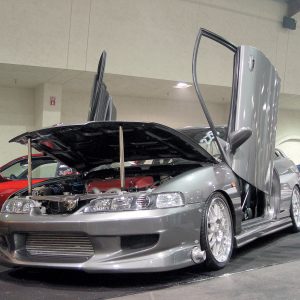
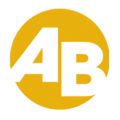
THE AUTO BUILDER
Featured
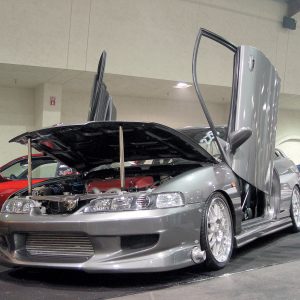
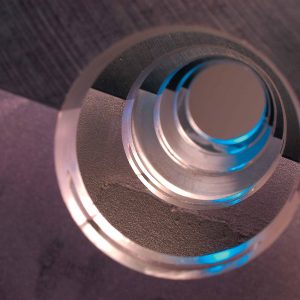
B-Series Bullseye: Part II
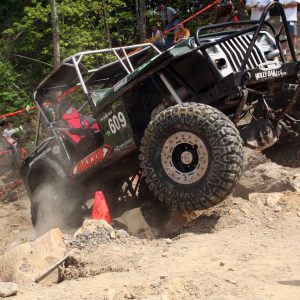
Rock Crawling the Sport That Defines Champions
- All Post
- 20 High Priority - SR Super Rod
- Builds
- 25 High Priority - FB Ford Builder
- Cars
- 30 High Priority - AR American Rodder
- 01 Post Status
- 35 High Priority - RD Rodders Digest
- 40 High Priority - OTR On the Road
- 45 High Priority - SRB Street Rod Builder
- 50 High Priority - TB Truck Builder
- 55 High Priority - BSCENE Buckaroo Scene
- 60 High Priority - FPB Family Power Boat
- Trucks
- Swaps
- Performance Boats
- _000 Home Sliders
- Builders
- 00 Sidebars
- Manufacturers
- 05 High Priority - HCI Hot Compact Imports
- 05 Publications
- 10 High Priority - CR Chevy Rumble
- Back
- Chassis
- Engine
- Fuel System
- Electrical
- Exhaust
- Transmission / Drivetrain
- Suspension
- Steering
- Brakes
- Wheels and Tires
- Interior
- Exterior
- Accessories
- Power Adders
- Back
- Chassis
- Engine
- Fuel System
- Electrical
- Exhaust
- Transmission / Drivetrain
- Suspension
- Steering
- Brakes
- Wheels and Tires
- Interior
- Exterior
- Accessories
- Power Adders
- Back
- Chassis
- Engine
- Electrical
- Exhaust
- Fuel System
- Transmission / Drivetrain
- Suspension
- Steering
- Brakes
- Wheels and Tires
- Interior
- Exterior
- Accessories
- Power Adders
- Back
- Chassis
- Engine
- Electrical
- Exhaust
- Fuel System
- Transmission / Drivetrain
- Suspension
- Steering
- Brakes
- Wheels and Tires
- Interior
- Exterior
- Accessories
- Power Adders
- Back
- Chassis
- Engine
- Fuel System
- Electrical
- Exhaust
- Transmission / Drivetrain
- Suspension
- Steering
- Brakes
- Wheels and Tires
- Interior
- Exterior
- Accessories
- Power Adders
- Back
- Chassis
- Engine
- Fuel System
- Electrical
- Exhaust
- Transmission / Drivetrain
- Suspension
- Steering
- Brakes
- Wheels and Tires
- Interior
- Exterior
- Accessories
- Power Adders
- Back
- Chassis
- Engine
- Fuel System
- Electrical
- Exhaust
- Transmission / Drivetrain
- Suspension
- Steering
- Brakes
- Wheels and Tires
- Interior
- Exterior
- Accessories
- Power Adders
- Back
- Engine
- Fuel System
- Electrical
- Outdrives
- Steering
- Interior
- Accessories
- Power Adders
- Exterior and Hull
- Back
- Chassis
- Engine
- Electrical
- Exhaust
- Fuel System
- Transmission / Drivetrain
- Suspension
- Steering
- Brakes
- Wheels and Tires
- Interior
- Exterior
- Accessories
- Power Adders
- Back
- Chevrolet
- Cadillac
- Pontiac
- AMC
- Buick
- Jeep
- Lincoln
- Ford
- Honda
- GMC
- BMW
- Mitsubishi
- Dodge
- Nissan
- Chrysler
- Subaru
- Toyota
- Plymouth
- Mercury
- Volvo
- Volkswagen
- Oldsmobile
- Acura
- Back
- 05 Pub HCI Hot Compact Imports
- 15 Pub 4x4 4x4 Builder
- 20 Pub SR Super Rod
- 25 Pub FB Ford Builder
- 30 Pub AR American Rodder
- 35 Pub RD Rodders Digest
- 40 Pub OTR On the Road
- 55 Pub BSCENE Buckaroo Scene
- 10 Pub CR Chevy Rumble
- 50 Pub TB Truck Builder
- 60 Pub FPB Family Power Boat
- 45 Pub SRB Street Rod Builder
- Back
- Chip Foose
- Ring Brothers
- Jack Fuller
- Bob Cullipher
- Jerry Nichols
- Bobby Alloway
- Jesse James
- Carl Casper
- J.F. Launier
- Steve Sellers
- Boyd Coddington
