A LOOK AT POWER WINDOWS AND ELECTRIC WIPERS BY SPECIALTY POWER WINDOWS
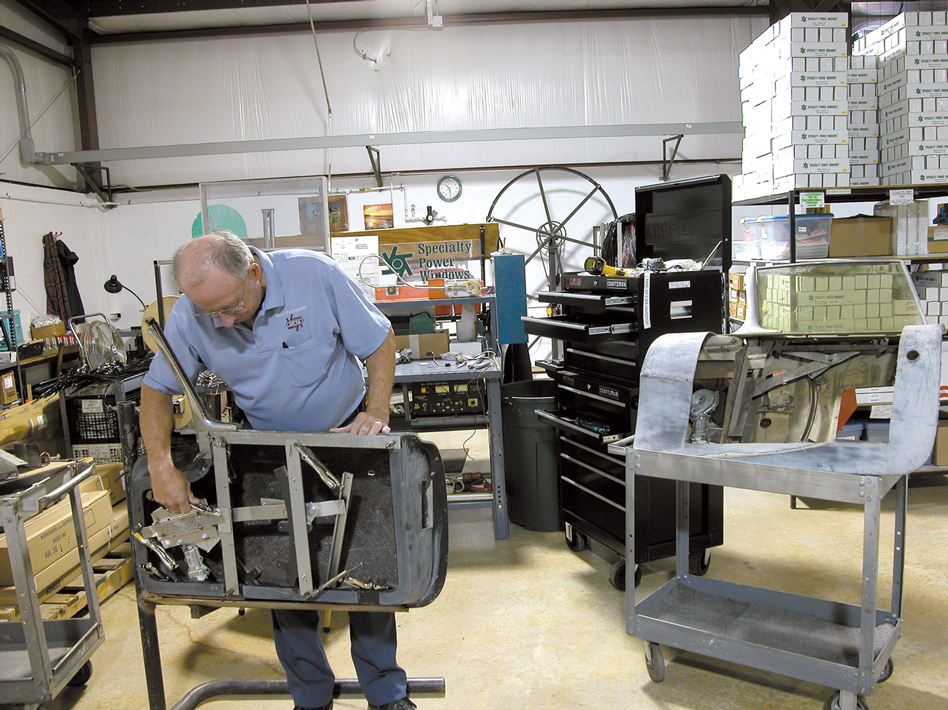
There was a time not all that long ago, between station wagons and SUVs, when big conversion vans were the family transportation of choice. In the beginning, the Big Three considered vans to be commercial vehicles, fitted with rubber floor mats, vinyl seats and short (if any) side windows, not the decked-out, posh family transport they would become. Indiana, Georgia, north Florida and a couple of other areas became production centers for van conversions. Starting with the stripped-down utilitarian vehicles, converters added full interiors, swiveling captainʼs chairs, big windows, tables and more. Because Dodge, Chevy and Ford considered the vehicles to be strictly utilitarian, they didnʼt bother to design any of the components needed for the conversions, so a thriving cottage industry sprang up to supply seats, picture windows, lighting systems and all the other options needed by the prototype soccer moms.
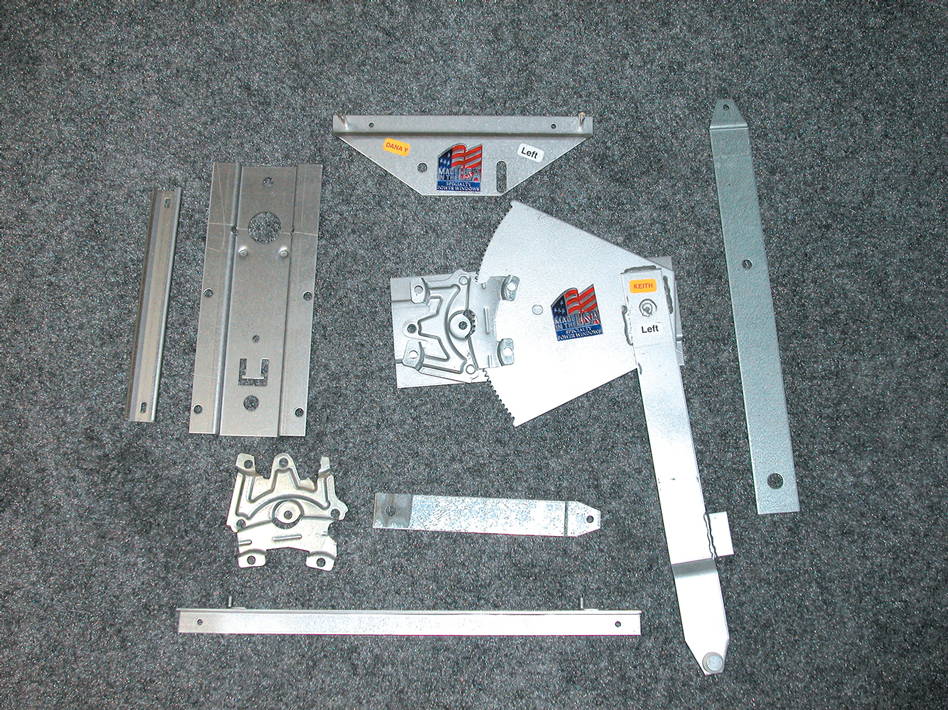
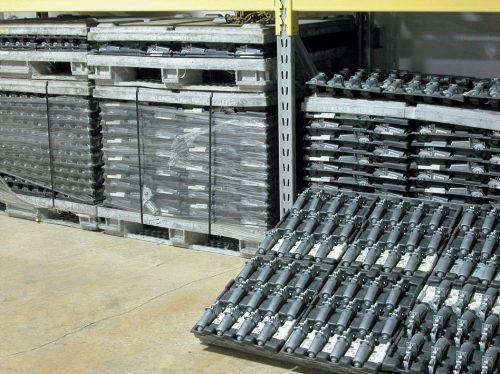
In 1986, Ervin and Louise Castlebery got out of the body shop business and started supplying van conversion companies with power window lift mechanisms designed specifically for the vansʼ front doors. The Forsyth, Georgia, business thrived, right up until the Big Three decided that they were missing some market share by not offering their own conversion vans and, of course, the components to convert them. Overnight the Castleberysʼ market went away. Soon after, the conversion van was done in by SUVs, putting the final nail in the conversion van industryʼs coffin.
