How the Pros Make Perfect Brackets
You’ve seen them plenty of times; in shops, tech articles and featured buildups, as well as on many a rolling chassis and frontend displays in vendors’ booths. What we are referencing are those perfectly cut and finished brackets, made from quarter-inch (or thicker) steel plate. There are never any visible cutting marks around their edges, and no evidence of filing or grinding. Anyone who has made his own brackets at home in the garage, using a hacksaw and a file, has to wonder at the perfection of these pieces.
Most of you already know that these brackets are fabricated using a plasma cutter, an incredible invention that has practically replaced the gas torch—it requires only a very steady hand to make great-Âlooking cuts. Evolution then stepped it up and the pantograph—which is a series of parallel arms and pivot points allowing a plasma cutter to copy a pattern repeatedly and accurately—has been used successfully. Now, through the magic of digital technology and the introduction of precision stepper motors, inexpensive yet powerful computers and affordable, user-friendly CAD software, aftermarket manufacturers (and even the average street rod shop) can have at their disposal a totally automated plasma cutting system. But there’s one last portion of that evolution which makes all this new technology so adaptable today, and that’s the younger, computer-savvy generation of shop technicians who were born and raised in the digital decade and have NO FEAR.
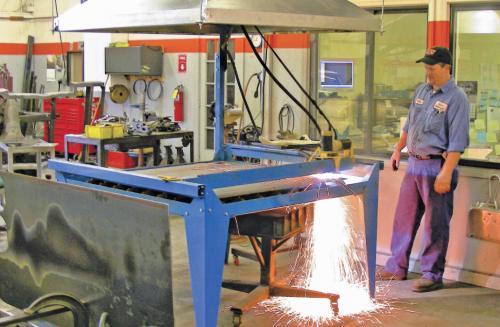
On a recent trip to Fat Man Fabrications in Charlotte, North Carolina, we curiously asked what was going on inside a large, black curtained box shielding a brilliant glow and spewing sparks out the bottom. We found the answer to be very interesting and thought you’d enjoy a look yourselves. For garage builders like us, this is presented as entertaining information, but for a rod shop that does any production work, this is an introduction to a new piece of equipment which could very likely cut your fabrication labor costs in half, while producing a higher-quality part.Â
Follow along as we show how Kevin Weekly designs and cuts a fresh batch of rearend four-link mounts. Bear this in mind as you check it out: Each rearend requires four hanger sides and two hanger backs. Do you think you can make one hanger side in the time it takes Weekly to produce four complete sets, plus a like number of the parts required to mount the forward ends of the links? How about if we told you it takes him less than 30 minutes, raw material to parts on the shelf? Ain’t technology great?Â