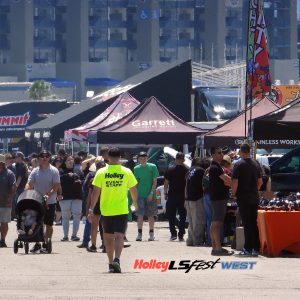
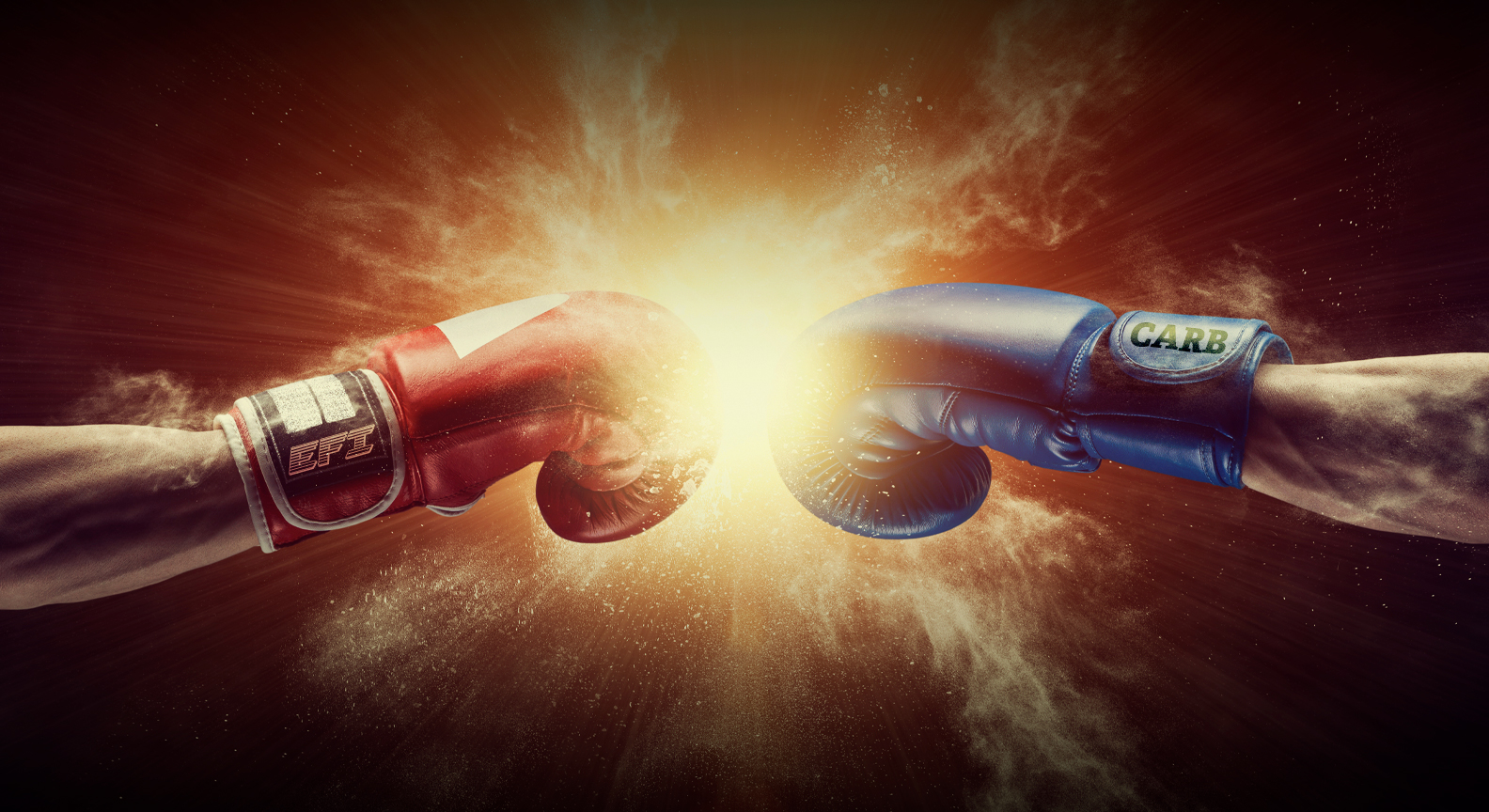
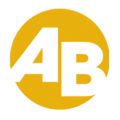
THE AUTO BUILDER
Featured
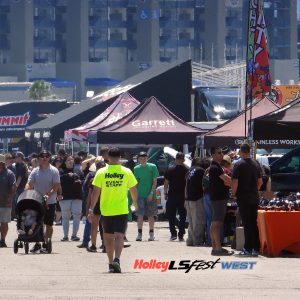
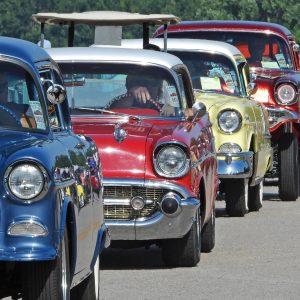
Beech Bend’s Best at the Tri-Five Nationals 2025

JOHNSON & JOHNSON ’CUDA
- All Post
- 20 High Priority - SR Super Rod
- Builds
- 25 High Priority - FB Ford Builder
- Cars
- 30 High Priority - AR American Rodder
- 01 Post Status
- 35 High Priority - RD Rodders Digest
- 40 High Priority - OTR On the Road
- 45 High Priority - SRB Street Rod Builder
- 50 High Priority - TB Truck Builder
- 55 High Priority - BSCENE Buckaroo Scene
- 60 High Priority - FPB Family Power Boat
- Trucks
- Swaps
- Performance Boats
- _000 Home Sliders
- Builders
- 00 Sidebars
- Manufacturers
- 05 High Priority - HCI Hot Compact Imports
- 05 Publications
- 10 High Priority - CR Chevy Rumble
- Back
- Chassis
- Engine
- Fuel System
- Electrical
- Exhaust
- Transmission / Drivetrain
- Suspension
- Steering
- Brakes
- Wheels and Tires
- Interior
- Exterior
- Accessories
- Power Adders
- Back
- Chassis
- Engine
- Fuel System
- Electrical
- Exhaust
- Transmission / Drivetrain
- Suspension
- Steering
- Brakes
- Wheels and Tires
- Interior
- Exterior
- Accessories
- Power Adders
- Back
- Chassis
- Engine
- Electrical
- Exhaust
- Fuel System
- Transmission / Drivetrain
- Suspension
- Steering
- Brakes
- Wheels and Tires
- Interior
- Exterior
- Accessories
- Power Adders
- Back
- Chassis
- Engine
- Electrical
- Exhaust
- Fuel System
- Transmission / Drivetrain
- Suspension
- Steering
- Brakes
- Wheels and Tires
- Interior
- Exterior
- Accessories
- Power Adders
- Back
- Chassis
- Engine
- Fuel System
- Electrical
- Exhaust
- Transmission / Drivetrain
- Suspension
- Steering
- Brakes
