Thereʼs More to High-Performance Brakes Than Stopping the Car
In the eyes of the Chevy enthusiast, ultimate acceleration reigns supreme. Everything plays second fiddle in the performance-oriented minds of many enthusiasts, including handling, comfort and so on—besides, those things are tough to quantify. Acceleration and top speed are what we are into and unfortunately, all too often, last on the performance priority list is braking. Remember, no matter how quick or fast a particular Chevy is, and no matter how well that Bow Tie handles, no matter how plush it is, no matter how straight the body panels are or how crafty it’s built, eventually you have to get the thing to stop.
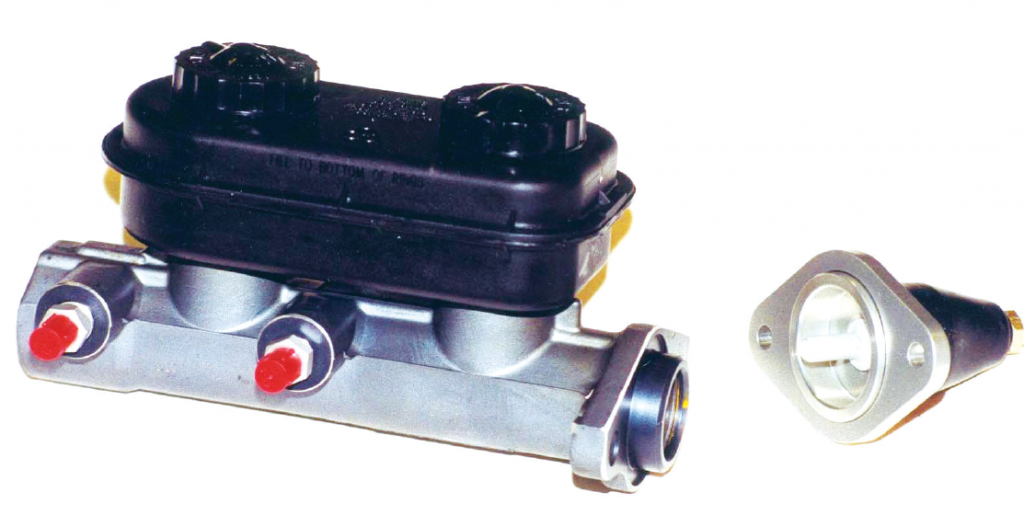
The wet boiling points are outlined as follows:
- DOT 3 = 284 degrees F
- DOT 4 = 311 degrees F
- DOT 5 = 356 degrees F
As you can see, the wet boiling point of silicone brake fluid is significantly higher than its glycol-based counterparts. That’s because unlike silicone fluid, glycol-based brake fluid does not absorb moisture. In addition to the decrease in brake efficiency, when the fluid is intermixed with moisture, a number of internal brake components can be attacked by water found in the system disc-brake pistons, which can corrode, causing a dangerous situation, and an expensive repair bill.
So why don’t the OEs make the switch to silicone-based brake fluids? While silicone brake fluids do not absorb moisture (and do not harm paint finishes if spilled), they do have some pitfalls. One problem is slight compressibility under high temperatures. If the brake system is exposed to very high temperatures, the silicone fluid can compress slightly, with the end result being a spongy pedal. In addition, silicone fluid is affected by atmospheric pressure. When a silicone-equipped vehicle is used in high-altitude conditions, the fluid can expand significantly, again contributing to a spongy pedal. Also, many of the rubber components used in brake systems are manufactured from ethylene propylene rubber (EPR), and many silicone fluids are not compatible with EPR, which causes them to expand.
Several brake system manufacturers offer their own specially blended fluids. An example is Wilwood’s 570 Racing Brake Fluid, which has a minimum 570-degree F dry boiling point. This fluid will withstand the severe heat requirements sometimes found in a racing brake system. Wilwood points out that part of the formulation for the 570 Racing Brake Fluid is its low viscosity, which allows easy bleeding of the brake system. It also eliminates aeration of the brake fluid caused by foaming, due to excessive pedal pumping.
So what’s the answer? Here’s some insight: Never mix brake fluid brands or types, and make every effort possible to keep contaminants out of the brake fluid. Once the protective seal is broken on a can of brake fluid, use it immediately. Purchase brake fluid in small cans. When the seal is broken in a larger container, moisture tends to collect, which can lower the fluid boiling point and make it unsuitable for high-performance applications. Reserve the use of silicone brake fluid for cars that are only driven periodically, such as collector cars or antiques. Finally, consider flushing out the old glycol fluid in your car’s braking system and replacing it with fresh racing brake fluid on a regular basis.
