How to Keep Your Engine Ship Shape
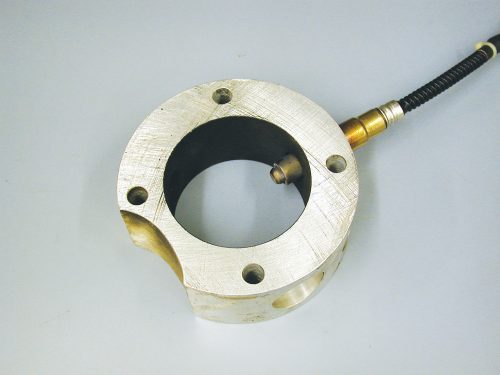
There’s no escaping the fact that gasoline prices are out of sight. This has many boat owners wondering how to tune their engines so they can get more hours out of a tank of fuel, while at the same time improving overall efficiency. A properly tuned fuel and ignition system will allow your marine engine to perform at its potential, and will be more enjoyable to use because it’s efficient and reliable.
Proper tuning can make the difference between a engine that runs great and one that always sounds as if it needs a tune-up. For most marine tuners, one of the biggest mysteries is how to “jet” the engine in order to obtain the correct air/fuel ratio necessary for high-speed performance or for just cruising or idling through a no-wake zone.
Ignition Timing and The Advance Curve
Air/fuel mixture is important, and we promise to cover that in a minute, but checking the ignition timing and advance curve really is the first step in engine tuning, since an incorrectly timed ignition may give you a false air/fuel ratio reading. Regardless of what
ignition system you use, if the spark timing is not correct, the engine will not produce all its potential power.
Any distributor, be it original equipment or a performance replacement, must have the mechanical advance curve checked and then tailored to both the engine and the fuel. One of the best references for initial timing for a high-performance engine comes from Barry Grant, Inc. At its website, www.barrygrant.com, you can find out about the correct timing for your engine by clicking on the “Demon selection guide” section. If it helps, use a 0.050 valve lift camshaft duration as a guide.
The advance curve used most on a mild-cam 9:1-compression Chevrolet V-8 engine is 12 degrees initial timing, plus another 24 degrees of mechanical advance by 3,600 rpm. An engine equipped with a hot cam or an air-gap/race-designed intake manifold may respond well to 18 degrees of initial timing, combined with a shorter mechanical advance curve of 18 degrees at 3,200 to 3,400 rpm. If the engine does not have enough ignition spark timing advance it may lack power, have poor throttle response, use too much fuel and cause the engine to run hot. If the engine has too much ignition spark advance, the engine may lack power, may ping, use too much fuel or run hot. The correct ignition timing will create maximum cylinder pressure at about 12 degrees after the piston goes past top dead center (TDC); only then can you get all the energy out of the fuel, creating maximum power and efficiency. Once the correct ignition advance curve has been confirmed, any problems at that point can be traced to an incorrect air/fuel
mixture.
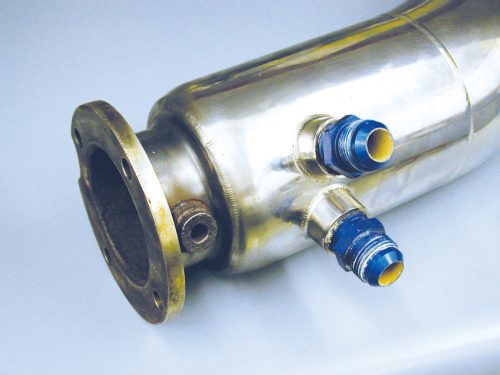
The fuel you use (reformulated pump or race) is an important part of an engine’s operation. Many things can affect how the fuel interacts with the engine, including air density (i.e., altitude, barometric pressure, air temperature, humidity), compression ratio, camshaft, exhaust system, ignition timing curve, engine condition, fuel pressure, airflow through the flame arrestor and more. With all these factors coming into play, one of the most important areas to focus on, therefore, is the correct air/fuel mixture for
your engine.