- Wheels and Tires
- Interior
- Exterior
- Accessories
- Power Adders
- Back
- Chassis
- Engine
- Fuel System
- Electrical
- Exhaust
- Transmission / Drivetrain
- Suspension
- Steering
- Brakes
- Wheels and Tires
- Interior
- Exterior
- Accessories
- Power Adders
- Back
- Chassis
- Engine
- Fuel System
- Electrical
- Exhaust
- Transmission / Drivetrain
- Suspension
- Steering
- Brakes
- Wheels and Tires
- Interior
- Exterior
- Accessories
- Power Adders
- Back
- Engine
- Fuel System
- Electrical
- Outdrives
- Steering
- Interior
- Accessories
- Power Adders
- Exterior and Hull
- Back
- Chassis
- Engine
- Electrical
- Exhaust
- Fuel System
- Transmission / Drivetrain
- Suspension
- Steering
- Brakes
- Wheels and Tires
- Interior
- Exterior
- Accessories
- Power Adders
- Back
- Chevrolet
- Cadillac
- Pontiac
- AMC
- Buick
- Jeep
- Lincoln
- Ford
- Honda
- GMC
- BMW
- Mitsubishi
- Dodge
- Nissan
- Chrysler
- Subaru
- Toyota
- Plymouth
- Mercury
- Volvo
- Volkswagen
- Oldsmobile
- Acura
- Back
- 05 Pub HCI Hot Compact Imports
- 15 Pub 4x4 4x4 Builder
- 20 Pub SR Super Rod
- 25 Pub FB Ford Builder
- 30 Pub AR American Rodder
- 35 Pub RD Rodders Digest
- 40 Pub OTR On the Road
- 55 Pub BSCENE Buckaroo Scene
- 10 Pub CR Chevy Rumble
- 50 Pub TB Truck Builder
- 60 Pub FPB Family Power Boat
- 45 Pub SRB Street Rod Builder
- Back
- Chip Foose
- Ring Brothers
- Jack Fuller
- Bob Cullipher
- Jerry Nichols
- Bobby Alloway
- Jesse James
- Carl Casper
- J.F. Launier
- Steve Sellers
- Boyd Coddington
- Rad Rides by Troy
- Cal Auto Creations
- George Barris
- West Coast Customs
- Back
- Street Rods
- Hot Rods
- Late Model
- Drag Race
- Handling
- Compact Cars
- Chassis
- Engine
- Fuel System
- Electrical
- Exhaust
- Transmission / Drivetrain
- Suspension
- Steering
- Brakes
- Wheels and Tires