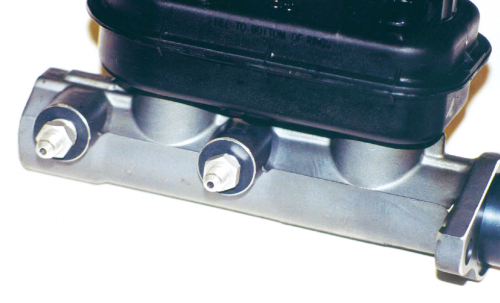
When it comes to stopping power, you have to bear in mind that the Chevrolet in question used up plenty of energy to produce those low-elapsed times, stunning 0-to-60 times and impressive top-end numbers. And that very same car needs to dissipate the same energy to bring it all to a grinding halt. There’s more to brakes than simply stopping the car—reliable brakes are essential. They must be capable of stopping the car repeatedly and they must accomplish this with no fuss and no additional input from the driver. There are plenty of components within the brake system, but the place it all begins is the brake pedal and master cylinder. Let’s look at this overall.
Selecting A Master Cylinder
There are many different master cylinders available in today’s marketplace, but for high-performance Chevy applications or any application with four-wheel brakes, you must use a dual (tandem) assembly. A dual-master cylinder separates the brakes, front to rear. When shopping for a dual-master cylinder, several features are critical, such as the piston bore dimensions and the location of the outlet ports. A good number of master cylinders, including those for countless late-models with power brakes and ABS, have the outlet ports on the “wrong” (engine) side. This makes plumbing difficult or even impossible in some situations. Also, some master cylinders are not well-suited to non-power-boosted vehicles like those regularly seen in modified cars.
Perhaps the slickest master cylinders we’ve seen for these applications are the Mopar-style aluminum-body master cylinders sold by Mark Williams Enterprises. They are perfect for most high-performance, firewall-mounted Bow Tie applications. The advantage is that two different bore sizes are readily available, 1 inch and 1-1/8 inches. A 1-1/32-inch bore cylinder is also available and is so very close in size to the 1-inch assembly that it is sometimes called just that. We’ll get into the need for different bore sizes later. These aluminum-bodied master cylinders have relatively large-capacity plastic reservoirs with dual-outlet bores that correctly face the driver’s-side fender (when mounted on the firewall). If there is a shortcoming with this Mopar-style master cylinder, it’s the size of the outlet fittings. The front fitting is a 9/16-20 inverted flare, while the rear is a 1/2-20 inverted flare. It can be difficult to find appropriate adapter fittings for these dimensions, but Lamb Components offers a solution. It manufactures number 3 AN male adapters specifically for these master cylinders. These fittings are inexpensive and real time-savers. They are also available as options on the Mark Williams master cylinders.
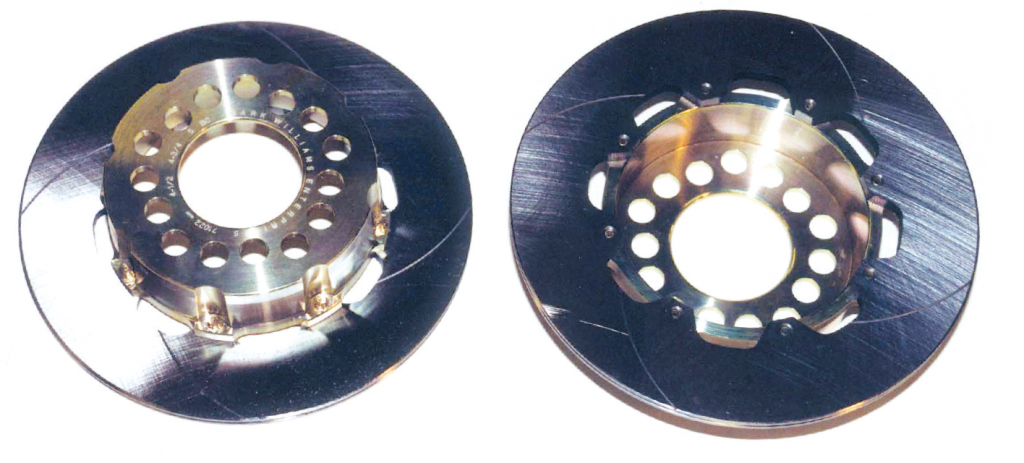
These master cylinders will require an adapter to fit the firewall mounting on most vehicles. The adapters are designed to convert an application, such as an F-body that originally came equipped with a power booster, to the manual Mopar pattern. Lamb Components offers several of these adapters for varied applications.
