The Ultimate Low-Buck Buildup
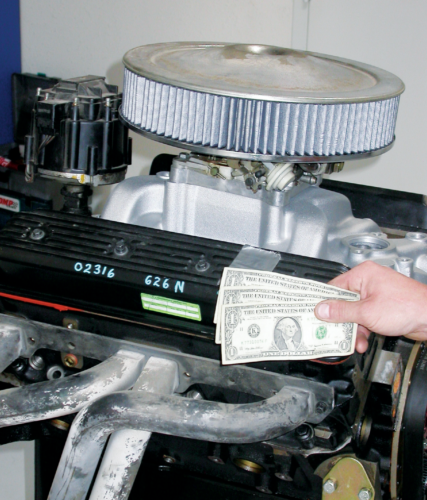
The premise was simple enough: take one popular small-block Chevy and select the most cost-effective components to achieve a two-fold goal of power and economy. In our case, we decided to attempt to produce an economical, honest 400 hp.
Building a 350ci small block to produce 400 hp is really no big deal, but doing it on what might be considered an extreme budget can be quite another story. For our needs, we decided to combine the goal of 400 hp with a spending limit of $1,000. Given the fact that a grand is less than the cost of a set of small-block aluminum cylinder heads today, reaching 400 hp looks pretty impressive, not to mention somewhat difficult. To make things even more impressive—or difficult, depending on one’s perspective—we decided that our $1,000 spending cap would include the cost of the motor. That’s right, we were attempting to build a 400hp small-block Chevy for a total of $1,000, including the cost of the motor!
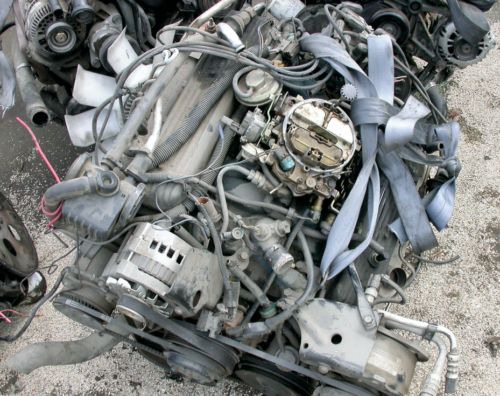
Since we were not starting the buildup with a running motor, the first order of business was to obtain a suitable candidate. Given our spending limit, a new or even rebuilt motor was out of the question. This left but one avenue open for locating our base motor: the local auto dismantler. Before rushing off with tools in hand, we let our fingers do the walking through the local “Recycler” paper. Basically a swap meet on paper, “Recycler” listed a number of complete engines for sale. We located several 350 Chevy engines available complete from air cleaner to oil pan (including accessories) for a paltry $450. The engines were also guaranteed to be in “good running order” (whatever that means).
While $450 for a running 350 Chevy is a good deal, the purchase would mean burning through nearly half of our total budget. After a few calls on what looked liked good deals on used motors, we finally came to grips with the reality that this project called for a trip to the wrecking yard. Calling first, we found a few yards that offered complete motors for just $225 (plus a core of $40). Of course, the motors for $225 were still installed in the vehicle, so this meant trading elbow grease for the additional cost savings. Always up for a quickie R&R, we ventured off to our favorite Pick-a-Part, in search of a true low-buck, yet hopefully well-running engine.
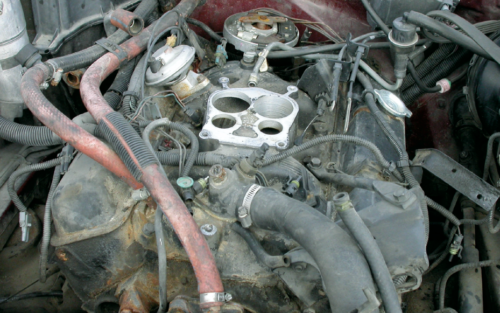
The $225 price tag was certainly attractive, despite the time and the labor required to remove the motor and to lug it home. Ben Franklin reminded us in Poor Richard’s Almanac that “The honey is sweet, but the bee has a sting.” In this case, the honey was the low $225 price tag, but the sting was the potential to remove what could best be described as a useless pile of junk. For our needs, even if the motor removed turned out to be a rebuildable core, we were hosed. We could always use it at a later date on another buildup, but the success of this project relied on finding a running small block in good working condition.