- Interior
- Exterior
- Accessories
- Power Adders
- Chassis
- Engine
- Fuel System
- Electrical
- Exhaust
- Transmission / Drivetrain
- Suspension
- Steering
- Brakes
- Wheels and Tires
- Interior
- Exterior
- Accessories
- Power Adders
- Chassis
- Engine
- Electrical
- Exhaust
- Fuel System
- Transmission / Drivetrain
- Suspension
- Steering
- Brakes
- Wheels and Tires
- Interior
- Exterior
- Accessories
- Power Adders
- Chassis
- Engine
- Electrical
- Exhaust
- Fuel System
- Transmission / Drivetrain
- Suspension
- Steering
- Brakes
- Wheels and Tires
- Interior
- Exterior
- Accessories
- Power Adders
- Chassis
- Engine
- Electrical
- Exhaust
- Fuel System
- Transmission / Drivetrain
- Suspension
- Steering
- Brakes
- Wheels and Tires
- Interior
- Exterior
- Accessories
- Power Adders
- Chassis
- Engine
- Fuel System
- Electrical
- Exhaust
- Transmission / Drivetrain
- Suspension
- Steering
- Brakes
- Wheels and Tires
- Interior
- Exterior
- Accessories
- Power Adders
- Back
- 05 Post Imported
- 20 Post Missing Images (All)
- 25 Post Missing Images (Partial)
- 15 Post In Progress
- 30 Post Internal Review
- 40 Post On Hold
- 50 Post Approved
- 10 Post Images Imported
- 17 Post Missing TXT Files
- 18 Post Missing PDF Files
- 27 Post Missing Content
- Back
- Chassis
- Engine Swaps
- Interior Swaps
- Driveline
- Back
- Street Trucks
- OffRoad Trucks
- Chassis
- Engine
- Fuel System
- Electrical
- Exhaust
- Transmission / Drivetrain
- Suspension
- Steering
- Brakes
- Wheels and Tires
- Interior
- Exterior
- Accessories
- Power Adders
- Chassis
- Engine
- Fuel System
- Electrical
- Exhaust
- Transmission / Drivetrain
- Suspension
- Steering
- Brakes
- Wheels and Tires
- Interior
- Exterior
- Accessories
- Power Adders
- Back
- 01 Sidebar Left
- 01 Sidebar Right
CARB OR EFI?