Pushing Pedals
Brake pedal ratio is critical, as the brake pedal acts as a lever to increase the leverage the driver can comfortably apply to the master cylinder. In turn, the master cylinder forces fluid (pressure) to the disc-brake caliper (pistons) or to the wheel cylinders (drum brakes). If you examine the layout of a brake pedal, you will notice the pedal arm pivot, along with the mounting point for the master-cylinder pushrod. The dimensions between pedals are rarely identical, and by varying the length of the pedal arm and/or the distance from the pushrod mount to the pivot, you can change how much force is required to energize the master cylinder. This is referred to as mechanical advantage or pedal ratio. This formula will help you figure out psi:
Input Force x Pedal Ratio
Brake Piston Area
Translated, this is the amount of force exerted by your leg times the pedal ratio, divided by the area of the brake piston(s). The typical adult male can exert approximately 300 pounds of force with one leg. If you’ve ever tried leg presses, 300 pounds is a bunch, and something around one-third or one-half that amount is more comfortable, even in a high-performance application.
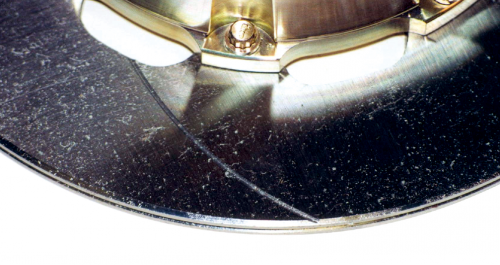
Some people think that if you pump the pedal to increase brake-holding power, it will increase brake-line pressure. In practice it doesn’t really change the pressure. If you must pump the pedal to increase the holding power of the brakes, something has pushed the pistons farther back in the caliper (runout in the rotor, a cocked caliper and bad mounts are some examples), or there could be air in the system. The bottom line is if you have to pump the brakes to hold a car or stop it, not only is something wrong, but pumping the brake pedal does not build pressure (although it may eliminate pedal travel). It just feels as if you are building pressure.
The average manual (non-power-boosted) master cylinder will require somewhere between 600 to 1,000 psi to be totally effective. Somehow, you have to translate the 100 to 150 pounds of leg force into 600 to 1,200 psi. The way this is accomplished is by pedal ratio. Changing the overall length of the pedal arm is generally not possible, so it’s easier and far more practical to shorten the distance between the pivot point and the master-cylinder pushrod mount location. That’s why vintage Chevrolets almost always had two master-cylinder pushrod positions on the brake pedal—one for cars with power brakes and another for cars with manual brakes.
Brake-line pressure is different than the force you apply to the pedal. Force acts in one direction and is addressed in pounds. Pressure acts in all directions and is addressed in psi (pounds per square inch). Levers can be used to change the force. Inside the hydraulic system, the surface area of the piston is what is affected by pressure. Decreasing the bore size of the master cylinder will increase the pressure it can build. Pistons in master cylinders are specified by bore size.
There is a catch, however. The area of a circle (or bore) is:
π x R2
The area of the piston surface increases or decreases as the square of half the bore size or diameter. The area of a 1-1/8-inch master cylinder is approximately 0.994 square inches. The area of a 1-inch-bore master cylinder is approximately 0.785 square inches. As a result, switching from the larger master cylinder to the smaller version will increase the line pressure approximately 26.5 percent, assuming that pedal ratio has not changed.
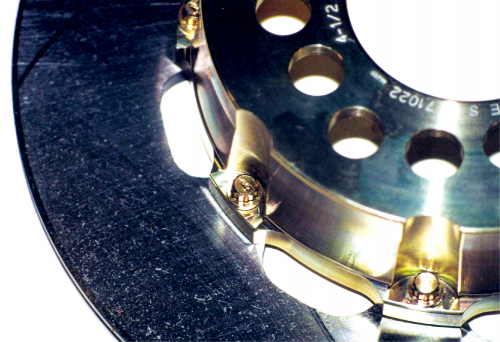
If a single-piston, front-design brake is used in conjunction with a pair of four-piston rear calipers, a 1-inch tandem master cylinder will work. In applications where four-piston brakes are used front and rear (definitely desirable in a high-performance Chevy), a 1-1/8-inch-bore tandem master cylinder will work.