Believe us, running motors are out there for the taking. Given the sheer production numbers, this is especially true of small-block Chevys, though we made every effort to avoid the 305 small blocks and instead concentrated on finding a 350. The added displacement and bore size would help us achieve our goal on the limited budget available for performance parts. Available in both cars and trucks, our only concern was to locate a good-running motor with a four-barrel Q-jet. Though we would be replacing the cast-iron four-barrel intake manifold, the Q-jet was mandatory to help us achieve the desired power and keep us within budget. New four-barrel carbs are expensive, and besides, a good-running Q-jet offers a unique combination of performance and driveability.
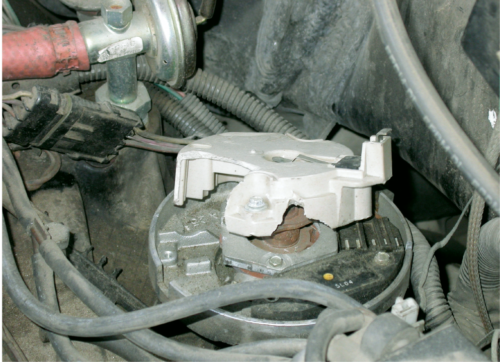
Here are a couple of tips that may help you separate a usable small block from the rest of the junk. First off, make sure that the motor in question has everything present that you will need to install in your vehicle. In most cases, the cost includes everything from the air cleaner assembly down to the oil pan, and from the fan to flexplate. We even managed to snag the motor mounts, starter and all of the accessories, though we would not include several of them once installed into the awaiting ’72 Camaro. Make sure to check for little things that often get robbed off junkyard motors, like the distributor hold-downs, accessory mounting bolts and carburetor linkage. Heck, we even attached the kick-down linkage from the trans to the carb, which went unnoticed by the junkyard cashier.
While you are checking to make sure everything is present and accounted for, make sure the things that are present are in good working order—or at least not cracked. Check things like the distributor, exhaust manifolds and oil pan. Major leaks are often a sign of abuse or poor maintenance, neither of which are desirable. Of course, a clean motor can also mean that it was cleaned to make it look more desirable, as opposed to actually being more desirable.
After checking out the major components, it is time to look specifically at the motor to ascertain its health and viability for the project. Check the coolant, oil and spark plugs. The oil and coolant have likely been drained, but check inside the radiator cap or even in one of the radiator hoses for signs of antifreeze. Fresh antifreeze is a good sign; a rusty radiator or thermostat housing is not. If the oil has been drained, smell the dipstick (does it smell like burnt oil?) and even go to the trouble of removing the drain plug on the oil pan. Does the residual oil resemble sludge or is it clean? Don’t confuse high mileage for abuse, as dark oil can mean that the motor simply needed an oil change and not a bearing change.
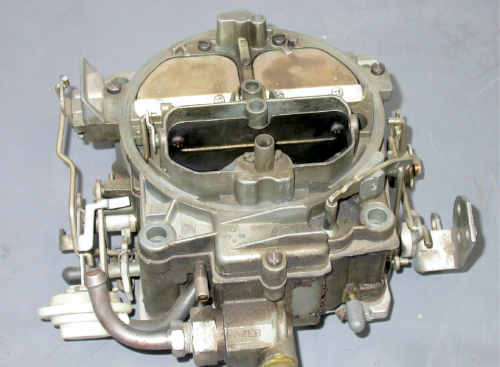
Don’t be afraid to yank a valve cover to verify the condition of the engine, as going to all the trouble of pulling a motor only to find out that it’s a junker is a huge waste of time and energy. Check the spark plugs for signs that the engine was burning oil. Avoid engines with oil-contaminated plugs, but don’t assume fresh plugs are the ultimate sign of a well-preserved motor. If the oil and plugs pass inspection, try spinning the motor over with a racket on the crank pulley. If it spins freely with no binding, chances are the bearings are in good shape. If you are allowed to bring a battery in to crank the motor over, by all means perform a compression check.
