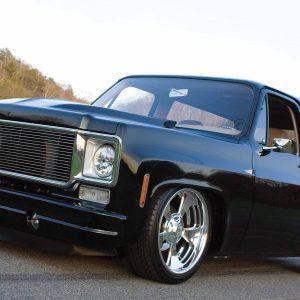
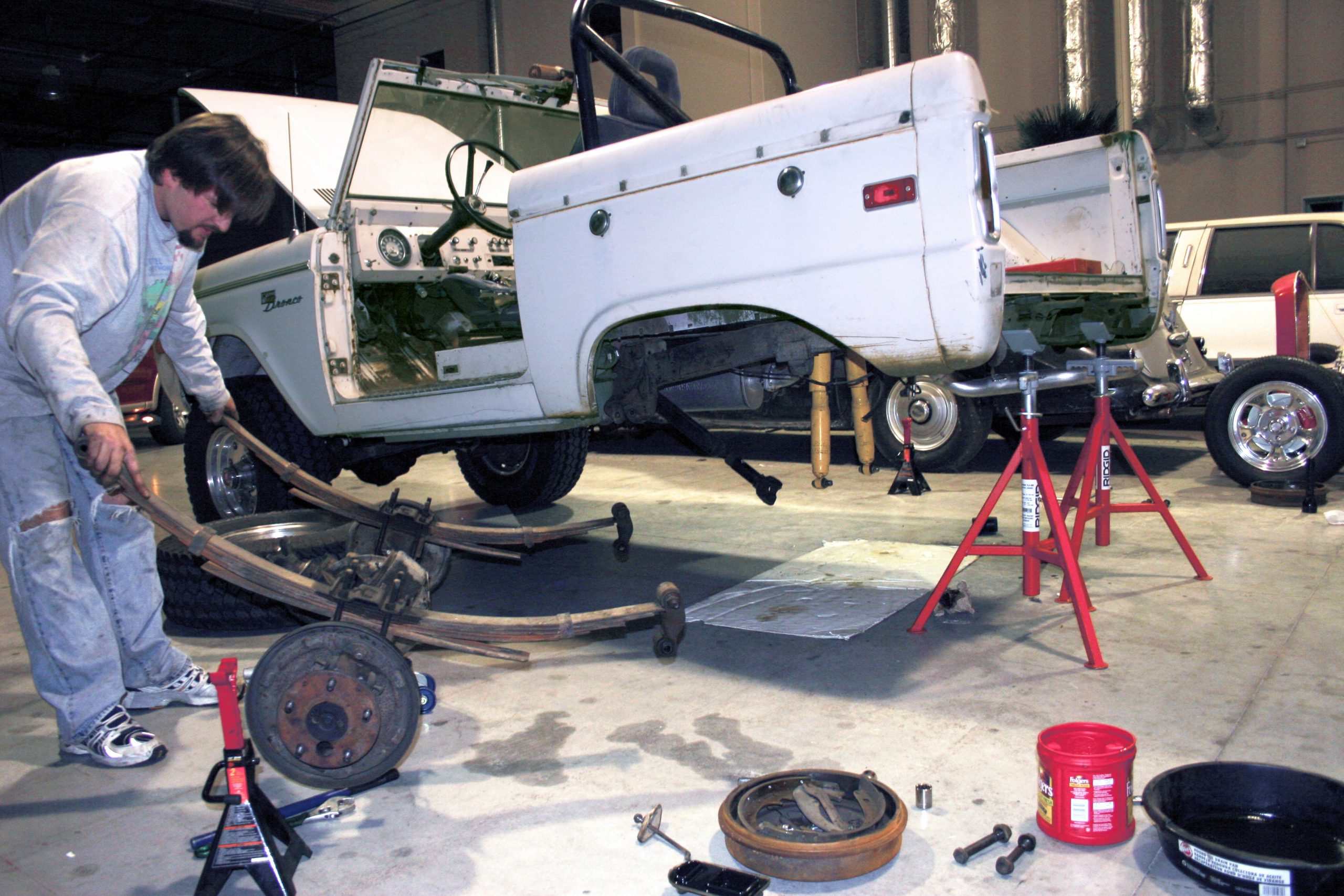
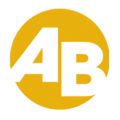
THE AUTO BUILDER
Featured
- All Post
- 20 High Priority - SR Super Rod
- Builds
- 25 High Priority - FB Ford Builder
- Cars
- 30 High Priority - AR American Rodder
- 01 Post Status
- 35 High Priority - RD Rodders Digest
- 40 High Priority - OTR On the Road
- 45 High Priority - SRB Street Rod Builder
- 50 High Priority - TB Truck Builder
- 55 High Priority - BSCENE Buckaroo Scene
- 60 High Priority - FPB Family Power Boat
- Trucks
- Swaps
- Performance Boats
- _000 Home Sliders
- Builders
- 00 Sidebars
- Manufacturers
- 05 High Priority - HCI Hot Compact Imports
- 05 Publications
- 10 High Priority - CR Chevy Rumble
- Back
- Chassis
- Engine
- Fuel System
- Electrical
- Exhaust
- Transmission / Drivetrain
- Suspension
- Steering
- Brakes
- Wheels and Tires
- Interior
- Exterior
- Accessories
- Power Adders
- Back
- Chassis
- Engine
- Fuel System
- Electrical
- Exhaust
- Transmission / Drivetrain
- Suspension
- Steering
- Brakes
- Wheels and Tires
- Interior
- Exterior
- Accessories
- Power Adders
- Back
- Chassis
- Engine
- Electrical
- Exhaust
- Fuel System
- Transmission / Drivetrain
- Suspension
- Steering
- Brakes
- Wheels and Tires
- Interior
- Exterior
- Accessories
- Power Adders
- Back
- Chassis
- Engine
- Electrical
- Exhaust
- Fuel System
- Transmission / Drivetrain
- Suspension
- Steering
- Brakes
- Wheels and Tires
- Interior
- Exterior
- Accessories
- Power Adders
- Back
- Chassis
- Engine
- Fuel System
- Electrical
- Exhaust
- Transmission / Drivetrain
- Suspension
- Steering
- Brakes
- Wheels and Tires
- Interior
- Exterior
- Accessories
- Power Adders
- Back
- Chassis
- Engine
- Fuel System
- Electrical
- Exhaust
- Transmission / Drivetrain
- Suspension
- Steering
- Brakes
- Wheels and Tires
- Interior
- Exterior
- Accessories
- Power Adders
- Back
- Chassis
- Engine
- Fuel System
- Electrical
- Exhaust
- Transmission / Drivetrain
- Suspension
- Steering
- Brakes
- Wheels and Tires
- Interior
- Exterior
- Accessories
- Power Adders
- Back
- Engine
- Fuel System
- Electrical
- Outdrives
- Steering
- Interior
- Accessories
- Power Adders
- Exterior and Hull
- Back
- Chassis
- Engine
- Electrical
- Exhaust
- Fuel System
- Transmission / Drivetrain
- Suspension
- Steering
- Brakes
- Wheels and Tires
- Interior
- Exterior
- Accessories
- Power Adders
- Back
- Chevrolet
- Cadillac
- Pontiac
- AMC
- Buick
- Jeep
- Lincoln