Testing a 500hp 454 to Find the Answer
Author
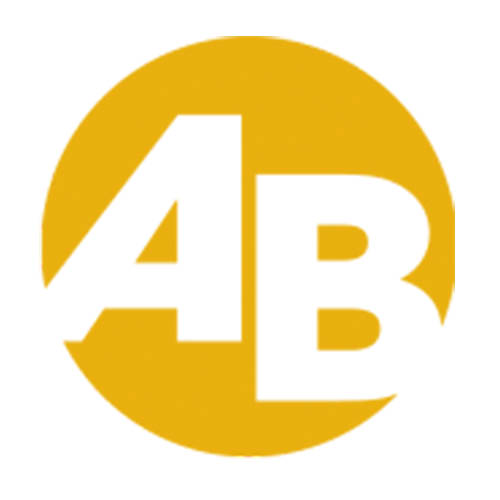
Richard Holdener
Story & Photography
The carb contingent will be quick to point out that the NASCAR boys do pretty well with their carbureted small-block motors, as do many forms of drag racing. Of course, the higher, more sophisticated forms of motorsports all rely on fuel injection—and so they should.
In an absolute test where peak horsepower is the only criteria, a carburetor can be tuned to run extremely efficient over a relatively narrow rpm range. The problem (usually) is that once dialed in for a particular power output and rpm range, the metering at lower engine speeds will generally suffer. This is especially the case where aggressive cam timing, head port volume and a short intake runner length all contribute to reduce the signal to the carburetor. Since the fuel flow is dependent on the strength of the signal, it is difficult for the carburetor to meter fuel properly under these adverse conditions. Obviously, the EFI has no such difficulties dealing with signal strength.
Even without the difficulties experienced on a wild combination, it’s tough to produce an even air/fuel curve over a broad range with a conventional carburetor. Sure, the carb experts will argue that it’s possible to dial in a carburetor with changes to the metering plates; but for most mortals, adjustments to the fuel metering are limited to jet and air bleeds (if so equipped). What usually happens with these changes is a satisfactory air/fuel curve that provides a safe mixture throughout the rpm range.
An example works well here: Suppose we installed a carburetor on a 400hp small block that provided an air/fuel reading of 12.8:1 at the horsepower peak of 6,000 rpm. The curve was pretty consistent, dipping down below 12.0:1 under 3,000 rpm. The problem is that if we decided to change jets to lean out the mixture in an attempt to improve the power output at 3,000 rpm, we would also lean out the mixture at 6,000 rpm. In this case, we are limited to tuning to the leanest spot on the curve. The result is a somewhat less-than-ideal air/fuel mixture elsewhere.
In some cases, the richer mixture may not hurt power and may actually help from a detonation standpoint (if the mixture was richer near the torque peak). But chances are the overall power curve will be down from the inability to dial in the fuel curve.
As we mentioned, the EFI system has the ability to dial in the air/fuel curve at every rpm and load point; thus you can dial in a 13.0:1 air/fuel curve from idle to redline. Though this will probably not produce the best (safe) power curve, the ability to achieve a desired air/fuel mixture will allow you to maximize the power production throughout the rev range.
While this seems like an ideal situation, there is always a price to pay for additional performance. In this case the price is in actual dollars, as a standalone engine management system is considerably more expensive than a typical off-the-shelf carburetor. If you were building an all-out, high-boost turbo motor, fuel injection should be your only choice.
But what about the average Joe assembling a mild big block for his street machine? Is the additional power worth the cost and complexity of converting to fuel injection?
For some, the answer is yes, if for no other reason than they can say they have an injected big block under the hood. With high-octane fuel prices at $2.50 a gallon, the EFI system should also be able to produce better fuel economy. But once again, the question is how much better? And at what cost?
