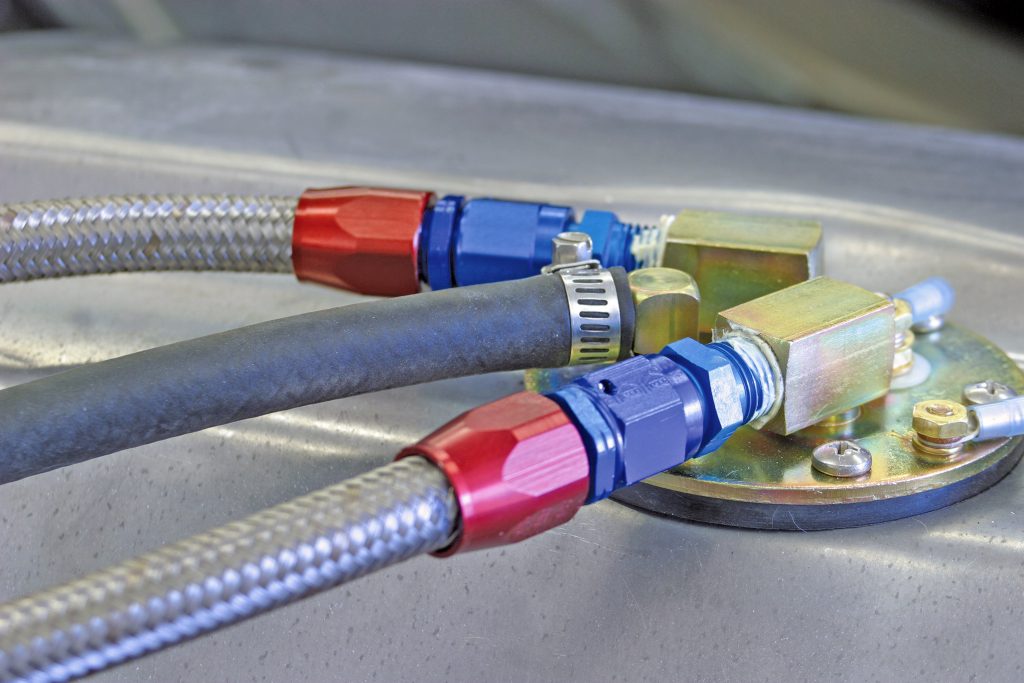
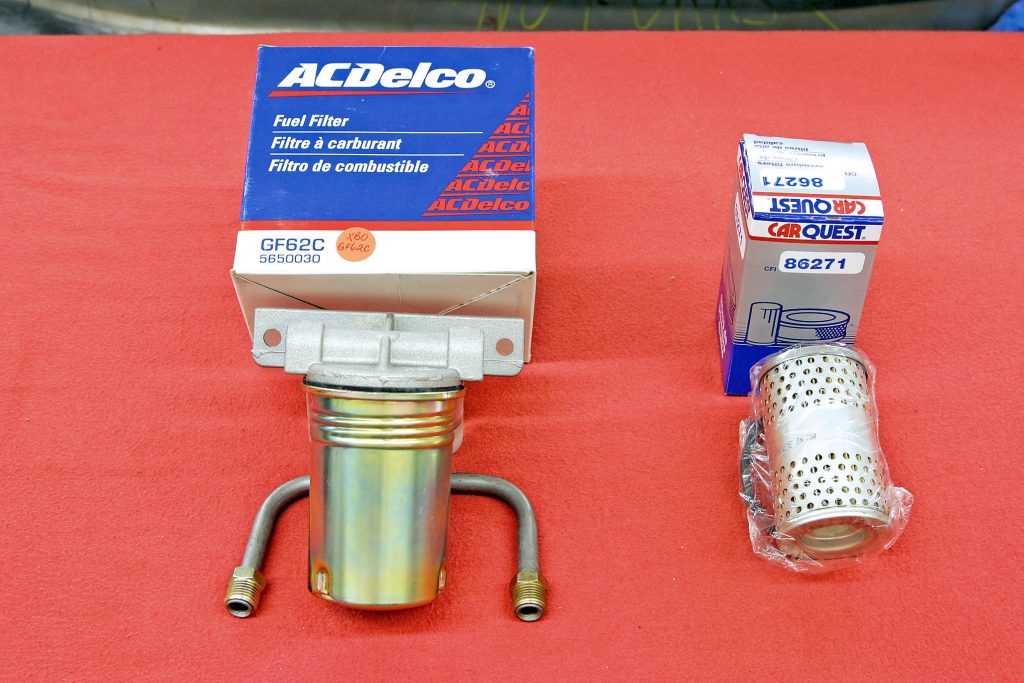
ARTICLE SOURCES
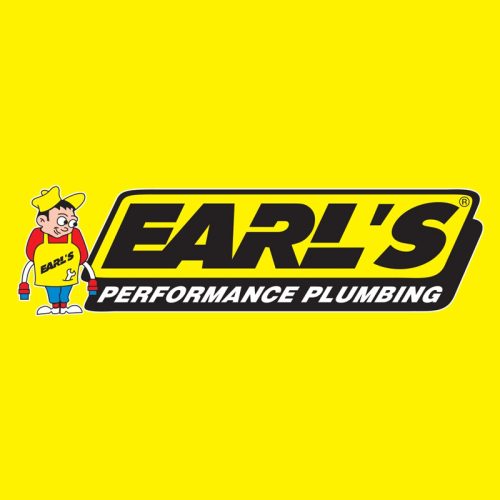
Earl's Performance Plumbing
A Division of Holley
1801 Russelville Rd.
Bowling Green, KY
(866) 464-6553
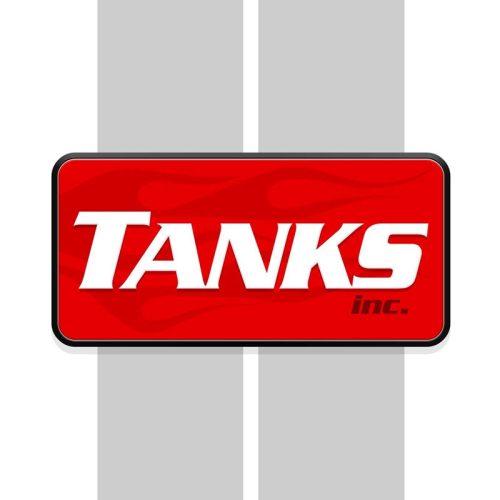
Tanks Inc.
260 Welter Dr,
Monticello, IA
(877) 596-3842
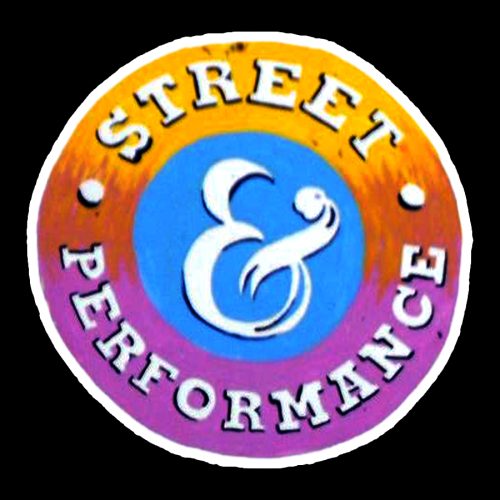
Street & Performance - CLOSED
1 Hot Rod Ln.
Mena, AR 71953
(479) 394-5711