- Ford
- Honda
- GMC
- BMW
- Mitsubishi
- Dodge
- Nissan
- Chrysler
- Subaru
- Toyota
- Plymouth
- Mercury
- Volvo
- Volkswagen
- Oldsmobile
- Acura
- Back
- 05 Pub HCI Hot Compact Imports
- 15 Pub 4x4 4x4 Builder
- 20 Pub SR Super Rod
- 25 Pub FB Ford Builder
- 30 Pub AR American Rodder
- 35 Pub RD Rodders Digest
- 40 Pub OTR On the Road
- 55 Pub BSCENE Buckaroo Scene
- 10 Pub CR Chevy Rumble
- 50 Pub TB Truck Builder
- 60 Pub FPB Family Power Boat
- 45 Pub SRB Street Rod Builder
- Back
- Chip Foose
- Ring Brothers
- Jack Fuller
- Bob Cullipher
- Jerry Nichols
- Bobby Alloway
- Jesse James
- Carl Casper
- J.F. Launier
- Steve Sellers
- Boyd Coddington
- Rad Rides by Troy
- Cal Auto Creations
- George Barris
- West Coast Customs
- Back
- Street Rods
- Hot Rods
- Late Model
- Drag Race
- Handling
- Compact Cars
- Chassis
- Engine
- Fuel System
- Electrical
- Exhaust
- Transmission / Drivetrain
- Suspension
- Steering
- Brakes
- Wheels and Tires
- Interior
- Exterior
- Accessories
- Power Adders
- Chassis
- Engine
- Fuel System
- Electrical
- Exhaust
- Transmission / Drivetrain
- Suspension
- Steering
- Brakes
- Wheels and Tires
- Interior
- Exterior
- Accessories
- Power Adders
- Chassis
- Engine
- Electrical
- Exhaust
- Fuel System
- Transmission / Drivetrain
- Suspension
- Steering
- Brakes
- Wheels and Tires
- Interior
- Exterior
- Accessories
- Power Adders
- Chassis
- Engine
- Electrical
- Exhaust
- Fuel System
- Transmission / Drivetrain
- Suspension
- Steering
- Brakes
- Wheels and Tires
- Interior
- Exterior
- Accessories
- Power Adders
- Chassis
- Engine
- Electrical
- Exhaust
- Fuel System
- Transmission / Drivetrain
- Suspension
- Steering
- Brakes
- Wheels and Tires
- Interior
- Exterior
- Accessories
- Power Adders
- Chassis
- Engine
- Fuel System
- Electrical
- Exhaust
- Transmission / Drivetrain
- Suspension
- Steering
- Brakes
- Wheels and Tires
- Interior
- Exterior
- Accessories
- Power Adders
- Back
- 05 Post Imported
- 20 Post Missing Images (All)
- 25 Post Missing Images (Partial)
- 15 Post In Progress
- 30 Post Internal Review
- 40 Post On Hold
- 50 Post Approved
- 10 Post Images Imported
- 17 Post Missing TXT Files
- 18 Post Missing PDF Files
- 27 Post Missing Content
- Back
- Chassis
- Engine Swaps
- Interior Swaps
- Driveline
- Back
- Street Trucks
- OffRoad Trucks
- Chassis
- Engine
- Fuel System
- Electrical
- Exhaust
- Transmission / Drivetrain
- Suspension
- Steering
- Brakes
- Wheels and Tires
- Interior
- Exterior
- Accessories