Also the master cylinder must be solidly mounted. Often a spongy brake can be attributed to master cylinder deflection. Firewall-mounted master cylinders use more than the firewall sheetmetal as the master cylinder support; there is a structural integrity to these mounting areas. Do not cut away any of this reinforcement and be sure to look for any cracking in the area of the master cylinder, especially in a vintage Chevy with manual (non-boosted) brakes. The sheetmetal surrounding the master cylinder can eventually fatigue in these cars, even though they were never modified. Unmodified cars with power brake boosters seldom have evidence of firewall fatigue. Sharp chassis builders will make every effort to physically brace the master cylinder mounting area of the firewall where applicable.
It’s easy to see as you increase the pedal force, the pedal ratio or both that the stroke of the master cylinder is shortened (brake-line pressure is unaffected). When you increase the size of the master-cylinder piston, you decrease the output pressure of the master cylinder. A smaller master-cylinder piston will exert more line pressure with the same amount of force than a master-cylinder piston with a larger piston area. But there is another catch: since the brake-line fluid pressure is working against the surface of the wheel cylinder (or disc-brake piston), increasing the area of the cylinder will increase brake torque. That’s why some enthusiasts, when using drum brakes, replace wheel cylinders with larger models.
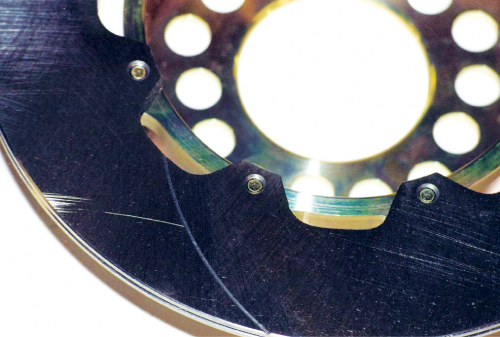
A good example of this is the early GM wheel cylinders, which typically measure 3/4-inch bore size. These units can be replaced with either 7/8-inch or 15/16-inch cylinders, like those on some domestic station wagons equipped with larger drum-brake wheel cylinders. By increasing the size of the wheel cylinder, the clamping power of the drum brakes will increase.
The bottom line is to find a wheel cylinder that works for your particular application. Playing with wheel cylinders (bore sizes) also has an effect upon the brake pedal feel. Just remember that when mixing and matching OEM parts, the balance must be done very carefully.
If you need to improve the stopping power of your car, or if you need to reduce the effort it takes to depress the pedal, there are several options: a) decrease the master cylinder bore size; b) increase the pedal ratio; c) increase the wheel cylinder bore size (on drum brakes). If you increase the pedal ratio, you’ll have more travel at the master-cylinder piston. If you decrease the master-cylinder bore size, the piston has to travel farther to move the same amount of fluid. Typically, a master cylinder has approximately 1-1/2-inch to 1-3/4-inch of stroke. The idea is to properly coordinate the pedal ratio with the bore size to arrive at approximately half of the stroke (roughly 1 inch), in order to make the brakes feel comfortable on application—and of course, bring the car to a halt.
Getting Your Proportion
Proportioning valves are used in a number of different applications. In street-driven vehicles, proportioning valves are used only on the rear brakes and never on the front brake system. Basically, the reason for using a proportioning valve is to provide the proper rate of pressure to the rear brakes. As you apply brake pedal force, the vehicle transfers weight from the rear of the car to the front. When the brakes are applied initially, the pressure to the brakes is more or less linear. As the weight transfer to the front increases with brake application, the rear of the car becomes lighter. At some point, the linear brake pressure must be changed so that the rear tires of the car do not lock up. Keep in mind this is in a street car application, which generally speaking, is a vehicle with identical or relatively close tire and wheel sizes front and rear. Many high-performance Chevys incorporate mismatched tire and wheel sizes, and because of the larger rear tire, it is possible to run a car without a proportioning valve. Even as weight is transferred to the front of the car, the ultimate size of the back tire will help eliminate brake lockup, due to its larger size and contact patch.