- Rad Rides by Troy
- Cal Auto Creations
- George Barris
- West Coast Customs
- Back
- Street Rods
- Hot Rods
- Late Model
- Drag Race
- Handling
- Compact Cars
- Chassis
- Engine
- Fuel System
- Electrical
- Exhaust
- Transmission / Drivetrain
- Suspension
- Steering
- Brakes
- Wheels and Tires
- Interior
- Exterior
- Accessories
- Power Adders
- Chassis
- Engine
- Fuel System
- Electrical
- Exhaust
- Transmission / Drivetrain
- Suspension
- Steering
- Brakes
- Wheels and Tires
- Interior
- Exterior
- Accessories
- Power Adders
- Chassis
- Engine
- Electrical
- Exhaust
- Fuel System
- Transmission / Drivetrain
- Suspension
- Steering
- Brakes
- Wheels and Tires
- Interior
- Exterior
- Accessories
- Power Adders
- Chassis
- Engine
- Electrical
- Exhaust
- Fuel System
- Transmission / Drivetrain
- Suspension
- Steering
- Brakes
- Wheels and Tires
- Interior
- Exterior
- Accessories
- Power Adders
- Chassis
- Engine
- Electrical
- Exhaust
- Fuel System
- Transmission / Drivetrain
- Suspension
- Steering
- Brakes
- Wheels and Tires
- Interior
- Exterior
- Accessories
- Power Adders
- Chassis
- Engine
- Fuel System
- Electrical
- Exhaust
- Transmission / Drivetrain
- Suspension
- Steering
- Brakes
- Wheels and Tires
- Interior
- Exterior
- Accessories
- Power Adders
- Back
- 05 Post Imported
- 20 Post Missing Images (All)
- 25 Post Missing Images (Partial)
- 15 Post In Progress
- 30 Post Internal Review
- 40 Post On Hold
- 50 Post Approved
- 10 Post Images Imported
- 17 Post Missing TXT Files
- 18 Post Missing PDF Files
- 27 Post Missing Content
- Back
- Chassis
- Engine Swaps
- Interior Swaps
- Driveline
- Back
- Street Trucks
- OffRoad Trucks
- Chassis
- Engine
- Fuel System
- Electrical
- Exhaust
- Transmission / Drivetrain
- Suspension
- Steering
- Brakes
- Wheels and Tires
- Interior
- Exterior
- Accessories
- Power Adders
- Chassis
- Engine
- Fuel System
- Electrical
- Exhaust
- Transmission / Drivetrain
- Suspension
- Steering
- Brakes
- Wheels and Tires
- Interior
- Exterior
- Accessories
- Power Adders
- Back
- 01 Sidebar Left
- 01 Sidebar Right
B-Series Block Hop-up
Sleeving A B-series Block Is Not New, But How It Is Done Can Make All The Difference
Author
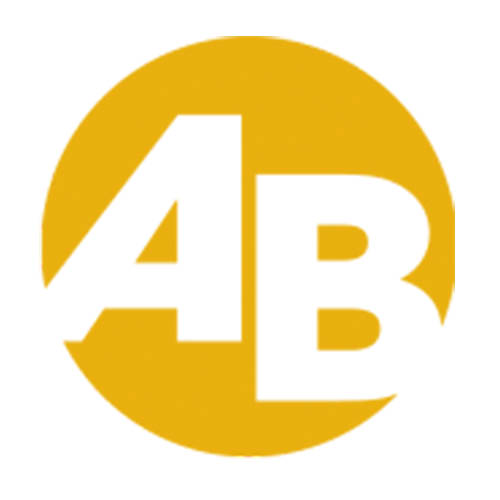
Sean Greene
Words & Photography
These days, if you want to go fast on the track in a Honda, forced induction is almost a must, as most vehicles come with relatively small-displacement engines when compared to their domestic brethren. Basically, the more cylinder pressure and fuel that you can ignite, the faster you go. Admittedly, this all sounds pretty general, but for now, let’s roll with that thought.
THE FIRST STEP IS TO REMOVE THE GREASE AND DIRT FROM THE BLOCK. THE EASIEST WAY TO DO THIS IS TO PLACE THE STRIPPED BLOCK INTO WHAT IS CALLED A HOT TANK. BASICALLY, HOT WATER AND CHEMICALS ARE SPRAYED ON THE BLOCK AND COOKED TO REMOVE YEARS OF GRIME AND GUNK. ONCE THIS IS DONE, THE BLOCK CAN BE INSPECTED FOR CRACKS OR OTHER IMPERFECTIONS.
The problem with running a lot of boost on the B-series block is that the open-deck design, is great for efficiency, but lousy for strength. The factory sleeves tend to flex, causing ring sealing problems and resulting in a loss of power. They may even crack under the high-pressure conditions associated with extreme racing.