- Power Adders
- Chassis
- Engine
- Fuel System
- Electrical
- Exhaust
- Transmission / Drivetrain
- Suspension
- Steering
- Brakes
- Wheels and Tires
- Interior
- Exterior
- Accessories
- Power Adders
- Back
- 01 Sidebar Left
- 01 Sidebar Right
Project BRONCAROO
Building A Modern Vintage Bronco
Author
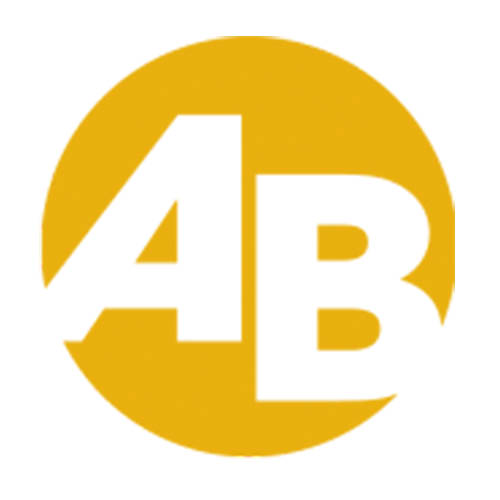
Steven Llorca
Photography by Brent Ross
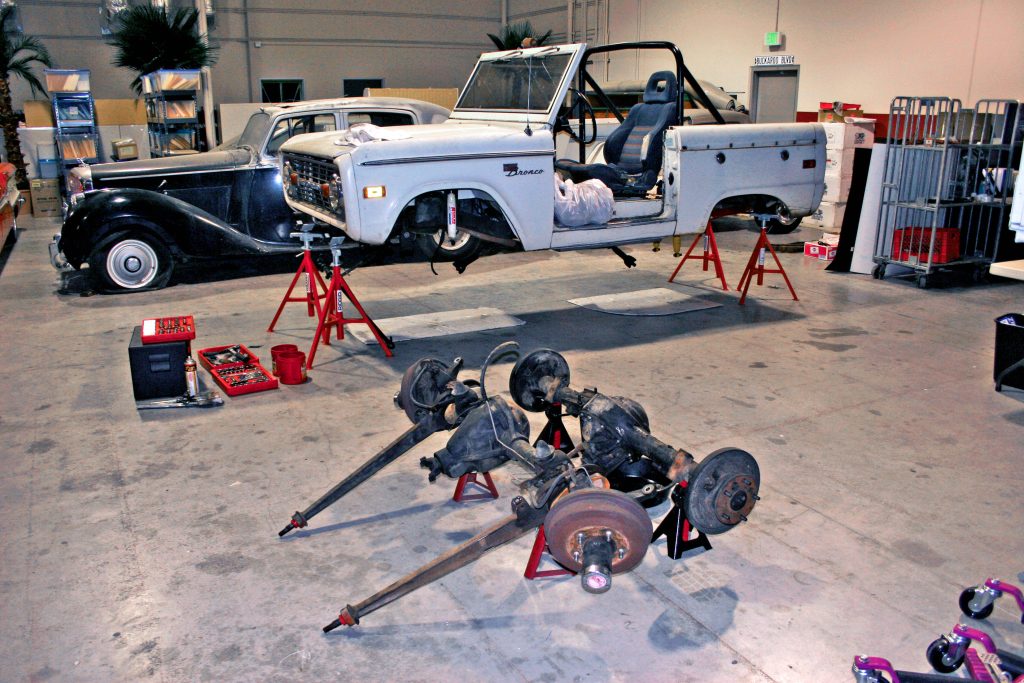
Today’s 4x4s have become extremely specialized. At one end of the spectrum are one-off, purpose-built, non-street-legal rock buggies. These are the cream of the rock crop. Most have tube chassis with what seems like nearly 360 degrees of axle articulation. Often the transfer cases are doubled up to produce crawl ratios way beyond the once magical 100:1. They’re obviously awesome, and capable of handling boulders as if they were speed bumps.
On the opposing end of the spectrum are the more common leather-clad, urban SUVs with their multiple DVD players and chromed 20-inch wheels. Steven Llorca wanted something more in the middle of these two extremes. Well, maybe not quite the middle; more like just a couple of notches to the street-legal side of the rock-buggy camp. He wanted a serious rocker capable of driving to the office and to the trail. What better project platform than the early Ford Bronco, which is arguably credited with starting both the SUV and the off-roading crazes?
Enter Broncaroo–Steven’s 1973 Ford Bronco project. In this installment, Broncaroo benefits from a heavy helping of stronger axles and low rock-crawling gears from Superior Axle & Gear. Air lockers from ARB will fill both differentials, and it’s all expertly put together by Coast Driveline & Gear in Ventura, California.
SHAFTED
Axles have it tough! Think about it: They are caught between the engine’s torque, which has been multiplied many times by the transmission, transfer case reduction and low final-drive gearing, only to have forces on the opposite end doing their best to resist the rotation. The resistance efforts come from many factors when four-wheelin’. The most obvious is the 4×4’s massive tires. In Broncaroo’s case, 37×12.5×17 Trail Ready tires will be beat against VW-size boulders. It is not uncommon for an axle under full torque to be twisted 180 degrees. Of course, as soon as the throttle is closed or the tires break traction, the load is diminished and the axles untwist, only to repeat the routine seconds later when everything hooks up again.