Properly tuning a boat engine carburetor or programmable fuel injection by “reading” the spark plug is an art that only a handful of people can do properly. Top tuners can look at the spark plug, the exhaust port and the first 6 inches of the header for proper “color,” and then make an educated guess as to what jet size change is needed. One of the disadvantages of this method is that the header and spark plug only can indicate what the mixture is at the exact rpm and load condition the plug was checked, so tuning is mainly by trial and error.
It’s important to get the air/fuel mixture correct. If the air/fuel mixture is too rich, it may load up the spark plugs. Too much fuel will foul the plugs. If the air/fuel mixture is too lean, the engine may lack power. Having the air/fuel mixture correct for all your load conditions allows you to get maximum horsepower and as many hours of use as possible from a tank of fuel without causing engine damage.
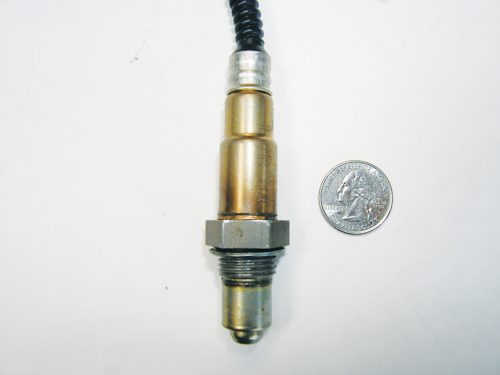
Modern-day tuners are taking advantage of the technology being used to make today’s new boats engines run well: a wide-band oxygen sensor that reads the content of the engine’s exhaust. A wide-band oxygen sensor reads the oxygen (unburned combustible) content of the exhaust to determine the air/fuel
mixture. This new technology is being used by the top teams in NASCAR (NASCAR rules only allow its use on the dyno and during test sessions) and NHRA Pro-Stock, as well as by some of the top Super Cat offshore race teams to help them obtain the almost unreal amount of power needed to win. One unit that gets the job done is the Innovate Motorsports Digital Air/Fuel Ratio Meter with a wide-band oxygen sensor ($350). At that price, any serious boat racer or weekend warrior should have one in his toolbox.
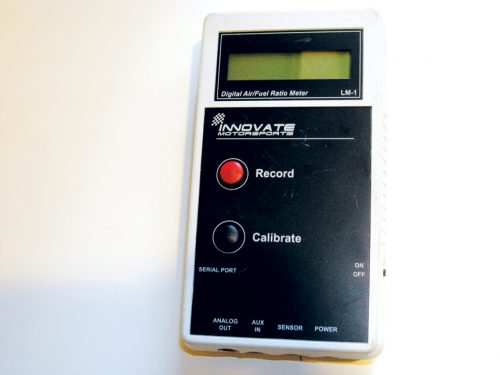
non-pros can afford.
Tuning with a Digital Air/Fuel Meter
A wide-band oxygen sensor can read air/fuel mixtures as rich as 9:1 or as lean as 19:1 (a standard, narrow-band oxygen sensor is only accurate at air/fuel mixtures around 14.7:1). This sensor offers extremely fast
reaction times for the readings, but accuracy can be affected by a high-performance cam or a supercharged engine at light-load/low-rpm testing conditions because of the excess oxygen in the exhaust created by the cam overlap or the supercharger’s blow-through effect. The digital air/fuel meter method requires you to know what air/fuel mixture your engine needs for each driving condition. And since needs differ from engine to engine, ask your builder for the correct formula.
A starting point for air/fuel mixtures for most performance marine engines is 14.1:1 to 13.4:1 at idle, and 14.2:1 to 14.0:1 at cruising or light-load RPM. For power and acceleration, 12.5:1 is ideal for a normal engine. Still, many marine engine builders prefer 11 or 11.5: 1. A high-performance engine with an improved combustion chamber design, such as a Pro-Stocker or a Winston Cup engine (which are being used in some of the top offshore race boats), can use a slightly leaner power mixture of a 13.0:1 ratio. A supercharged engine can use a power mixture richer than 12:1 as a method to help control the detonation that can be caused by higher cylinder pressures.