B-series blocks are made from aluminum alloy, which is great for saving weight, but it’s not as strong as an iron block that affords increased strength at the cost of added weight. In both cases, there’s a tradeoff: you either get strength and a weight penalty with the iron block or lower weight and frailty with an aluminum block.
Another problem with the B-series block is that if you wish to increase the bore size due to replacement pistons, you must bore the factory sleeve. This leaves less material for strength, which compounds the open-deck problem.
Luckily, this isn’t as bleak as it sounds. Owners of B-series blocks have solutions to these problems, such as CNC-fabricated block guards or spacers that are pressed in at the top of the block to minimize flex and distortion of the cylinders. There’s also the all-new Dart block, but we’ll save that one for another article.
However, the problem with block guards or spacers is they are limited to the installer and many builders have been led to believe that these spacers can be tapped into place with the butt end of a wooden hammer. What happens is that the spacer seldom goes in correctly and can cause failure, instead of preventing it.
The current practice that is used in open-deck blocks like the B-series Honda block is to install a set of ductile iron sleeves. This isn’t anything new, as tuners have been using sleeves in domestic V-6 and V-8 blocks for a long time, and they have proven that the technique works.
Out of all the materials available for this purpose, ductile iron was chosen because of its strength and versatility. In the past, gray iron was considered to be the most versatile of all foundry metals because its high carbon content made it easy to melt and cast. It had a low shrinkage rate and a tensile strength up to 60,000 psi; but aluminum alloy, such as 2024 alloy, has a tensile strength rating up to 63,000 psi. While both have high tensile strengths, the resistance to fracture is high as temperatures increase.