This constant twist-and-release action will work-harden the material over time. Once they’re work-hardened, the axles will resist twisting, and will break. Eventually, this will happen to even the best axles, but the best can handle a lot more before reaching this point. Experienced four-wheelers who use their 4x4s hard know how long axles will live in their vehicle. The smart ones then replace those axles shortly before they fail. They are easier to replace in the garage than on the trail. Upgrading to high-quality, larger-diameter aftermarket axles also greatly reduces failure opportunity.
Though the ’73-vintage Bronco came with a front Dana 44 and a Ford 9-inch rear, favorites of many four-wheelers, that doesn’t mean they cannot be improved. In fact, because they are so popular, there’s a lot of great products available to improve them further.
Here Steven turned to Superior Axle & Gear. It is among the largest axle manufacturers. It has OEM replacement axles as well as custom shafts with larger diameters, more splines, different bolt circles, and so on.
Superior’s axles are first forged and then machined, splined and heat-treated. Wrought in this fashion, the spline can be rolled on, a cold-form process in which the splines are formed under tons of pressure. Cold forming is said to produce superior grain structure as well as involute splines, which are the correct shape for factory side gears. The axle is then heat treated, resulting in much stronger splines compared to those that are cut.
LOCKED UP
Most first-generation Broncos, or any 4x4s for that matter, came with open differentials; a few were equipped with limited-slip diffs from the factory, while still fewer were found with OEM locking differentials of any style. So what’s an open differential? For street use, it is arguably the best style of differential to have.
The reason is because roads are not perfectly straight, and at some point in time you do need to turn. During a turn, the inside tire travels a shorter distance than does the tire across the axle on the outside of the turn. Since the outside tire swings a larger arc, it traverses a greater distance. To do so, the tire on the outside must rotate faster and a greater number times than the inside tire.
In the simplest of terms, through a series of internal gears, an open differential is designed to allow each wheel to turn independently, thus eliminating binding during cornering. This is ideal for use on pavement where smooth operation and long tire life, among other factors, are paramount.
Off-road, however, open diffs are not such a hot deal. When one tire loses traction, an open differential effectively directs all the engine torque to the spinning tire, rather than to the tire with traction, so momentum is lost. The clearest example of this is the two-wheel-drive vehicle that pulls off the shoulder of the road with the right-side tires in deep sand and the left-side tires firmly on asphalt. You’ve been there–the tires in the sand spin and bury themselves, while the ones on pavement do nothing. The vehicle does not move and is stuck. Obviously, the open differential is not the ideal type to use when venturing off-road.
The next differential up the off-road food chain is the limited slip .Limited-slip differentials use various mechanisms to allow open-differential-type action when going around turns; yet if a tire begins to spin, a limited-slip differential transfers more torque to the non-slipping tire. The most common limited slip accomplishes the torque transfer via spring pressure and clutches within the differential.
The king of the off-road hill is the locking differential, or lockers, as they are commonly called. Lockers work great off-road and can be installed in either the front or rear differential, or in both. They essentially lock both wheels of the same axle together so that engine torque is divided evenly at nearly all times. Climbing ability is improved amazingly. However, a locker will release one wheel when turning on high-traction surfaces, such as pavement, and act momentarily as an open differential. Depending on the locker and how it is set up, turning can be jerky and can heavily load all the axle components. If a locker is used at the front, steering can be heavy. However, these steering characteristics are not an issue in the dirt, where there is limited traction and slippage occurs. It is generally agreed that if you are going to install just one locker, it should be in the rear to gain the biggest off-road advantage, but some people who use their 4x4s often on the road prefer to place the locker in the front diff. Why? On pavement, the 4×4 will be in two-wheel drive, with the front hubs unlocked, so the locker will not affect ride or steering. If it were in the rear, it would. However, there are many rear lockers on the street, and one becomes accustomed to driving with them and having the inside tire chirp a bit.
There are two remaining differential types: spools and selectable lockers, the most common of which is the ARB air locker. Spools are popular in drag racing, where there is no turning and strength is at a premium. They are simply a solid piece of splined steel to accept the axles and join them as one. They do not have any differential properties.
The ARB is perhaps the most versatile of the differential styles. It accomplishes this without compromising or biasing performance toward the street or the rocks. An ARB air locker is a driver-controlled locking differential that can be switched on or off when extra traction is required. When it’s off, it acts as an open differential. When it’s switched on, it essentially becomes a spool, providing the ultimate in 4×4 traction. To use the system, the driver activates the air locker via a dash-mounted switch. Pneumatic (air) pressure supplied by an onboard 12-volt air compressor engages the locking mechanism within the air locker, thus preventing the wheels from turning independently. The air locker is deactivated by flicking the switch, returning the differential to normal. Depending on your application, an ARB can be installed in the either the front, back or both differentials.
For Broncaroo, Steven opted to go the ARB route both front and rear because of the superior performance it offers on- and off-road.