We performed all these procedures (with the exception of the compression check) on our motor and wound up pulling a four-barrel 350 from a ’77 Caprice. We chose the four-barrel motor over the many two-barrel versions because of the additional power potential. The cast-iron four-barrel intake manifold was going to get upgraded, but we planned on retaining the Q-jet to keep our costs in line.
The same held true for the cast-iron exhaust manifolds. The restrictive manifolds were given the old heave-ho to make room for a set of inexpensive tubing headers. For our 400hp application, we were not concerned with finding a four-bolt main 350 block. The two-bolt blocks are much more prevalent, and more than stout enough for our 6,000rpm (hydraulic flat-tappet) small block. Having run 540 hp and 7,000 rpm on a two-bolt block, we were not concerned about using one on this mild 400hp application. All we needed was the Q-Jet and a sound short block, as we planned on replacing the stock cylinder heads as well.
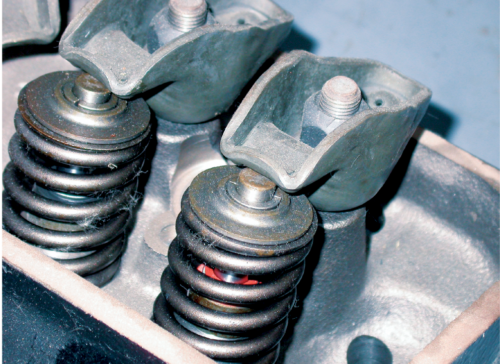
Care was taken to retain every nut and bolt while removing the motor from the car. This included the tranny and torque converter bolts, motor mount bolts and all of the vacuum and PCV lines. It’s not a bad idea to shoot a few pictures during the removal to remind you where all the hoses and fittings go, should you decide to retain these items on your vehicle.
During our search for what would become our low-buck buildup, we took what could be described as a few wrecking yard liberties. The $225 charge for the engine included a complete motor, but nowhere did it say that every component must have come from that particular engine bay. After some scrounging, we located a few items that would save us a few precious pennies, namely a set of used headers and an open-element air cleaner. Since this was indeed a low-budget operation, we took the time to remove the headers from the ’79 Camaro (they would fit our ’72 model as well) and the open-element air cleaner from an early-’80s half-ton truck. We simply replaced the cast-iron exhaust manifolds and stock air cleaner with the new components and we were in business.
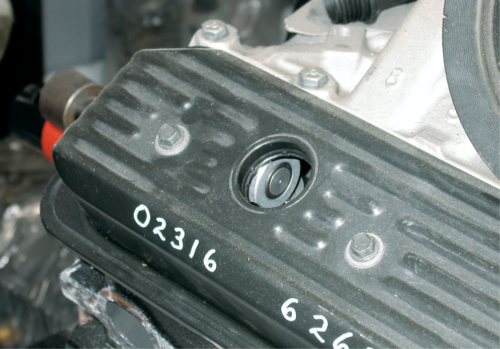
We also took the liberty of replacing our stock, stamped-steel rockers and valve covers with a set of guided rockers and center-bolt covers (including hardware) from a late-model truck. We knew the Vortec heads we planned on running required these components, so rather than purchase them, we simply swapped our parts for those required. This type of planning really helped eliminate some of the extra costs associated with building this motor. We made sure to leave the unused components in plain sight in the engine bay, should another customer require these items.
Once removed, we purchased the motor and transported it to the shop for immediate testing. The wrecking yard actually offered us a warranty (for an extra $12), which allowed us to return the motor for a replacement if it was internally damaged and unusable. As it turned out, the warranty money would have been wasted since our motor turned out to be a healthy one. A compression check revealed that every cylinder had 150 to 155 pounds of cranking compression. If offered, the warranty is still cheap insurance. Sure, you’d have to pull another motor, but you wouldn’t be out the $225 if you found a spun bearing or some other malady that could keep you from using the motor immediately.