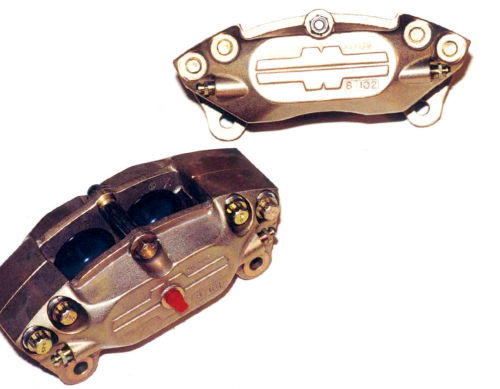
There are other factors other than tire size that can influence premature rear brake lockup, and some may surprise you. Here’s a bit of vintage Trans Am research done by Chevrolet: a 302ci engine with a closed throttle at high rpm can add something in the order of 200 pounds of brake force to the back tires. Weight distribution in the car will affect brake balance, as well as the surface you drive on. It all has an effect on brake lockup; even the aerodynamic forces play a role. So as you see, the variables with regard to brake balance are many.
Most aftermarket proportioning valves are adjustable, usually by way of a knob or lever. Typically constructed from billet aluminum, such a valve could have an adjustment range from 100 to 1,000 psi. This type of valve does the same thing as a standard proportioning valve; however, it provides you with the capability of fine-tuning the amount of pressure ultimately seen at the rear brakes. By adjusting the pressure, you can control the brake balance and eliminate brake lockup at the rear wheels.
Residual Pressure Valves
Residual pressure valves can—and in some cases must—be used with both disc/disc and disc/drum brake systems. The most common valves are 10psi versions and 2psi versions. In the case of 10psi valves, they are used in a system that incorporates drum brakes, disc/drum or drum/drum. The purpose of a residual pressure valve is to prevent air from entering the system when you release the brakes.
Here’s how that happens. In a typical drum-brake system, the wheel cylinder is usually equipped with what is commonly called a “chevron seal.” This device seals against the bore when pressure is built behind it. When the brake pedal is released quickly, a vacuum is created, which causes the chevron seal to pull away from the wall of the wheel cylinder. Since a vacuum was created, air can rush into the system, attempting to relieve the vacuum condition. The 10 pounds of residual pressure overcomes the vacuum effect and as a result, no air can enter the brake system.
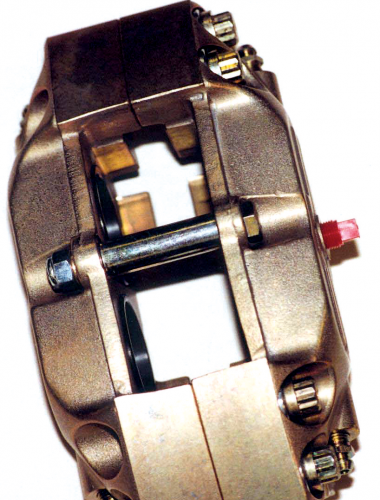
Some wheel cylinders (particularly late-model examples) are designed with a cup expander behind the seal. The purpose of this cup expander is to maintain the relationship between the seal and the wheel cylinder bore. Because of this, they do not require residual pressure valves. Aside from taking a wheel cylinder apart, there is no easy way to determine if a cup expander has been installed. It should also be pointed out that some master cylinders designed specifically for disc/drum brake systems already incorporate an internal 10psi residual pressure valve. But the key here is that only some have this feature. In some cases, jobber specifications for the component can spell out these particulars, but if the information is not available, it is possible to run an auxiliary residual pressure valve in conjunction with cup expanders. It won’t hurt to install one, as having two valves in the system doesn’t compound the effect. You don’t need to worry about brake drag caused by the residual pressure valve, as a common rear-drum arrangement typically takes between 50 and 75 psi to overcome the force of the return springs.
The 2psi residual pressure valve is used in disc/disc brake systems. But these valves are required only if the height of the master-cylinder fluid level is lower than the top of the brake-caliper piston. Your brake system most likely will not have this characteristic, as this is only common in modified cars such as race cars, street rods or any car with a floor-mount master cylinder. A residual pressure valve works in only one direction, so it must be installed properly. It stops the brake fluid from draining back to the master cylinder once the brakes are released. Characteristically, this problem will manifest itself in a pedal that requires pumping at least twice to gain proper pedal feel.