Ductile iron is a graphitic metal that contains a high concentration of graphite spheres in its composition, unlike iron that contains flakes of graphite. If you have ever bent a graphite fishing rod or golf club, you know how strong it is. The same is true in ductile iron. It’s very resilient to fractures and cracking, while having 100,000 psi of tensile strength.
The sleeve of choice for many high-performance engine builders is the Darton sleeve. Darton uses sleeves that have been centrifugally cast, a process where molten ductile iron is evenly distributed over the interior of a mold that ensures proper thickness without voids left by traditional casting methods. This process affords the Darton sleeve tensile strength of 130,000 psi. Aside from being strong and resistant to cracking, ductile iron affords thermal resistance able to withstand temperatures as high as 800 degrees F, while being very resistant to corrosion.
Non-OEM blocks (like the Dart block) and welding of deck surfaces are outlawed by the NHRA. This ruling is a double-edged sword in a sense, as products like the Dart block would elevate the performance and power potential of B-series-powered vehicles. However, it also opens the doors for companies such as Dodge, General Motors, Ford and even McClaren to develop special engines for well-funded race teams. This could then make it virtually impossible for many racers to compete. Imagine a McClaren-powered Civic scorching the dragstrip. For now, blocks such as the Dart can be used on the street and racers will continue to use sleeved blocks because it is cost-effective, proven technology.