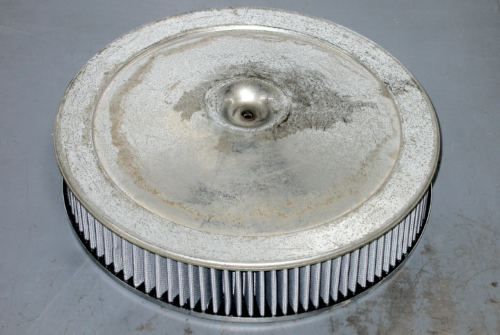
After the compression testing, we leaked down the cylinders. The leak-down test revealed that our motor was indeed healthy, with all the cylinders registering less than 8 percent. The final test was to check oil pressure. A new oil pump was not on the budget and we were hoping to get by with the stock pump, leaving more money for performance parts. After filling the pan with 10W-40 and spinning the oil-pump driveshaft with an electric drill, we were rewarded with nearly 60 psi of cold oil pressure. Naturally, this pressure would drop once it warmed up, but this seemed to verify that our small block was ready to rock.
With a complete 350 Chevy now at our disposal, it was time to start picking the performance parts. Our ’77 350 was originally rated at just 170 hp, hardly what you’d consider a powerhouse. To reach our goal of 400 hp, we needed to address the fundamental restrictions to power production. Our low-compression smog motor was obviously not the ideal choice for a performance buildup, but every motor will respond to the right performance components.
First on the list was a set of cylinder heads. Initially, we wanted to simply upgrade the existing heads with hand porting, milling and a valve job, but we soon changed our minds after adding up the cost of all the proposed modifications to the stock heads. The porting was essentially free, as the author planned on taking the cartridge rolls to the stock ports, but the machine work was pretty pricey, especially in comparison to the initial cost of the motor. We decided to purchase a set of new Vortec heads from GM Performance Parts. They wound up being a tad more expensive than reworking the stock heads, but the additional improvements offered by the Vortec heads more than offset the additional cost.
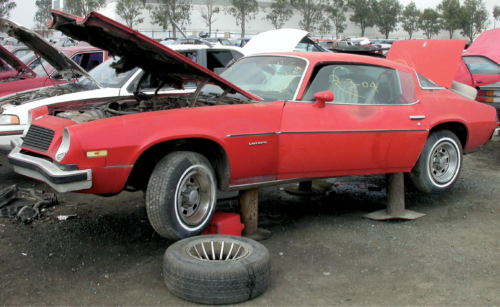
The benefits offered by the new Vortec heads included greatly improved flow without resorting to porting, all-new associated components (including valve job), and a smaller 64cc combustion chamber (without resorting to milling the already weak stock castings). Compared to a traditional smog-era, stock, iron cylinder head, the Vortec head offered an intake flow improvement of 35 to 40 cfm (at 0.500 lift). Oddly enough, Chevy did not dramatically improve the exhaust flow of the Vortec head compared to a more pedestrian iron head (like an 882 casting), but we took this into account by ordering a dual-pattern cam profile.
In addition to the airflow gains, the Vortec head upgrade also promised a performance valve job, something we would have to perform on the used stock heads. The Vortec heads also came with new intake and exhaust valves, seals and retainers, though it was necessary to upgrade the valve springs to accept our cam choice. The Vortec heads further improved performance with a smaller, more efficient combustion chamber (64cc) that increased the static compression ratio of our stock motor by nearly 1 full point, and it improved mixture motion (and fuel atomization) with the revised chamber design. The combination of increased airflow, all new components and increased efficiency and compression made the Vortec head hard to pass up, especially at a down-and-dirty price of just $500. We’d have spent nearly that much improving the prone-to-cracking stock heads and still had to cope with the less efficient and significantly larger (72cc) combustion chambers.