Ervin had always been a car guy, and since he was set up as a production manufacturing facility, capable of designing and building OE-quality power window lift systems, complete with all the tracks and lift components, it wasnʼt much of a jump to begin offering kits to the street rod marketplace. Specialty Power Windows (SPW) units are designed with window regulators, lifts and glass channels manufactured in-house—not just a motor and switches that you connect to your existing mechanisms. The motors are new factory GM parts, left and right specific, with OE connector plugs and switches, and SPW designs its lift and track systems around these.
Several model-specific kits are available, as well as “universal” kits that, by virtue of an ingenious design, are readily adapted to almost any application. Rather than employing the traditional window regulators and scissors arms to raise and lower the window, they employ a flexible cable to push or pull the window up and down the track. The electric motor mounts at the lower end of the track, and both the top end of the track and the cable are cut to the length you need for your application. Basically, your job is to mount the track, cut it and the cable to length, mount the switch and run the wires. For its vent window delete/one-piece glass conversion kits, SPW even supplies templates for cutting the new glass.
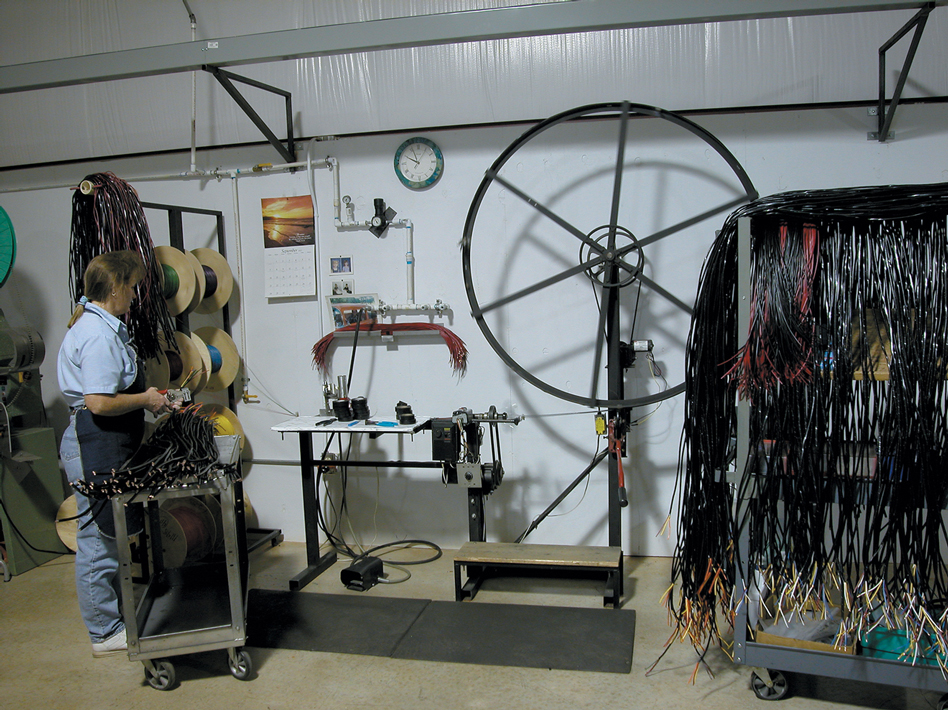
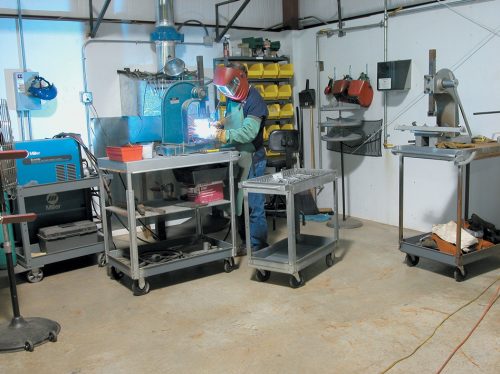
This is perhaps one of the most ingenious machines we’ve ever seen. Robby and his father built it years ago, allowing SPW to make all of its wiring harnesses in-house, rather than farming them out. Wire is drawn off spools on the left and pulled through a ring to group the wires tightly together. The wire bundle is attached to the outside rim of the angle-iron wheel, which is rotated by an electric motor. As the wheel