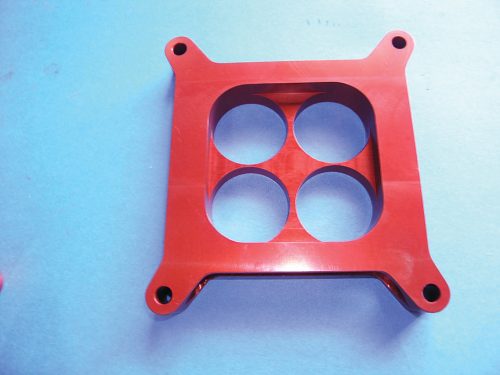
The Innovate Motorsports Digital Air/Fuel Ratio Meter reads the air/fuel mixture in real-time, or samples, and records the air/fuel mixture data at a rate of 12 samples per second over a period of up to 44 minutes; this data lets you tune in the ideal air/fuel mixture curve your engine needs to run at its best.
The performance and replacement marine carburetors sold today have a generic “tune-up,” or jetting unless the carburetor is built for a specific engine and fuel. A carburetor not built and tuned for a specific engine, exhaust system and fuel should supply an air/fuel mixture rich enough for a variety of engines, but this isn’t always the case. If the carburetor is supplying too lean of an air/fuel mixture, the engine will lack power, feel sluggish or overheat, which eventually could cause engine damage. If the carburetor is supplying an air/fuel mixture that’s too rich, the engine may tend to load up, foul the spark plugs, run sluggishly and lack power. The carburetor must have 5.5 to 6.5 pounds of fuel pressure at all rpms and load conditions. If the fuel pressure goes above 6.5 pounds, the carburetor will flood, especially in rough water. If the carburetor floods, you’ll see black smoke coming from the exhaust, or the engine will begin to miss and will run sluggishly until it clears out. Too low a pressure, and the engine will be starved for fuel at higher loads and engine speeds, and engine damage may follow.
One area often ignored is fuel tank venting. If air can’t get into the tank to replace the fuel the engine is consuming, fuel can not get out. The fuel tank must have a vented gas cap or some other type of vent system. Doug Schriefer, from Barry Grant, Inc., points out that for every gallon of fuel used, a gallon of air must be allowed into the fuel tank. If you’re adding power to your boat, you may need to upgrade the fuel tank vent system with larger hoses or additional vents. If the fuel tank is vented by a hose that is routed to an external vent, be sure to route the hose with a loop in it that’s above the external vent. This will keep any water spray from traveling through the hose and into the tank. Also, remember to upgrade the fuel filter/water separator, since the engine is operating in a marine environment and it’s important to keep the fuel injectors dry. Proper fuel pressure/volume and fuel tank venting are important because a marine engine is expected to supply more power for a longer duration over automotive engines, so the fuel pump must be able to supply enough fuel
for the carburetor while the engine is supplying the boat
with full power.
Reading the Air/Fuel Mixture
A lean fuel mixture (too little fuel for the amount of air in the cylinder) can cause an engine to surge or miss at idle and part throttle, stumble on acceleration, overheat, lose power and cause possible engine failure. A rich fuel mixture (too much fuel for the amount of air in the cylinder) can cause an engine to load at idle, foul the plugs and run poorly. There are several different methods used to determine what the air/fuel mixture should be. Always check the air/fuel mixtures under load with a carbureted engine.
First, try reading the spark plugs using an illuminated magnifying glass. This method involves looking at the base of the spark plug insulator (the white part of the plug) for a slight coloring change just above where the insulator comes through the steel case. If the mixture is too lean, it will leave no color, while a too-rich mixture will cause the fuel ring to become more prominent. Over-rich mixtures will give the plug a sooty appearance. Pulling off the header and looking at the color of the exhaust port in the cylinder head and at the first six inches of the exhaust header also is a way to determine the air/fuel mixture, but the header and spark plug color only can show what the air/fuel mixture was at the load condition during the test. In the days of leaded fuel and point ignition, this method worked well, but today the use of unleaded fuels and high-energy ignition systems have made this method much harder because little color is seen on the spark plug, which means you may need to call in an expert. Looking at the spark plug insulator for signs of detonation, which is seen as specks of aluminum, can be an effective way to determine if the ignition timing is too far advanced for the octane rating of the fuel being used.