RS Machines in Carson, California, is one such shop that has been machining blocks and installing sleeves since 1996 and has grown to be the best-kept secret in import drag racing. Not because it innovated something that nobody else did, but because RS makes a quality product that the world’s best tuner racers trust.
In any form of competitive sport, the team that can maintain an advantage the best will always be successful and hard to beat. The team that keeps that advantage a secret the longest is even better off. This is exactly where RS Machines shines. Racers such as Bisi Ezerioha, Erick Aguilar and Jojo Callos use blocks prepped by RS Machines to dominate and smash records.
What does RS Machines do that is so special? We were curious too, so we dropped by the shop to cover the process of installing ductile iron sleeves that are guaranteed not to leak. Here’s what we found.Â
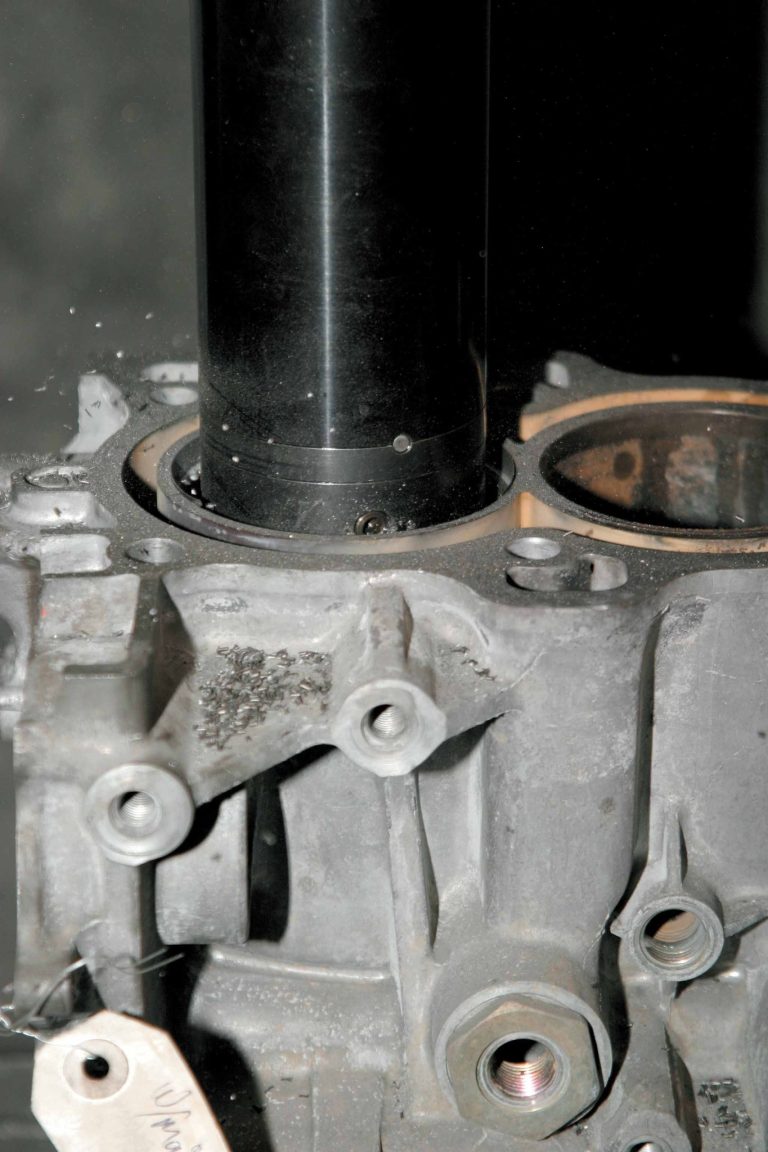
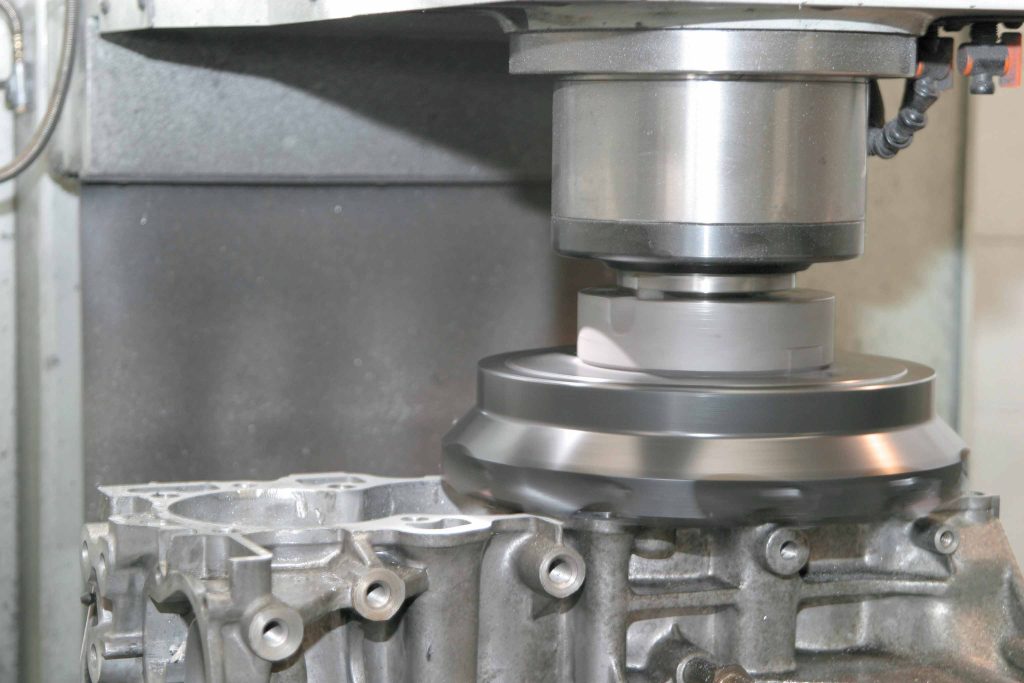
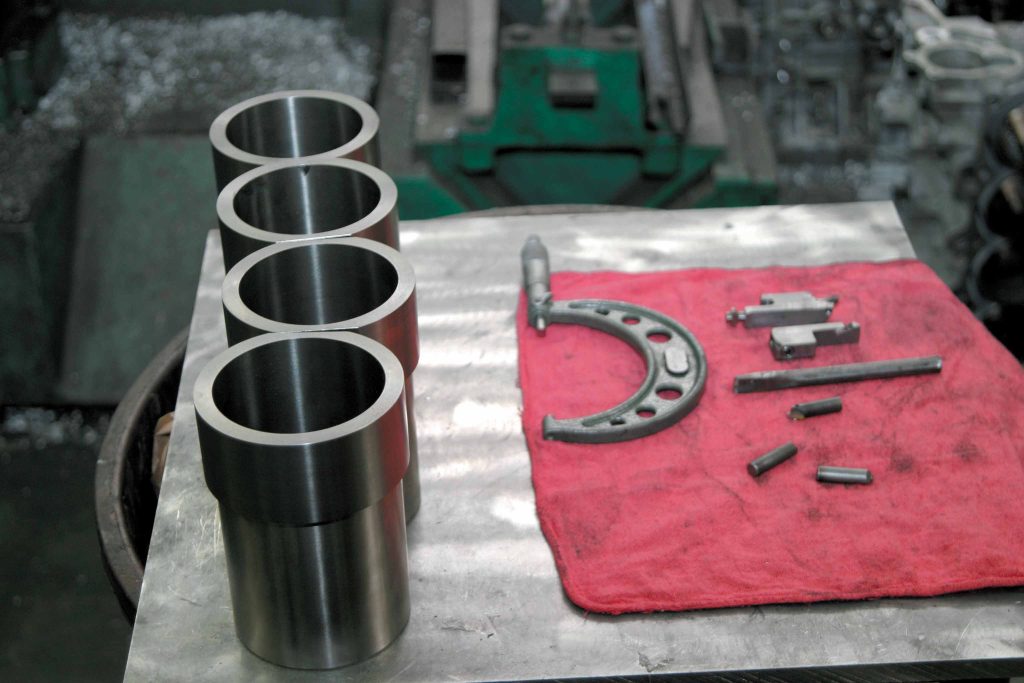
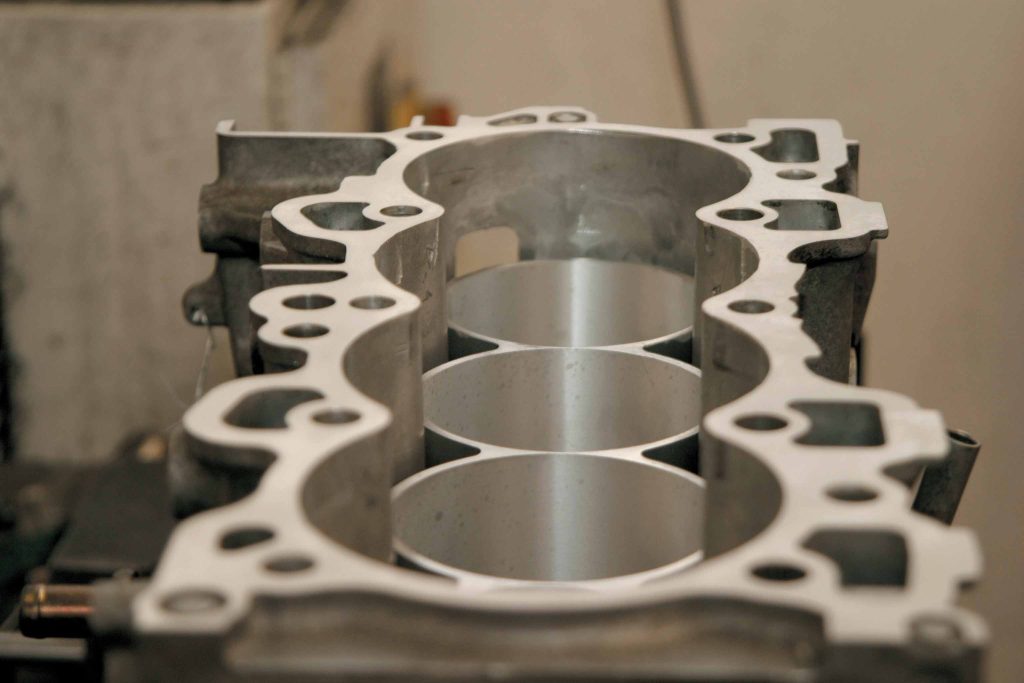
1. When the block has been removed and dried off, its stock cylinders are gradually bored out in steps to accept the new ductile iron sleeves. In this case, a set of sleeves with a bore of 3.18 inches and length of 5.5 inches were ordered from the Darton catalog (PN 200-014).
2. Once the precise boring process is completed, the block is resurfaced to ensure a proper seal at the head gasket. Several passes are performed. Each pass removes a certain amount of material, depending on the application of the engine and a customer’s needs. Since there are a number of competitors that have tried to copy this process, RS Machines keeps the details a secret; however, whenever any block is being built it’s not uncommon for 0.010 inch to be decked to ensure a perfect mating surface.
3. The Darton ductile iron sleeves are checked for bore accuracy with a micrometer (the instrument in the background) before installation.