turns, it pulls the wire off the spools. Just ahead of the wheel, the wire is pulled through a rotating head that holds a roll of electrical harness tape. The head is driven by a second motor, rolling the whole roll of tape around the wire. The wire is drawn through a hole in the center of this head, with the tape rotating around the hole, wrapping the wires as they are pulled through. The large wheel is calibrated around the perimeter with different lengths marked off for different applications, and it stops automatically when the specified length of wire has been pulled. The now-wrapped wires are cut off and hung on a cart, which is then moved to another station where the ends are stripped and the proper connectors are crimped on.
Several jigs are used to assemble and hold the tracks, lifts and regulator mechanisms while they are welded together. The use of arbor presses to quickly and solidly secure jigs is a great idea. With the upper and lower halves of the jig mounted on the ram and secured to a plate fixture under the ram, the parts can be laid in place and the ram is lowered to hold them down for welding. That’s an idea that could find its way into your home shop during smaller fabrication projects.
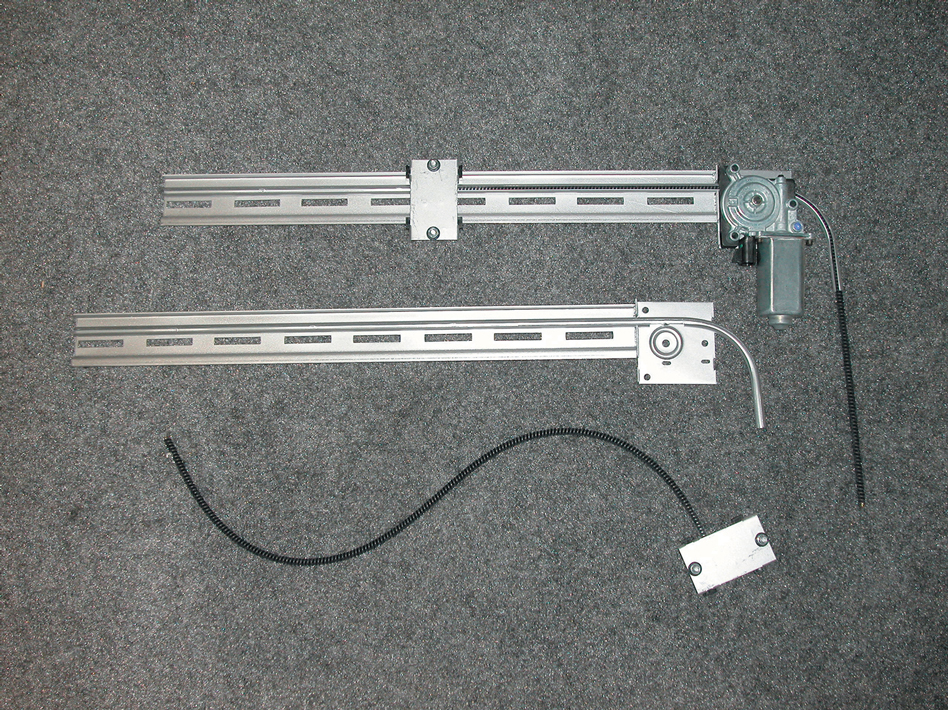
A couple of years ago Ervin passed away, and son Robby Whitehead took over, though Louise still comes into the office daily. The heart of their market has been street rods, and in recent years theyʼve seen the market beginning to edge into later model years. “In the beginning, we couldnʼt give away kits for ʼ55-ʼ57 Chevy cars,” Robby told us. “Everybody was restoring them, and if it wasnʼt factory, they didnʼt want it. Now the ʼ55-ʼ57 kits are one of our best sellers–we keep them on the shelf at all times.”