Next you can try trial-and-error jetting changes. You can do this through timed
acceleration or top-speed runs. Obtaining the correct cruise mixture (the air/fuel mixture the engine operates at while driving under
light-load conditions) is not as easy since it involves jetting the carburetor to get the highest vacuum and then doing trial-and-error runs to get the best drivability. When setting the power and cruise mixtures, it’s always advisable to stay a little rich to avoid engine damage. The idle mixture is set using a tachometer to get the max speed from each idle screw, and then going leaner to get a 20-rpm drop in speed; this is known as the lean/drop method.
After the correct basic engine condition and tune-up is confirmed, the next step is to determine what the air/fuel mixture is at idle through 3,000 rpm. If the cruise mixture is off, first change the jets in order to get the air/fuel mixture correct at the 2,500- to 3,000-rpm cruise range. Then check and set the idle mixture. If the air/fuel mixture is too lean at idle or part throttle, and the idle mixture screws do not provide enough adjustment, the correction may involve enlarging the idle jet. This lean condition at part throttle will cause the engine to miss or stumble. This is a common problem with many of today’s performance carburetors. If the air/fuel mixture is too rich at idle and at part throttle, the idle jet/restriction may be too big and may need to be replaced with a smaller one.
Now take the boat for a run and read the air/fuel mixture using a wide-band oxygen sensor to check the cruise speed air/fuel mixture main jetting, followed by a check of the power air/fuel mixture under load. During a test, you can read and then correct the air/fuel mixture so you can have them correct at idle, cruise and full throttle. If you are buying an engine package that has been dyno-tuned or developed and run on an engine dynamometer, get the engine builder to supply you with the air/fuel mixture it ran on the dyno at both maximum power and cruise-rpm loads. Then be sure they are the same with the engine in the boat. If your engine is being custom built, have the builder record the air/fuel mixture on the dyno with an air/fuel meter unit. Then you can use the recorded data to tune the fuel curve to supply the engine with the same air/fuel mixture used by the builder on the dyno. Many of the engines we’ve checked have had the correct ignition spark timing and air/fuel mixtures for high rpm/wide-open-throttle (WOT) operation, but needed a lot of tuning at low-rpm/part throttle/normal conditions. In most cases, when an engine is run on a dynamometer, only maximum power is checked while using race-style headers with open exhaust (non water-jacketed marine headers), and they supply the engine with air that is not of the same density as the air is when your boat is in the water. In addition, the carburetor probably did not have a flame arrestor or any other type of air cleaner on it.
The air/fuel mixture and ignition timing curves should be corrected for real-world operating conditions of your boat’s engine. Keep in mind the changes in back pressure created by the exhaust system, which may cause the air/fuel mixture to change from its original baseline, reducing engine performance from what was recorded on the dyno. One additional tuning aid is carburetor spacers. An open spacer will move up the powerband in rpm; a four-hole spacer will help with torque in lower rpms, while a
combination spacer such as the Barry Grant PN110075 combines the benefits of both four-hole and open spacers to give you the best of both designs.
Tuning A Fuel-Injected Engine
If the fuel-injection system is programmable, the correction may be as simple as a few computer program changes. But if it’s not, there are still a few tricks that can be done. The easiest way to change the air/fuel mixture on a non-programmable fuel-injection system is to change the fuel pressure or the flow rate of the fuel injectors. As the fuel pressure increases, the fuel flow will be increased, thus making the air/fuel mixture richer. Increasing the fuel pressure has a limited effect on fuel mixtures; if you increase the fuel pressure too much, the fuel injectors windings may not have enough power to open the fuel injectors against the increased fuel pressure. This will cause the mixture to go lean and the fuel injectors to lock up. If you need to increase the fuel pressure more than 15 percent from a base of 40 psi to get a rich enough air/fuel mixture, it may be time to buy larger fuel injectors. Lowering the fuel pressure will cause the air/fuel mixture to go lean, but, again, limit you change to no more than 15 percent; if more correction is needed, smaller fuel injectors may be needed. The fuel supply system must be able to supply enough volume and pressure to maintain at the sustained load conditions seen while running a boat at full power for extended periods of time.