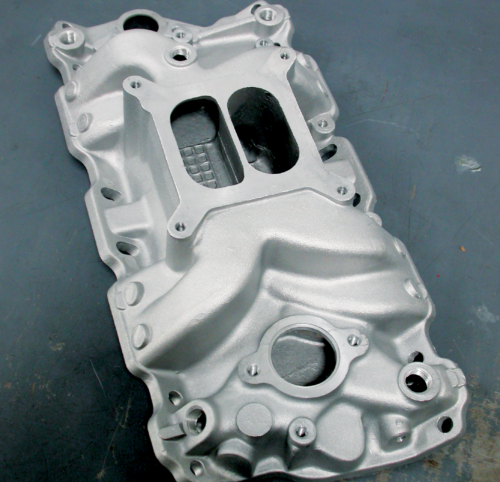
The Vortec heads were not without their problems, however; the first of which was a lack of adequate retainer-to-seal clearance. It seems that the Vortec heads as supplied by GM will only allow maximum cam lifts of 0.450 to 0.475-inch, depending on whom you listen to. Since we intended on running a cam with 0.480-inch lift, this put us in harm’s way in terms of adequate retainer-to-seal clearance.
Problem number two was that the stock springs supplied with the Vortec heads were production-oriented, meaning they offered just 75 pounds of seat pressure. While adequate for a low-rpm truck motor, the springs were nowhere near sufficient for our performance needs. The cure was to have the valve guides machined down to increase the retainer-to-seal clearance. In addition to trimming the height, we also took the liberty of decreasing the diameter (0.560-inch) of the guides. This was done to facilitate the use of aftermarket (0.530-inch) valve guide seals. We were fortunate enough to trade our stock smog heads for the machining operation performed to the valve guides. The cost associated with trimming the guides was $75, so figure on adding that to the cost of the buildup, if you are not quite as lucky with your horse-trading. Trimming the guides allowed us to add the necessary springs and retainers (Crane 10309-1 or equivalent) to facilitate the use of our performance cam profile.
The one downside to running the Vortec cylinder heads was that late-model heads required the use of a dedicated intake manifold. The bolt pattern on the Vortec heads differed from the traditional small block. Due to the popularity of this head casting, many aftermarket manufacturers have seen fit to cast intakes with the proper bolt pattern. Both GM and Edelbrock offer dual-plane intakes for the Vortec heads, but we found a more cost-effective version. Sure, you could try to source one on eBay or at a swap meet, but unlike the traditional intake pattern, the specialized Vortec intakes are a little tougher to locate used.
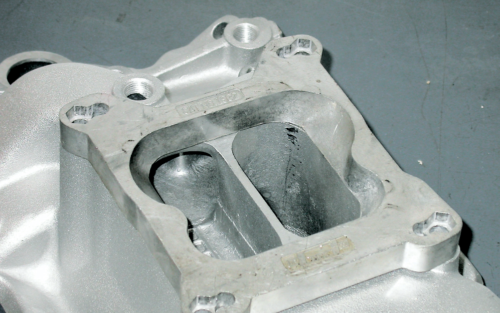
We found an aluminum, dual-plane high-rise intake from Motorville Wholesale. The dual-plane intake promised a broad powerband, something especially beneficial on a street application. The high-rise design also promised plenty of horsepower all the way to 6,000 rpm (or slightly beyond). The stock, cast-iron Q-Jet intake is an excellent choice for low-rpm performance, but if you are looking to produce 400 hp, the stock intake will definitely limit maximum performance. The dual-plane, high-rise aluminum intake was set up to accept a square-bore carb, so we purchased a spread-bore-to-square-bore adapter to run our Q-Jet.
The heads and intake ensured plenty of airflow, but our performance tin man was still missing a heart. Obviously the stock cam was not going to allow our motor make anywhere near 400 hp, despite the improvements to the induction system. With just over 9.0:1 compression (courtesy of the reduced chamber size in the Vortec heads), it was going to take something a bit wilder than the stock cam timing to take the 350 to the 400hp level. As mentioned earlier, the intake-to-exhaust flow relationship of the Vortec heads all but dictated the use of a dual-pattern cam.