When designing a model-specific kit, SPW starts out with an original factory door and cuts a huge opening in the front of it for access to the back side of the doorʼs interior panel. New lift mechanisms, original-style regulators, tracks and glass channels can then be easily designed from inside the door. Itʼs a smart, efficient process, though Corvette restorers will flip out at the set of windowed first-generation doors we saw. Besides the universal and model-specific kits, SPW also supplies most of the aftermarket fiberglass body manufacturers, as well as special projects and limited-production vehicles such as the exotic Mosler MT900 sports car. Once the specs are determined, the metal components are stamped out, bent to shape and welded together, all in-house.
Several years ago, SPW began thinking about electric windshield wiper kits, as many of the principle components are similar in function. The intermittent wiper kits use commercial two-speed, self-parking electric wiper motors that drive the same kind of flex cable found in the companyʼs window kits. The cable engages gears on the back of the wiper transmissions and is completely enclosed in bendable steel tubing (like brake line). Because of this streamlined design, there isnʼt any worry about making room under the dash for moving arms or cables that normally connect the motor to the wiper arm transmissions. Itʼs also an extremely thin profile, so it fits well behind pre-war dashes. Perhaps most unique is that you can run any cable length, which allows you to put the motor almost anywhere in the interior if space is at a real premium. SPW offers cable in lengths up to 144 inches, so you could put the motor in the trunk of your coupe, running the cable through the roof or along the floor up to the windshield. We were as impressed with the slick design of SPWʼs wiper drives as we were with its window lifts. What we like most about them is the OE look, fit and feel of both kits, and how they install like a factory assembly instead of like an aftermarket afterthought. Hereʼs how they do it.
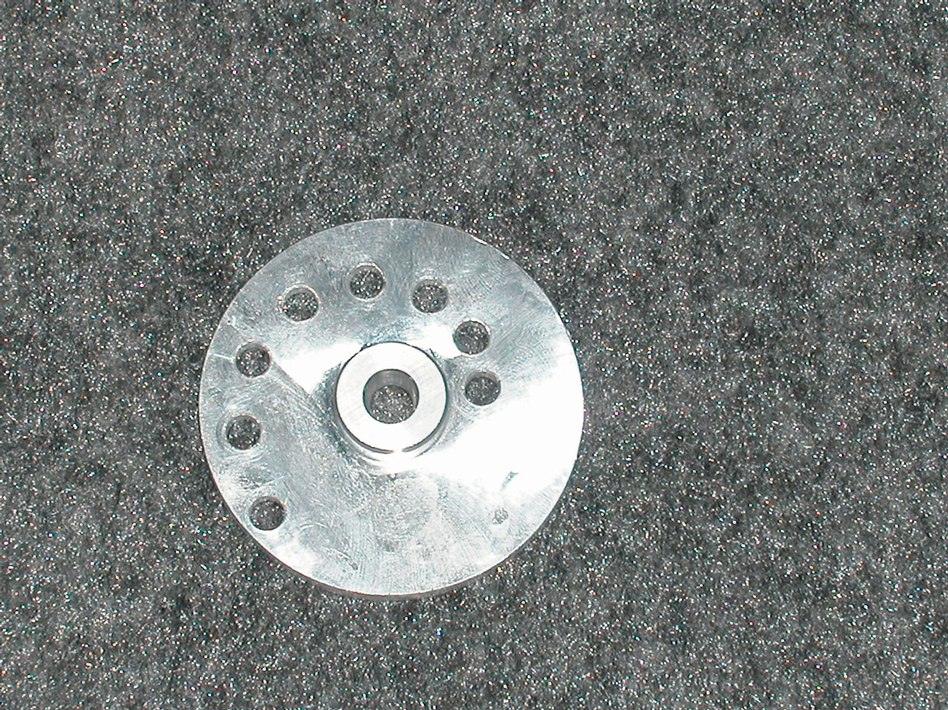

Article Sources
Specialty Power Windows
800/634-9801
140 Industrial Park Drive Forsyth , GA 31029