GEARING DOWN
To discuss gearing, we must first come to terms with gear jargon. Let’s see, higher is lower, so does that mean you go faster or slower? Gearing is expressed as a ratio–the ratio between the driven gear and the driving gear. In the case of differential gearing, we talk about the ratio formed by ring-and-pinion gears. The pinion gear is the driving gear, since it is motivated by engine torque routed to it through the driveline. The ring gear is turned by the pinion gear, so it is the driven gear. To learn the ratio, we divide the number of teeth on the pinion gear into the number of ring-gear teeth. Hence, if the ring gear has 30 teeth and the pinion gear has 11 (30 / 11 = 2.72), we have a 2.72:1 gear set, more commonly known as 2.73s due to rounding off. Let’s look at another set of ring and pinion gears with 39 and 8 teeth, respectively (39/8 = 4.875, or a ratio of 4.88:1). So which is a higher gear set, 2.72 or 4.88? Well, the 4.88s are the higher ratio numerically, but they are actually the lower gears when measured in terms of road speed verses engine rpm. The 4.88s also produce the greatest torque multiplication. Perhaps this analogy will help to make it clearer: The lowest/slowest gear in a transmission is first gear, but numerically it will have the highest, or largest, number. If our two ratio examples were in a transmission, the 4.88:1 would be first gear, while the 2.73:1 would be about third gear. So let’s agree to call the higher numerical ratios the lower gears.
It was not that long ago that gearing was pretty simple–but limiting. Most truck tires were measured in inches, and if you installed tires that were 10 percent larger in diameter, you would install ring-and-pinion gears that were 10 percent lower. Many manufacturers’ gears went only as low as 4.10:1. The world has changed, of course. Final-drive ratios have become very deep, but the larger part of the picture is the availability of overdrive transmissions combined with low first-gear ratios. The five-speed NV4500 with a 6.34:1 first-gear ratio and .73:1 overdrive is just one example that comes to mind. The 700R4 is also a hot transmission now, due to the aftermarket. It has a 3.06:1 first-gear ratio and a .07:1 overdrive and is a good choice for the auto crowd.
Aftermarket manufacturers such as Advance Adapters, JP and others make adapters to bolt these to nearly any engine or transfer case we can imagine. Likewise, many companies offer low-range transfer case gears in the 4:1 to 5:1 range. Some awesome crawl ratios are now easily achieved while retaining an acceptable highway gear. Crawl ratio is the final reduction after all gearing. It is easily calculated by simply multiplying all the ratios together. Take a 6.34 first-gear ratio, a 5.0 low range and 4.88 gears and you get 154:1! Crawl ratios starting at or lower than 45:1 are acceptable for all but the most serious of rock crawlers. Now that we have deep first gears, overdrives and 5:1 transfer cases, we no longer have to bias our final-drive choice in favor of either a low crawl ratio and lots of engine rpm on the road or decent highway rpm and steeper gearing off-road.
These factors don’t necessarily negate the need to change gears when going to larger rubber; we just want to give you some other things to think about rather than simply referring to some old gearing chart from the ’80s. Those old charts still work, despite new math. However, they do not allow for modern transmissions and a very creative and aggressive aftermarket full of alternate tranny and T-case gearing and the ability to swap almost anything anywhere.
Rather than bog you down with a bunch of mind-numbing formulas for converting metric-size tires to inches or calculating engine rpm verses mph for a given tire and gear, among many other needed calculations, we’re going to point you to the internet. We sat here compiling all the math and our brains froze over. However, many of the gear and tire companies have really cool calculators that allow one to quickly compare all the gearing considerations and options. We have listed just a few for you.
Use the chart below to confirm the gear ratio of your gear set. Match the number of teeth on the pinion gear with the number of teeth on the ring gear. The ratio can also be determined by dividing the number of teeth on the driven (ring) gear by the number of teeth on the pinion (drive) gear. If you are wondering what ratio is in your truck and the housing is not tagged or the door tag does not show it, you can get a pretty close approximation by lifting both wheels of the same axle off the ground and then rotating the wheel one full turn and counting how many times the driveshaft spins. To do this, the transmission or transfer case must be in neutral and the vehicle must be properly blocked to prevent rolling.
| 5 | 6 | 7 | 8 | 9 | 10 | 11 | 12 | 13 | 14 | 15 |
21 | 4.20 | 3.50 | 3.00 | 2.63 | | | | | | | |
22 | 4.40 | 3.67 | 3.14 | 2.75 | 2.44 | | | | | | |