Brake Rotors
There are a number of different rotors in production today. In aftermarket applications, there are two or three different types that see regular use: solid steel and iron rotors, along with the newer, more exotic carbon rotors. Occasionally, you’ll find vented-steel rotors in certain applications. Which is best? That depends upon the car and the pocketbook.
As mentioned, solid rotors can be manufactured from steel or gray cast iron. Both have merits, but in the end, a rotor must have good wear and friction properties. It also must be rigid and have sufficient strength at high temperatures. Rotors are measured by the outside diameter and the total thickness across the pair of contact surfaces. Obviously, a vented rotor will be thicker and in most cases, far heavier than a solid rotor. In terms of diameter, the rotor is always limited by the size of the wheel. This is important, as traditional Bow Tie applications are constructed with 15-inch-diameter wheels. For larger-diameter rotors it will require at least a 17- or 18-inch-diameter wheel.
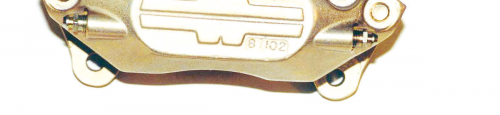
The size of the rotor is very important, as the swept area of the brake eventually determines the stopping capability. Swept area is the total area contacted by both the inner and outer pads as the rotor makes one complete revolution. It’s easy to see that if the rotor and pads are made larger, then the swept area increases. But don’t forget that wheel size will be the limiting factor.
In some cases, rotors may be cross-drilled or slotted in an attempt to improve performance. Cross-drilling a rotor serves the purpose of lightening it, and some builders believe it helps small pockets of gas trapped between the pad and rotor to escape. Others say drilling reduces the rotor’s life span and cooling capacity. Slotted rotors are most useful to racers, as the slots are designed to cut a new face in the pad with each rotation, removing any impurities or material buildup that can reduce braking ability. However, slotting does rapidly decrease pad life. On the street, most experts recommend drilled rotors over slotted ones.
Hats
In a production car, the brake rotor and hat are usually one-piece. Most aftermarket assemblies are two-piece. A one-piece steel rotor has a large amount of mass on one side and because of this, it will have a natural tendency to warp slightly. In turn, the pads wear on an angle, which effectively reduces contact area and can eventually cause brake problems. This is why in most high-performance applications the hat is almost always made as a separate component. The rotor is attached to the hat and is generally installed to either the wheel hub or the axle flange. The purpose of the hat isn’t only to provide a place to mount the rotor; it also provides a longer path for heat to travel from the brake swept-area surface to the wheel bearing. If this pathway is short, the wheel bearings will be affected.
Although hats can be produced from different materials, the most common aftermarket brake arrangement is aluminum. It’s perfect for the application since it’s very light and has the capability of dissipating heat very quickly. And not only does aluminum reduce weight, it reduces thermal stress on the rotor. Since aluminum expands at a rate greater than iron or steel, it tends to equalize the expansion difference created by the sometime extreme temperature of the rotor. On quality-engineered hats, the heat path is taken into consideration during its design, as this directs the heat away from the bearings, permitting the wheel to absorb the temperature. While there are two commonly used types of hat-to-rotor mounting design bolts and drive lugs, most street applications simply have bolt holes.
Brake Calipers
Caliper action is exactly like a hydraulic clamp. As brake fluid pressure is applied to this clamp, it bears down on the spinning rotor, eventually stopping the rotor from turning. Calipers can be two different designs, floating or fixed. Most stock disc brakes use the floating design, where the piston is located on one side of the caliper. As brake-fluid force is applied to the floating caliper, the piston is energized, pushing the pad against the rotor. Simultaneously, the entire caliper is drawn inward, energizing the curbside pad. In simple terms, the caliper moves inward (sliding on guide pins or installed on a flexible mount) each time the brakes are applied.
In contrast, most aftermarket brake systems rely upon a more robust fixed caliper. In this case, the caliper has a pair of pistons—or four or even six pistons—equally arranged from side to side. As fluid pressure is applied, the pistons equally receive pressure and the caliper clamps the rotor. In terms of optimum performance, a fixed caliper is considered the better design. A fixed caliper tends to wear the pads more evenly, as opposed to a floating caliper, which can wear pads at an angle. A fixed caliper does incorporate one or more extra seals than a floating caliper, making it more likely to leak. However, a fixed caliper will take more hard stops before it overheats.