Since we had no intention of running our test motor in a vehicle, a back-to-back test on fuel mileage was out of the question (although it does bear mentioning that the EFI system produced more power with less fuel, indicating that the fuel consumption would certainly be less with a well-tuned EFI setup). This test was designed to illustrate the benefits offered by fuel injection over a conventional carburetor. Our test motor consisted of a 9.3:1 454 equipped with GMPP oval-port aluminum heads, an Xtreme Energy XR276HR hydraulic roller cam (0.510 lift, 224/230 duration), and a single-plane Edelbrock Victor 454-R intake. The combo also included a Holley 850hp carb, MSD distributor and a set of headers running through 3.5-inch mufflers.
The Edelbrock intake was modified to accept fuel injectors by welding receiver bungs at the base of each intake runner. This conversion allowed us to run the intake in its original carbureted configuration, as well as fuel injected, without worrying about an intake swap. All we had to do was replace the carb with a four-hole throttle body from AccuFab and wire in the FAST fuel-injection harness. The converted Edelbrock intake allowed us to perform the carbs vs. computers test without getting dirty.
The first step was to run the 454 in carbureted form with the Holley 850 double-pumper. After a few rounds with jetting and timing, the mild 454 eventually produced 508 hp and 533 lb-ft of torque. The air/fuel curve varied from a low of 12.4:1 to a high of 12.9:1, with a few peaks and valleys along the way. Basically, we tuned to produce the highest air/fuel near 13.0:1, but this left a few areas still down below 12.5:1.
After installing the EFI setup and FAST management system, we were able to tune the mixture to produce optimum power throughout the rev range. The result was a gain of 6 hp to 8 hp and 6 to 8 lb-ft along the curve with the majority of power coming at the top, thanks to an air/fuel ratio of 13.0:1.
While the EFI system did allow us to dial in the air/fuel (and timing) curves of the 454, is the additional 6 hp to 8 hp worth an extra $2,000? Put another way, the traditional carburetor seemed to hold its own pretty well on this mild combination, and despite the slight difference in power would likely work every bit as well on the street. EFI is definitely better, but we can’t help but marvel at the simplicity and effectiveness of the simple carburetor. So there’s little wonder why carbureted motors are still going strong.
While we had the 454 on the dyno, we decided to run one final test. We suspected that the single-plane Victor Jr. was not ideal for our 5,500rpm big block, and that the application would be much better suited to a dual plane. As luck would have it, the Westech guys had an Edelbrock Performer RPM Air Gap intake handy, and we performed the intake swap with the motor still warm from the previous testing. The Edelbrock Performer RPM was run with the same Holley 850hp carb that produced such good results on the single-plane intake. Minor jetting was necessary due to the dramatic change in torque production, but it was clear on the first pull that the dual-plane was definitely the hot setup for this big-block Chevy.
In most cases, a dual-plane intake will increase the low- and mid-range torque while sacrificing top-end power to the more racy single plane. In this case the dual plane added all the torque, but sacrificed no peak power. Equipped with the dual plane, the 454 produced 514 hp (equaling the EFI setup), along with an amazing 564 lb-ft of torque. Torque production with the dual plane bettered the single plane by as much as 40 lb-ft. With more peak torque and more peak power, the dual-plane RPM Air Gap was clearly the intake for this 500hp big-block application.
Holley 850hp Carb vs. FAST EFI 454
For this test we ran the same Edelbrock Victor Jr. 454-R intake with both a carburetor and with fuel injection. This was accomplished by converting the manifold to EFI use. The conversion required welding injector bungs in place to provide fuel delivery to each port. Common fuel rails were used in conjunction with the eight injectors (four per side). This converted intake allowed us to install a Holley 850 carburetor and then run it again with the injectors and a four-hole AccuFab throttle body, all without removing the intake. We simply kept the injectors in place to eliminate any vacuum leaks while running the carb. The EFI injectors and MSD distributor were controlled by the FAST management system. The idea was to demonstrate the effectiveness of the EFI system compared to the conventional carburetor.