23 | 4.60 | 3.83 | 3.29 | 2.88 | 2.56 | | | | | | |
24 | 4.80 | 4.00 | 3.43 | 3.00 | 2.67 | | | | | | |
25 | 5.00 | 4.17 | 3.57 | 3.13 | 2.78 | 2.50 | | | | | |
26 | 5.20 | 4.33 | 3.71 | 3.25 | 2.89 | 2.60 | | | | | |
27 | 5.40 | 4.50 | 3.86 | 3.38 | 3.00 | 2.70 | 2.45 | | | | |
28 | 5.60 | 4.67 | 4.00 | 3.50 | 3.11 | 2.80 | 2.55 | | | | |
29 | 5.80 | 4.83 | 4.14 | 3.63 | 3.22 | 2.90 | 2.64 | 2.42 | | | |
30 | 6.00 | 5.00 | 4.29 | 3.75 | 3.33 | 3.00 | 2.73 | 2.50 | | | |
31 | 6.20 | 5.17 | 4.43 | 3.88 | 3.44 | 3.10 | 2.82 | 2.58 | | | |
32 | 6.40 | 5.33 | 4.57 | 4.00 | 3.56 | 3.20 | 2.91 | 2.67 | 2.46 | | |
33 | 6.60 | 5.50 | 4.71 | 4.13 | 3.67 | 3.30 | 3.00 | 2.75 | 2.54 | | |
34 | 6.80 | 5.67 | 4.86 | 4.25 | 3.78 | 3.40 | 3.09 | 2.83 | 2.62 | 2.43 | |
35 | 7.00 | 5.83 | 5.00 | 4.38 | 3.89 | 3.50 | 3.18 | 2.92 | 2.69 | 2.50 | |
36 | 7.20 | 6.00 | 5.14 | 4.50 | 4.00 | 3.60 | 3.27 | 3.00 | 2.77 | 2.57 | |
37 | 7.40 | 6.17 | 5.29 | 4.63 | 4.11 | 3.70 | 3.36 | 3.08 | 2.85 | 2.64 | 2.47 |
38 | 7.60 | 6.33 | 5.43 | 4.75 | 4.22 | 3.80 | 3.45 | 3.17 | 2.92 | 2.71 | 2.53 |
39 | 7.80 | 6.50 | 5.57 | 4.88 | 4.33 | 3.90 | 3.55 | 3.25 | 3.00 | 2.79 | 2.60 |
40 | | 6.67 | 5.71 | 5.00 | 4.44 | 4.00 | 3.64 | 3.33 | 3.08 | 2.86 | 2.67 |
41 | | 6.83 | 5.86 | 5.13 | 4.56 | 4.10 | 3.73 | 3.42 | 3.15 | 2.93 | 2.73 |
42 | | 7.00 | 6.00 | 5.25 | 4.67 | 4.20 | 3.82 | 3.50 | 3.23 | 3.00 | 2.80 |
43 | | 7.17 | 6.14 | 5.38 | 4.78 | 4.30 | 3.91 | 3.58 | 3.31 | 3.07 | 2.87 |
44 | | 7.33 | 6.29 | 5.50 | 4.89 | 4.40 | 4.00 | 3.67 | 3.38 | 3.14 | 2.93 |
45 | | 7.50 | 6.43 | 5.63 | 5.00 | 4.50 | 4.09 | 3.75 | 3.46 | 3.21 | 3.00 |
46 | | 7.67 | 6.57 | 5.75 | 5.11 | 4.60 | 4.18 | 3.83 | 3.54 | 3.29 | 3.07 |
47 | | | 6.71 | 5.88 | 5.22 | 4.70 | 4.27 | 3.92 | 3.62 | 3.36 | 3.13 |
48 | | | 6.86 | 6.00 | 5.33 | 4.80 | 4.36 | 4.00 | 3.69 | 3.43 | 3.20 |
49 | | | 7.00 | 6.13 | 5.44 | 4.90 | 4.45 | 4.08 | 3.77 | 3.50 | 3.27 |
50 | | | 7.14 | 6.25 | 5.56 | 5.00 | 4.55 | 4.17 | 3.85 | 3.57 | 3.33 |
51 | | | 7.29 | 6.38 | 5.67 | 5.10 | 4.64 | 4.25 | 3.92 | 3.64 | 3.40 |
52 | | | 7.43 | 6.50 | 5.78 | 5.20 | 4.73 | 4.33 | 4.00 | 3.71 | 3.47 |
53 | | | 7.57 | 6.63 | 5.89 | 5.30 | 4.82 | 4.42 | 4.08 | 3.79 | 3.53 |
GET IT TOGETHER
Here’s a look at what it took to put it all together for Broncaroo.
1) The ’73 Bronco uses a Dana 44 differential/axle assembly at the front. It is among the most desirable. Here it’s been fully disassembled and secured to one of Coast Driveline’s assembly stands. Mark at Coast Driveline suggested hanging on to the original shims to use them as mock-up shims during the setup stage. Also, since the shim that controls pinion depth is beneath the pinion bearing, the bearing must be pressed on and off to add or remove shims when setting the proper depth. Therefore, Mark suggested that the inside diameter of the old pinion bearing be lightly sanded until it slides on and off the pinion shaft. This will allow quick and easy checking for correct pinion depth without damaging the new replacement bearing from pressing it on and off the pinion shaft.
2) Since an ARB will be installed, we must poke a hole into the top of the centersection for the ARB air line. A small-diameter pilot hole is drilled first, followed by the correct-size finish drill. Since this hole requires a threaded fitting, it is important to use the correct drill size for the anticipated tap.
3) Once the air-line hole is drilled and tapped, the entire housing and all other parts are thoroughly cleaned. Mark stressed the importance of thoroughly cleaning every surface before starting the installation. He’s seen many home rebuilds fail simply from poor cleaning or from exterior grit introduced during the rebuild. To ensure proper sealing, Teflon tape is applied to the air-line fitting and the fitting is threaded into the housing.
4) Never install a new bearing into the old bearing race, because it can be tricky to remove an old race. Race pullers can often be rented, or a locale shop can pull the race for you. However, generally they can be tapped out from the inside. Take care not to gouge the race support area of the housing. Here a new race is installed using an aluminum driver that was the same outside diameter as the race. Other-style drivers may have the same taper as the bearing race. They must be made of a soft material to prevent damaging the bearing surface of the race.
5) This is a look at the pinion gear with the outer bearing installed. As mentioned before, since the depth-controlling shim goes beneath the gear, often the bearing must be installed and removed several times to achieve the correct measurement. This is where using the slightly enlarged mock-up bearing is helpful. Also note the preload shims.
6) The pinion gear with the inner bearing installed slides into the Dana 44 from inside the housing.
7) To start, use the same number of shims as did the original gear. This will provide a good baseline from which to start.