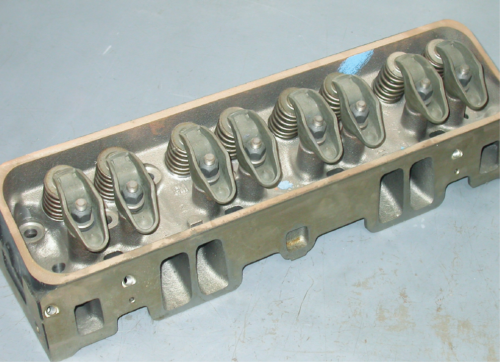
With cost still a major issue, we let our fingers do the walking through the pages of the Summit Racing catalog. What we were looking for was a cam profile that mirrored one of our favorite street small-block grinds from the Comp Cams catalog. If you can afford a few extra bucks, we’d say go with the Xtreme Energy XE268H, but with our tight budget, we were looking for savings. The XE268H cam offers a 0.477/0.480-inch lift split, a 224/230-duration split, and a 110-degree lobe separation angle. The closest cam we could find to these specs was Summit Racing PN SUM-K1105, which offered a 0.465/0.488-inch lift split and 224/234-duration split. The Summit cam included lifters for the paltry sum of $79.95. Given the poor 63-percent intake-to-exhaust-flow relationship, we suspected that the 10-degree duration split offered by the Summit cam might actually work out better than the 6-degree split offered by the Comp cam.
After the compression and oil pressure tests, the wrecking yard wonder was disassembled down to the bare short block. We installed the new Summit Racing hydraulic flat-tappet cam using plenty of cam lube. Since we had no way of knowing the mileage on the used motor, we decided that it was a good idea to spend a few bucks on a double-roller timing chain. At less than $20, the new timing chain ensured that our cam timing was unaltered by chain stretch. We coated and installed the new lifters included with the cam, and then installed the newly machined Vortec cylinder heads. We purchased a complete gasket set from Motorville for $24.95, which included a pair of new head gaskets. The performance set was $89, but our budget kept us with the cheap stuff. The heads were installed using the stock head bolts.
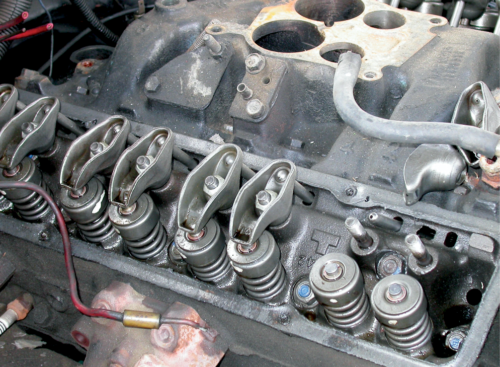
Next came the guided rockers and centerbolt valve covers. We then installed the new dual-plane intake from Motorville, followed by our carb adapter and Q-Jet four-barrel carb. The stock distributor was reused, along with the plug wires and spark plugs (ours were in perfect shape after a quick cleaning). The final step was to bolt on the 1-5/8-inch long-tube headers pirated from the Camaro in the wrecking yard, and our Low-Buck Chuck 350 was ready for some dyno action.
Though the rings and bearing had long since been acquainted, the same could not be said for the new cam and lifters. To properly break in the new cam, the motor was run at 2,200 rpm to ensure adequate oiling during the break-in period. The oil pressure looked steady at 55 psi and the motor sounded plenty healthy breathing through the 3-inch dyno exhaust. The initial pulls showed plenty of promise, with our low-buck engine pumping out more than 400 lb-ft of torque at just over 3,000 rpm. We experimented with timing (eventually settling on 34 degrees) and minor jetting to the Q-Jet before letting the hammer fly. With a safe air/fuel mixture in the high 12s, the 350 eventually pumped out 401 hp at 5,800 rpm and 426 lb-ft of torque at 4,200 rpm. We had officially reached our goal of producing 400 hp!