In the end, the power numbers were very close, with the nod going to the EFI setup. The extra power came from the ability to fine-tune the air/fuel mixture at every rpm. In the case of the carburetor, such fine rpm-specific adjustments are not possible, and though the air/fuel curve was good with the Holley carb, it was perfect with the EFI. This perfection netted an additional 6 hp to 8 hp and a like amount of torque. For most enthusiasts, the cost of this additional perfection is a tad on the steep side, as a carburetor is considerably less expensive than the cost of converting to fuel injection. Â
Performer RPM Air Gap vs. Victor Jr. 454-R
No matter how hard we try to convince enthusiasts, they seem bound and determined to pick the racy single-plane intake over the more effective dual plane. This is especially the case where the single-plane intake makes more ultimate peak power than the dual plane (which is often the case). Even in the cases where the single-plane manifold makes more peak power at high rpm, the dual plane will always offer more low- and mid-range torque on street-driven combinations.
In the case of our 454 test motor, the dual plane not only produced considerably more torque in the low- and mid-range, but also managed to equal the peak power output of the single-plane manifold. For this mild 454 application, the dual plane was definitely the intake manifold of choice. It is hard to argue with equal peak power, yet as much as 40 extra lb-ft of torque. Had we run the single-plane intake below 3,500 rpm, the torque difference might have been even greater.
We’ll say it one last time: For the vast majority of street applications, the dual-plane Performer RPM Air Gap is tough to beat.
ARTICLE SOURCES
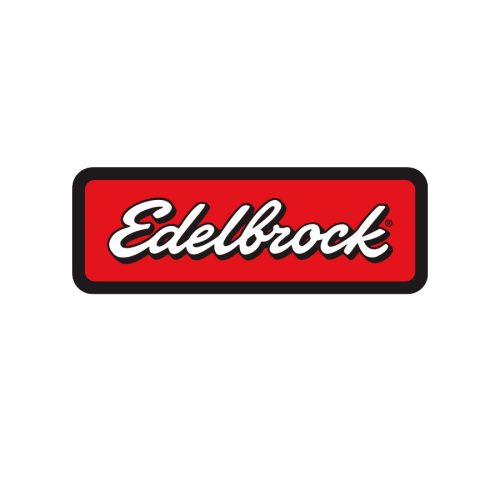
Edelbrock
8649 Hacks Cross Rd
Olive Branch, MS 38654
800/999-0853
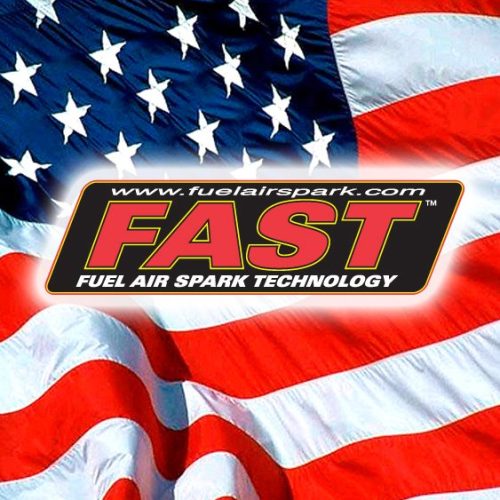
FAST - Fuel Air Spark Technology
8649 Hacks Cross Rd
Olive Branch, MS 38654
800/999-0853
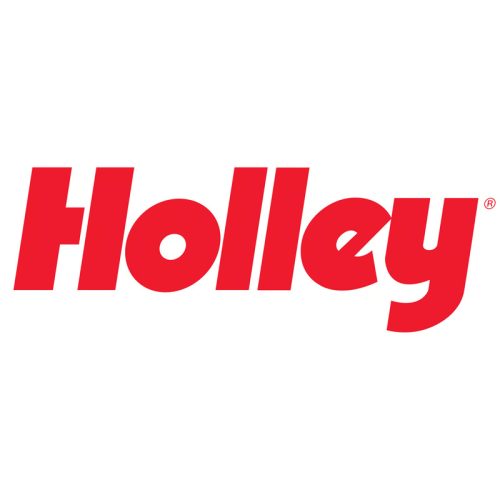
Holley
1801 Russellville Rd.
Bowling Green, KY 42102
270/782-2900