8) Next comes the mock-up bearing with a slightly enlarged inside diameter for easy installation and removal.
9) This is what all the preload shimming comes down to: measuring the amount of drag or preload on the pinion shaft. Preload is measured using an inch-pound torque wrench. The Dana 44 generally runs between 18 and 20 inch-pounds of preload. However, check your gear manufacturer’s instructions for its specifications. To achieve the proper preload, you will likely need to change preload shims and check the torque again. You may need to repeat these steps several times. During this inspection process, use the old yoke nut and torque it to 65 ft-lb.
10) With the proper preload set, you can remove the mock-up bearing and install the fresh ones. Steven ordered his Superior gears with the full Master Bearing set. This kit comes with everything new: bolts, seals, Temkin bearings and so on. A special tool that mates with the bearing section was used to tap the outer bearing onto the pinion shaft.
11) Some Dana 44s call for an oil deflector, while others do not. If your bearing set came with one, use it. It helps to direct oil to the bearing. However, do not stress about it if one was not included.
12) Now the seal is installed. It was not in place during the preload setup. If it were, it likely would have become damaged. Its sealing surface must be thoroughly greased where it rides against the yoke, otherwise it will wear and fail prematurely. Once failed, the pinion shaft will leak its lubricating fluid, as well as permitting water, sand and other undesirables to enter the housing.
13) For the final installation of the yoke, thoroughly grease the splines. This time you’ll use a new yoke nut and torque it to about 95 ft-lb, but check the torque specs from your manufacturer first.
14) The 4.88:1 Superior Axle & Gear ring gear is bolted onto the ARB air locker using new ring-gear bolts. It is important to tighten these bolts to the manufacturer’s specifications (both torque and pattern) and to use a thread-locking agent. Use a high-quality torque wrench to ensure accurate and consistent readings. However, even high-end wrenches must be occasionally calibrated, especially when used daily or if they have been dropped. The ARB is activated from one side. Here the air-supply collar with its air line attached is slipped into place. O-rings prevent air pressure from escaping while keeping differential fluid out. Care must be taken not to damage these O-rings or the soldered-on air line. Though extremely durable in application, they are easily damaged during installation if one is not careful.
15) The ARB is the heart of the differential, completely replacing the OEM ring-gear carrier and spider gears. When first installing the ARB, shim it so that it is a zero-clearance fit with the housing. Then lightly tap it into place using a rubber mallet. The zero-clearance is intentionally loose to make it easier to remove the carrier later on when we make shim adjustments. Depending on the application, it may be necessary to notch the bearing hold-down cap to allow passage of the air line.
16) With the ARB thoroughly seated, the bearing saddle caps are installed. Ensure that they are sitting flush and square and then torque them to about one half the recommended final spec for this mock/test stage. The saddle cap bolts have a shoulder, so care must be taken to ensure they are properly centered before you start cranking down on them. These saddle caps are not unlike the main bearing caps of an engine’s crankshaft. They were line bored, so they are matched to the housing. They have a specific location and orientation. They are marked from the factory, but at disassembly you may wish to make your own marks for left, right, top and bottom.
17) Backlash is measured using a dial indicator. The dial gauge must be firmly mounted to ensure accurate and consistent measurements. The tip of the dial gauge is placed on the outer end of the drive side of a ring-gear tooth. The desired backlash is generally etched into the ring gear and is available in the installation instructions. However, Dana 44s normally call for no more than .010 and no less than .006 inch of backlash. Optimum is usually .008 inch. This backlash is adjusted by moving the ring gear to the left or right as needed. The movement is accomplished by moving shims from one side to the other or changing shim size.
18) When you’re happy with the dial-indicator readings, the next step is to confirm what the gauge told you. You run a pattern by applying a special “paint” to the ring-gear teeth and then rotating the ring gear until the pinion gear leaves a contact pattern on it. Shown is the proper pattern on the coast side of the ring gear.
19) The drive side pattern is the final word. Here’s what you want to see. Getting this to look right is crucial to setting up a long-running ring-and-pinion set. Remember that during this mockup stage we installed the ARB into the housing with a zero-clearance fit? Well, now that we have juggled shims to get the proper pattern, we must tighten up the ARB or carrier’s overall fit into the housing. This is done by adding .004-inch worth of shims to each side of the carrier.
20) Until now the axle-tube seals have not been installed to prevent them from getting damaged while repeatedly pulling the carrier in and out to adjust shims. Here the seals are installed using a simple tool to seat them fully without nicking or otherwise destroying them. The tool is simply a nut and bolt that applies pressure on two spacers as the nut is turned. You can easily make one yourself.
22) We’re down to the final few steps. Carefully bend the copper air line and route it to the previously installed fitting in the housing. The tube cannot be allowed to contact any moving parts within the housing. Also keep in mind the contour of the cover so that the air line does not chafe against the inside or get pinched between the cover and the housing. Do not kink the line.
23) Here the copper tube protrudes slightly from the housing fitting. The plastic blue air line supplied in the ARB compressor kit will join the compressor to this fitting. The blue line must be carefully routed and tied to the chassis where it will not chafe or become damaged by trail obstacles and brush. An air leak will result in no locker. Some people swap the plastic line for much more expensive and more durable braided steel line, or even steel brake-line tubing where flexibility is not needed.