4. The block has been removed from the resurfacing machine and is ready to accept the new sleeves.
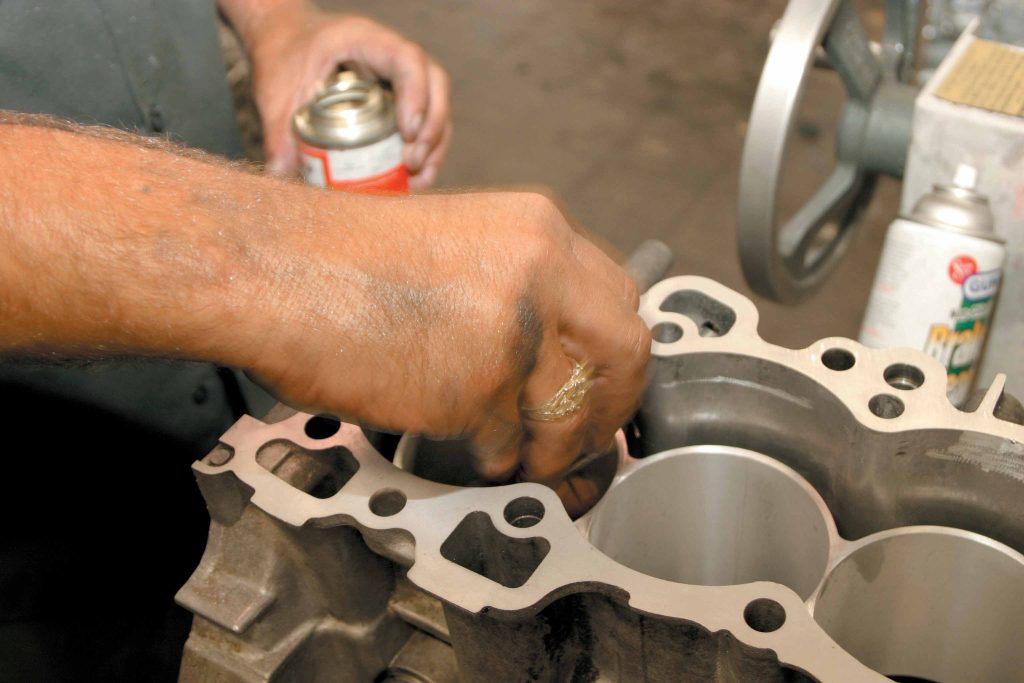
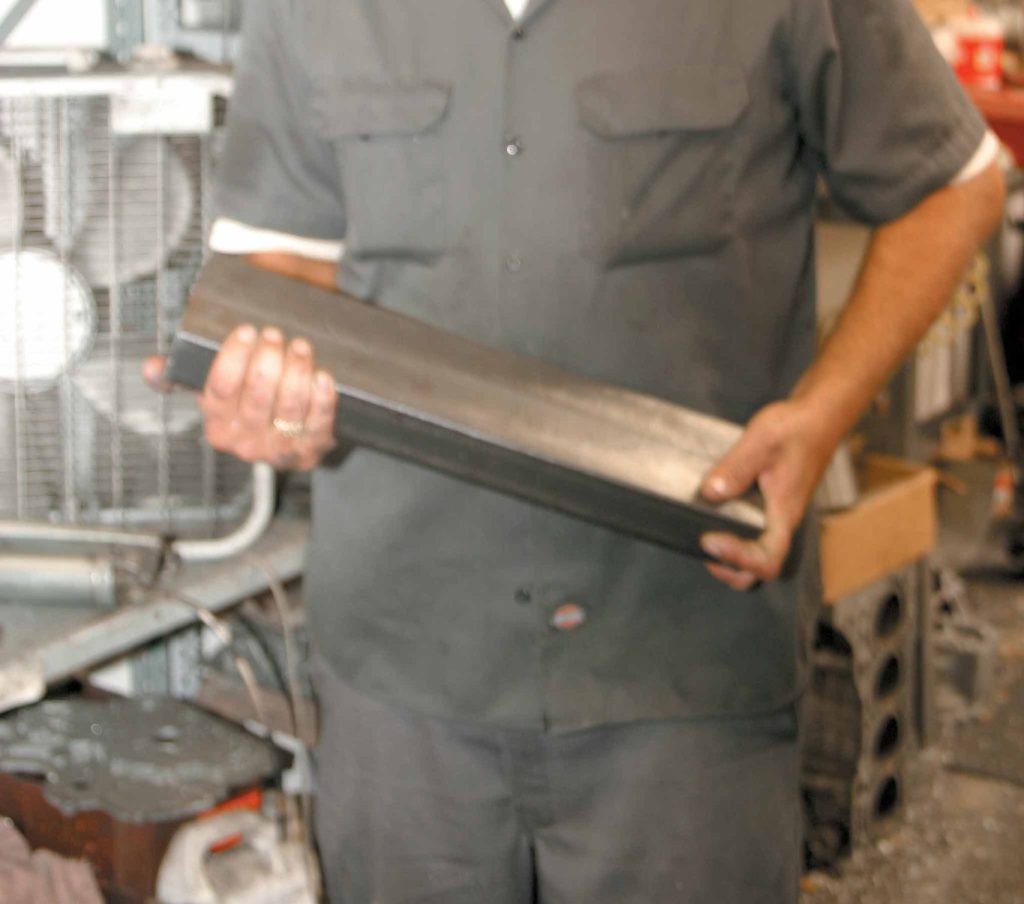
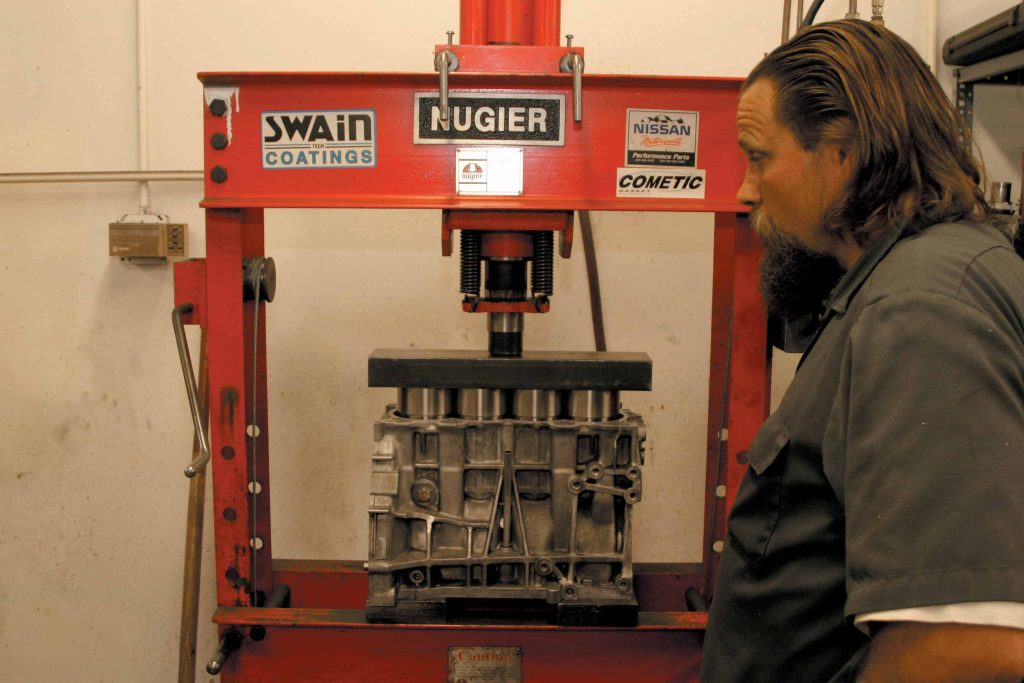
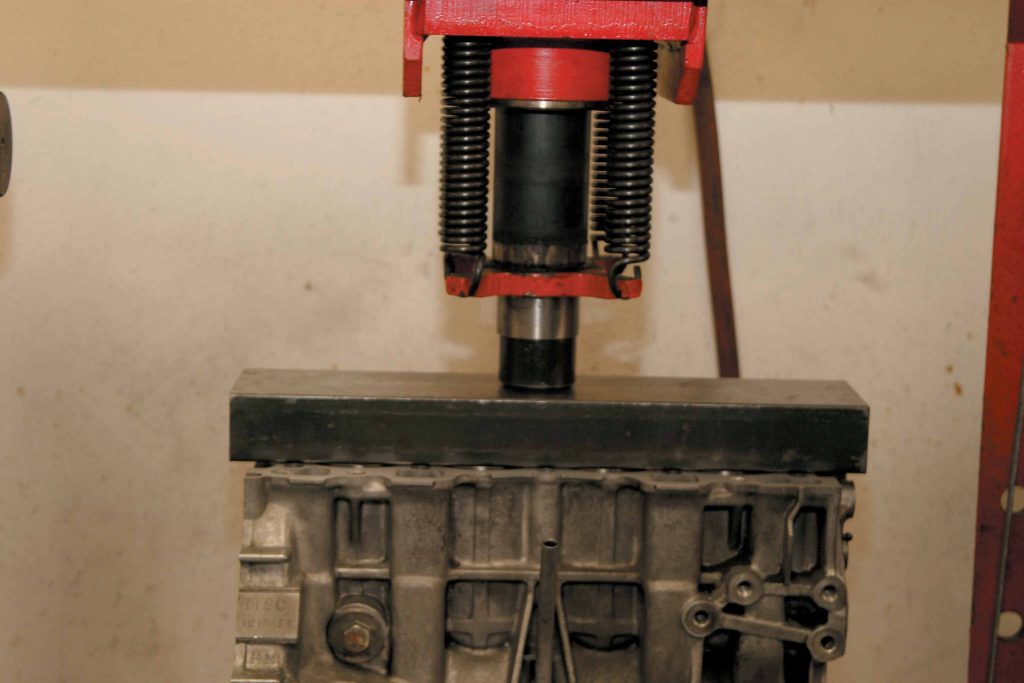
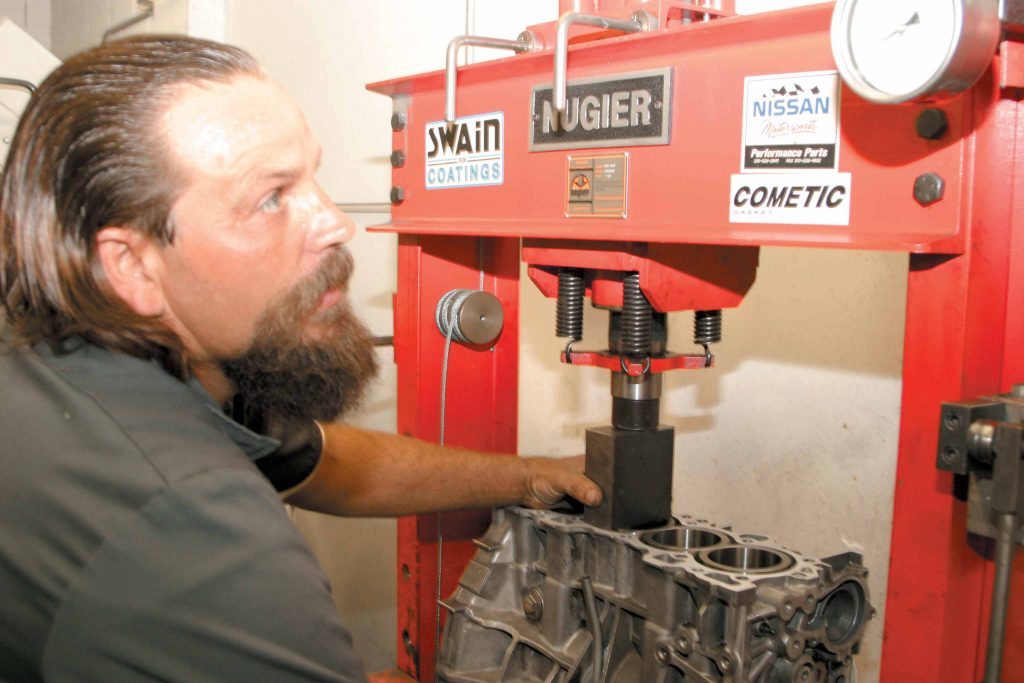
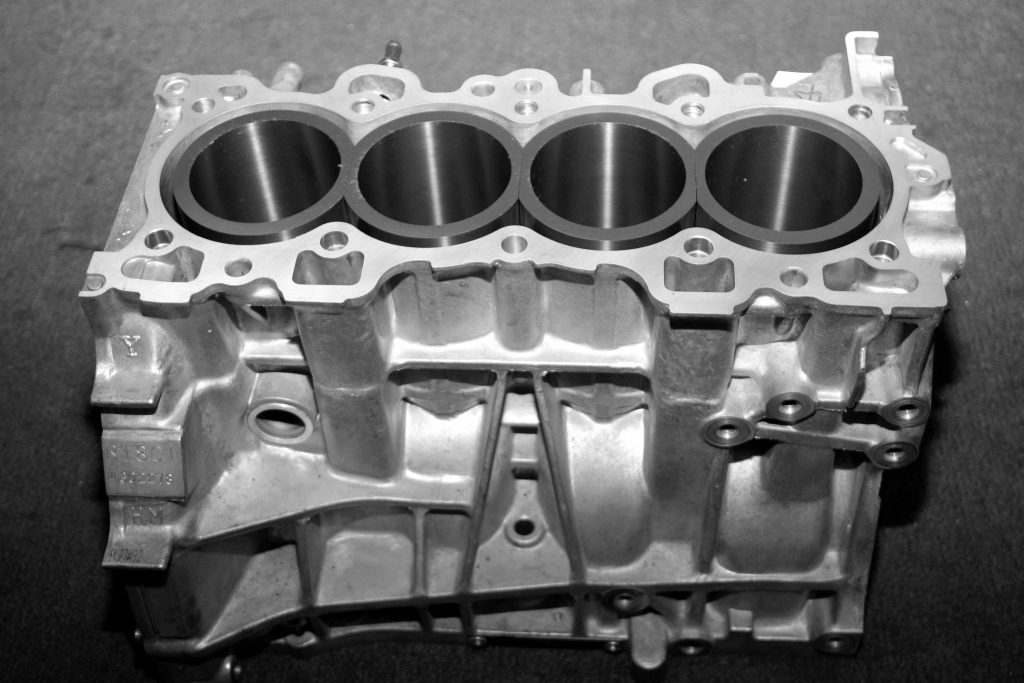
5. Before the sleeves can be installed, a special lubricant containing whale fat (from dead