Caliper rigidity, and consequently caliper flex, are both extremely important. If the body of the caliper flexes, then the feel in the pedal will be softer. A fixed caliper is more rigid than a floating configuration. What happens is the caliper is cocking the pistons, which leads to braking inconsistency and tapered pad wear. According to Williams, “The most important characteristic for a caliper’s stopping ability is the bridge strength. The limiting strength factor for [fixed] calipers is the fastener strength. All of the attention over material types, such as forged or billet, has little effect on the bridge strength. We use four 7/16-inch-diameter fasteners, plus a support bushing to eliminate caliper flex.”
Remember the previous caliper description because there’s more. In order to visualize this bridge strength scenario, think of a good, old-fashioned C-clamp tightened over a piece of 1/2-inch-thick steel plate. Once the C-clamp is tightened completely, turn the handle farther. The steel plate doesn’t move and neither do the jaws of the clamp. But the clamp handle turns. Watch the frame section of the C-clamp carefully—it’s moving. Even though there is no more clamping power being exerted on the plate, you can still tighten the clamp. What you’re actually doing is stretching the jaws of the C-frame on the clamp. That same phenomenon affects brake calipers. Remember, the forces are magnified.
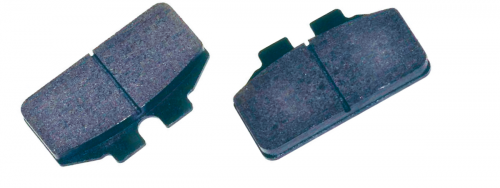
Compounding the problem is the material used in brake calipers. While iron calipers are strong, easy to cast in large volumes, easy to machine and relatively inexpensive to produce, they are also extremely heavy. That is why racing and high-performance calipers are almost exclusively manufactured from aluminum. Several different types of procedures are used to form caliper bodies: forgings, machined billets and castings. Each system has its own merits, but as we’ve pointed out, the real trick with aluminum calipers is to manufacture them with sufficient bridge strength to minimize caliper flex.
When choosing calipers, remember that the front brakes perform some 70 percent of total braking duties, so your front calipers should be more capable than the rears. Although many cars feature the same number of pistons in the front and rear calipers, many have more pistons in front than in back, and none have more in back than in front. What’s really important isn’t necessarily the number of pistons, but their total area. With that said, a four-piston caliper will typically be more powerful than a two-piston caliper and so on. Typical arrangements include two-piston front/one-piston rear calipers in mild-performance applications and four/two or even six/four if you really want to get serious. The bottom line when deciding upon caliper arrangements for your application is to follow the recommendation of the brake manufacturer.
Brake Pads
Much has been written about brake pad or lining material. Friction material in a brake is normally mounted on a brake pad backing plate, usually constructed from steel. The friction material is physically bonded to the pad, which in turn rests upon the caliper pistons. In some OEM examples, an anti-squeak shim is positioned between the pad and the piston. And in high-heat applications, an insulator is placed between the pad and the piston in an effort to reduce the temperature in the brake fluid and piston seal.
Different manufacturers have different theories, but remember that all pads start out cold and end up hot. This places special demands upon the high-heat pads because they require a longer warm-up to get up to operating temperature. What’s needed is a pad with a very high coefficient of friction, and the pad has to work with the rotor material selected (iron or steel). In certain cases, such as race pads, temperatures can get ridiculously high, so obviously the pad material must be able to withstand these temperatures. This has little to do with a normally driven street Chevy, other than to alert you to the fact that pads that will work at high temperatures will not be as effective when they are cold. Pads that are more of a compromise will tend to fade or exhibit high pedal effort when brake temperatures reach the extreme, especially over extended periods of time.
Some brake pads require breaking in before use, but not all. This conditions the pads and rotor surfaces. This bedding-in procedure will result in greater performance, longer wear, more effective swept area and less likelihood of rotor cracking due to thermal shock. Follow the aftermarket manufacturer’s recommendations for the type of pads you are using. In the end, the choice of pad compounds depends upon the car, the brake system and of course, how the car will actually be used.