27) The 9-inch Ford axle has real performance advantages over most axles. It is incredibly strong, and the aftermarket is full of upgrades and optional gear ratios. Steven chose the industry-standard Currie 9+ carrier. The 9+ is as strong as it gets for 4×4 applications. The Ford 9-inch is also cool because the third member can be assembled on the bench and then slipped into the main axle housing.
33) For illustration purposes, the pinion assembly is slid into the 9+ carrier to help show where the rear pinion support bearing will be pressed into the carrier. In addition to the Currie parts being much stronger than the OEM stuff, another advantage to their use is that they are beefier castings, precision machined using modern processes, rather than being some 25-year-old part with unknown history.
36) The Superior ring gear is bolted to the ARB and the outer support bearings are installed. Mark likes to use a thread-locking agent on all of the internal fasteners. The ARB assembly is set into the carrier. Mark recommends carefully cleaning all new parts. New differential parts are coated with a cosmalene-like coating to protect them from corrosion during shipping. This oily coating attracts dust and grit that could damage parts or prevent them from seating correctly. It also limits the effectiveness of thread-locking agents.
37) These are the threaded adjuster rings or expander rings that move the ARB/ring gear from side to side to adjust the running pattern. They do the same job as the shims we installed on the Dana 44. In this photo, one can see the thicker expander ring of the 9+ compared to the wimpy stock ring. When you order a 9+ and intend to use an ARB, be sure to let Currie know because the adjuster rings are different for ARB applications.
41) As with the Dana, position a dial gauge at the tip of a ring-gear tooth. The ring gear will be marked with the recommended backlash. The manufacturer usually specifies about .008 inch. Confirm the running pattern, with the drive side being the final word. The drive side is the outside radius of the teeth. Once adjusted, torque the saddle bolts to 75 ft-lb.
ARTICLE SOURCES
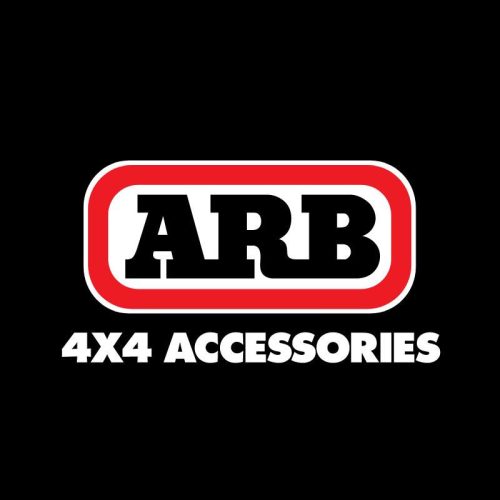
ARB 4x4 Accessories
20 South Spokane St.
Seattle, WA 98134
206/264-1669
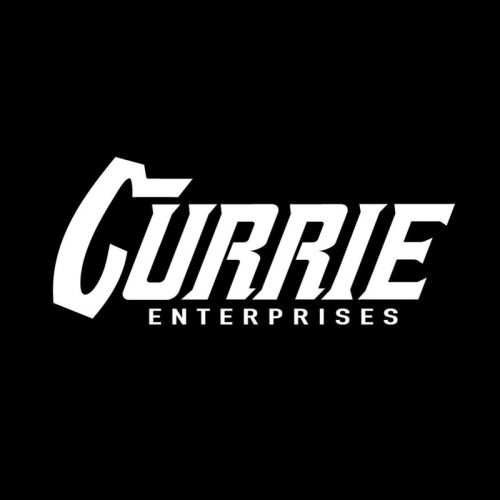
Currie Enterprises Inc.
1480 North Tustin Ave.
Anaheim, CA 92807
714-528-6957
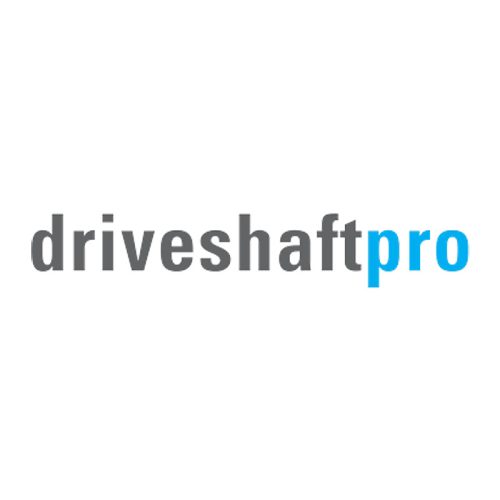
Driveshaft Pro
formerly Coast Driveline & Gear
2495 Palma Dr.
Ventura, CA 93003
(805) 656-0285
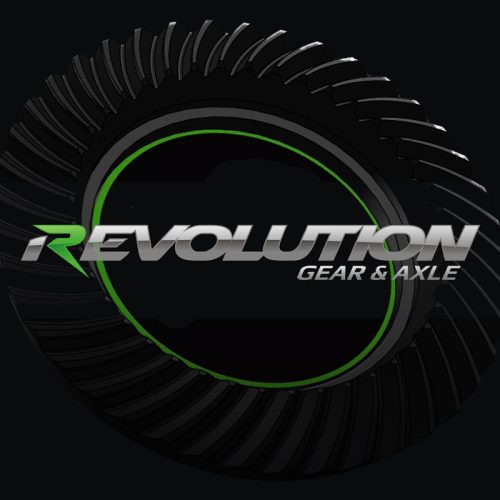
Revolution Gear & Axle
formerly Superior Axle & Gear
844/213-4327