whales, we’re told) is applied to the inside of the remaining stock bores. This makes installing the sleeves easier.
6. RS Machines uses a hydraulic press to install the sleeves. The press exerts a force of 10 tons onto a heavy stock of iron to press all four sleeves into place. (For six-cylinders, a shorter piece is used.)
7. Observing the press in action.
8. The sleeves are slowly pressed into place under careful supervision. Once the sleeves are just about flush, the press is retracted and the sleeves are pressed in individually.
9. Using a smaller piece of iron, each sleeve is pressed in at a predetermined pressure. The bores are honed and the block is now ready to be reassembled.
10. Here is the finished product.
ARTICLE SOURCES
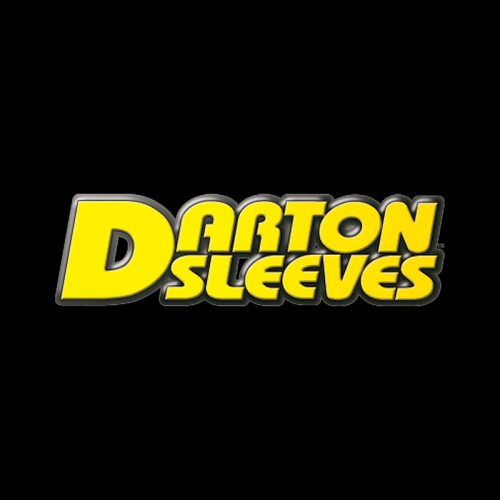
Darton Sleeves
2380 Camino Vida Roble, Building J & K
Carlsbad, CA. 92010
1-800-71-Darton