The final bill for our 400hp buildup checked in at $1,080, including the cost of the motor. We were excited about the 400hp peak number, but what really made us happy was the fact that this low-buck motor produced over 400 lb-ft of torque from 3,200 rpm to 5,000 rpm. Even down low at 2,600 rpm, our low-buck wonder churned out 380 lb-ft of torque. Destined for a daily driven ’72 Camaro, this 9:1 motor should make for an exciting commuter.
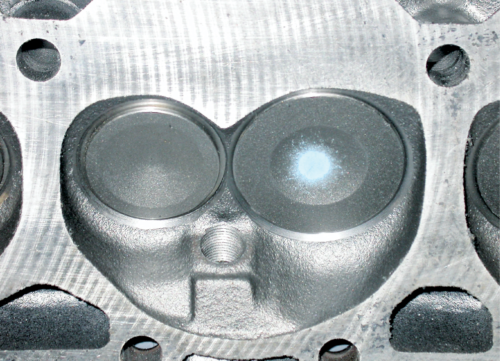
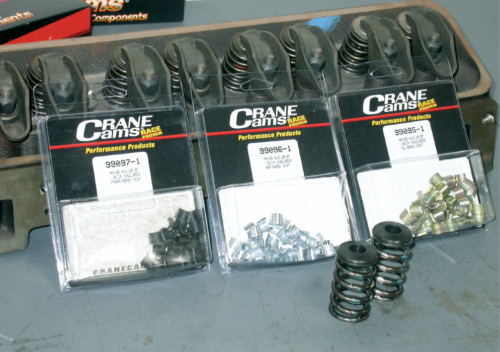
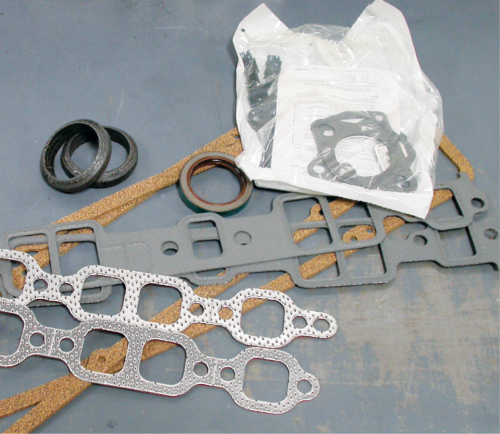
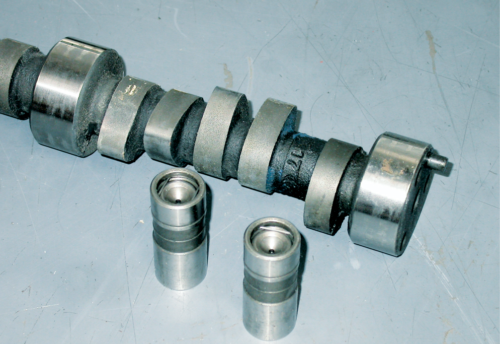
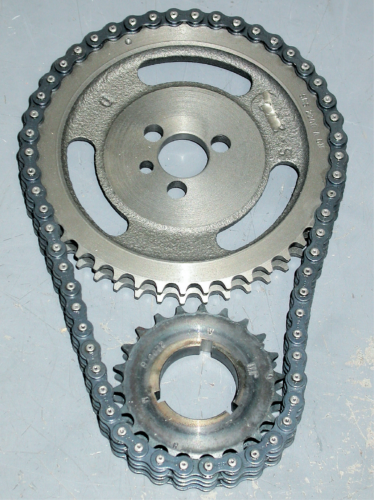
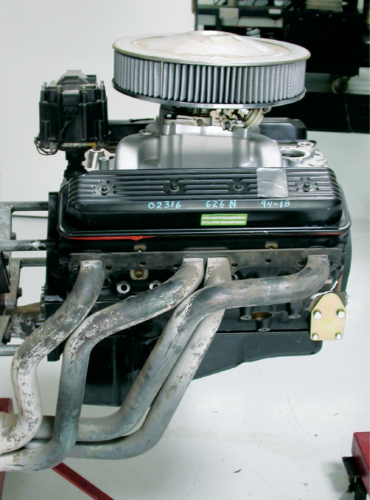