Brake Fluid
Brake fluids are not all created equal. Over the past several years, many changes have affected brake fluid, not the least of which is silicone-based fluid. Unfortunately, the fluid situation isn’t as simple as swapping one type of fluid for another. The Department of Transportation (DOT) has for some time issued a set of specifications for brake fluid types. The more common glycol-based or conventional fluids fall under DOT 3 and DOT 4 specifications. DOT 3 has a minimum dry boiling point of 401 degrees F, while DOT 4 has a minimum dry boiling point of 446 degrees F. On the other hand, silicone fluids fall under DOT 5, which has a dry boiling point of 500 degrees F (minimum). In a typical road car, the conventional fluid boiling point diminishes with time. Technically speaking, vehicles that are operated under damp conditions will notice a rapid deterioration of the brake fluid boiling point in as little as six months.
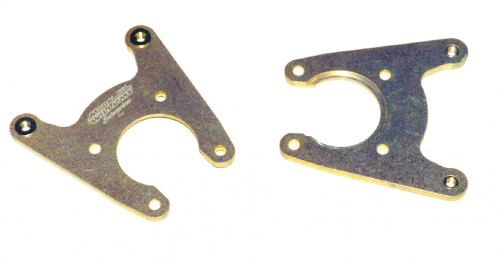
So what’s the big deal in regard to brake fluid boiling points? In reality, one of the most critical factors in regard to a hydraulic brake system is the dry and wet boiling point. If the fluid boils, small gas bubbles occur. These bubbles don’t disappear, but are trapped in the system. Since gas bubbles are compressible, the brake pedal becomes spongy. Generally speaking, a modified car can be plagued by wet boiling points. Normally, the brake system will function with a percentage of moisture in the system. Over time, this moisture content increases and as a result, brake performance decreases. That’s why wet boiling point specifications are also provided by DOT. The wet boiling points are outlined as follows:
- DOT 3 = 284 degrees F
- DOT 4 = 311 degrees F
- DOT 5 = 356 degrees F
As you can see, the wet boiling point of silicone brake fluid is significantly higher than its glycol-based counterparts. That’s because unlike silicone fluid, glycol-based brake fluid does not absorb moisture. In addition to the decrease in brake efficiency, when the fluid is intermixed with moisture, a number of internal brake components can be attacked by water found in the system disc-brake pistons, which can corrode, causing a dangerous situation, and an expensive repair bill.
So why don’t the OEs make the switch to silicone-based brake fluids? While silicone brake fluids do not absorb moisture (and do not harm paint finishes if spilled), they do have some pitfalls. One problem is slight compressibility under high temperatures. If the brake system is exposed to very high temperatures, the silicone fluid can compress slightly, with the end result being a spongy pedal. In addition, silicone fluid is affected by atmospheric pressure. When a silicone-equipped vehicle is used in high-altitude conditions, the fluid can expand significantly, again contributing to a spongy pedal. Also, many of the rubber components used in brake systems are manufactured from ethylene propylene rubber (EPR), and many silicone fluids are not compatible with EPR, which causes them to expand.
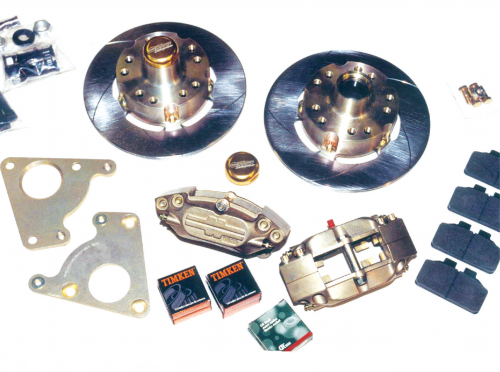
Several brake system manufacturers offer their own specially blended fluids. An example is Wilwood’s 570 Racing Brake Fluid, which has a minimum 570-degree F dry boiling point. This fluid will withstand the severe heat requirements sometimes found in a racing brake system. Wilwood points out that part of the formulation for the 570 Racing Brake Fluid is its low viscosity, which allows easy bleeding of the brake system. It also eliminates aeration of the brake fluid caused by foaming, due to excessive pedal pumping.
So what’s the answer? Here’s some insight: Never mix brake fluid brands or types, and make every effort possible to keep contaminants out of the brake fluid. Once the protective seal is broken on a can of brake fluid, use it immediately. Purchase brake fluid in small cans. When the seal is broken in a larger container, moisture tends to collect, which can lower the fluid boiling point and make it unsuitable for high-performance applications. Reserve the use of silicone brake fluid for cars that are only driven periodically, such as collector cars or antiques. Finally, consider flushing out the old glycol fluid in your car’s braking system and replacing it with fresh racing brake fluid on a regular basis.